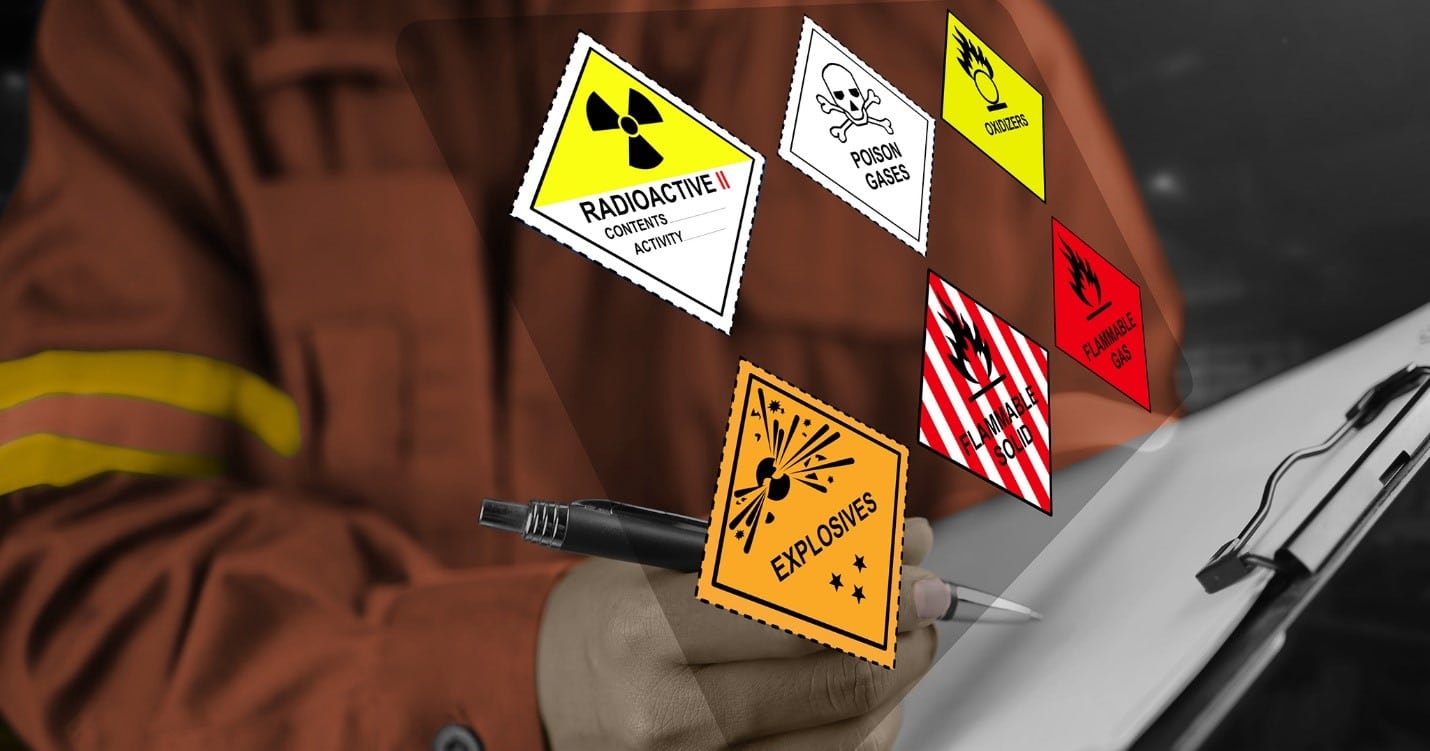
The term hazardous materials, or hazmat for short, may signify chemical suits, gas masks, and decontamination processes. Many people assume hazardous materials are exclusive to very specific industries, like chemical plants or laboratories.
In reality, hazardous materials are all around. They are found in most workplaces, and most people have some in their homes. Household cleaning products like bleach, drain cleaners, oven cleaners, and solvents are all classified as hazardous materials. Even pressurized items like aerosol cans and propane gas canisters are considered hazardous materials.
We all work and live around hazardous materials every day. So, it’s important to know the ABC’s of how to identify and handle them – especially for unfamiliar materials. Even if a hazardous material doesn’t appear to present an imminent threat, improper handling or storage can create a dangerous and potentially deadly situation.
To stay safe in the workplace, or anywhere hazardous materials can be found, it’s critical to keep these three “ABC” reminders in mind.
A – Awareness of Classification Levels
B – Be Informed for Proper Identification
C – Careful Handling, Storage, and Disposal
Awareness of Classification Levels
At the most basic level, a hazardous material refers to any substance or mixture that possesses properties capable of causing harm to human health, the environment, or property under the right conditions. That being said, the term eludes definition to an extent; best practice is to assume that all unknown materials are potentially hazardous.
In the U.S., hazardous materials are officially classified and managed by the Department of Transportation (DOT), working in conjunction with organizations such as the Occupational Safety and Health Administration (OSHA) and the Environmental Protection Agency (EPA).
DOT separates hazardous materials into nine different hazard classes based on their common properties and risks. There are hundreds of different materials that fall into these different categories.
Each hazard class (which has its own subdivisions) includes specific regulations and requirements for packaging, labeling, marking, and documentation to ensure safe transport and storage. Hazard classes also have specific requirements for storage and disposal. While this is not the only classification used in the workplace, it’s the most commonly used one throughout the U.S.
While these classes have unique requirements and regulations, they are not necessarily distinct when it comes to real-world application. Many materials fall into different classifications in different circumstances. For example, gasoline is primarily classified as a Hazard Class 3 due to its flammable nature. At the same time, it can also fall under Hazard Class 6 due to being a toxic substance.
Hazardous Material Classifications
- Class 1: Explosives – This class includes materials that can rapidly release gasses, heat, and energy, causing an explosion. This class is subdivided into six divisions, including mass explosion hazards, projection hazards, and minor blast or fire hazards. All fireworks and ammunition fall under Class 1.
- Class 2: Gasses – This class includes all gasses, including those that are compressed, liquefied, or dissolved. Within this class, there are three divisions: flammable gasses, non-flammable gasses, and toxic gasses. Nitrogen, chlorine, and methane all fall under Class 2.
- Class 3: Flammable Liquids – Class 3 covers all flammable liquids, which are defined as liquids with a flashpoint below 100°F (or 140°F for construction materials). Gasoline, diesel fuel, paints, and certain solvents all fall under Class 3.
- Class 4: Flammable Solids – Class 4 covers solids that can easily ignite. This class is composed of three divisions: flammable solids, spontaneously combustible materials, and materials that emit flammable gasses when in contact with water. Matches, safety flares, magnesium, and white phosphorus are all Class 4.
- Class 5: Oxidizers and Organic Peroxides – Oxidizers and organic peroxides make up Class 5 of DOT’s hazardous materials classification. Oxidizers are substances that facilitate or support combustion, while organic peroxides are thermally unstable and can decompose. Hydrogen peroxide and ammonium nitrate fall under Class 5.
- Class 6: Toxic and Infectious Substances – This wide-ranging class includes materials that are toxic or pose a risk of infection. They are divided up into two types: toxic substances and infectious substances. Pesticides and herbicides, lead compounds, and biological samples are all considered Class 6.
- Class 7: Radioactive Materials – Perhaps the least likely to be encountered on a daily basis, Class 7 includes radioactive materials that emit ionizing radiation and require special handling and transport precautions. It’s divided into three types, based on levels of radioactivity and associated risks. Uranium, plutonium, and other radioactive materials all fall under Class 7.
- Class 8: Corrosive Materials – Corrosive materials are substances that can cause damage to people and materials they come into contact with through chemical reactions. Common examples include acids, bases, and certain cleaning agents. Many household cleaners are Class 8.
- Class 9: Miscellaneous Dangerous Goods – This catch-all category includes a variety of different materials, from lithium batteries and asbestos to other environmentally hazardous substances. Officially, all materials that have anesthetic, noxious, or other similar properties that could cause discomfort are Class 9.
Be Informed of Proper Identification
With nine different classifications and numerous subdivisions within each, it’s difficult for workers to fully understand every type of hazardous material and their unique regulations and requirements.
While certain workplaces that regularly encounter a variety of hazardous materials require more robust identification training across all DOT classes – locations that employ first responders, truck drivers, and shipping personnel, for example – most workers do not encounter many unfamiliar hazardous materials on a day-to-day basis.
Employers at workplaces like these should focus on providing employees with training and quick-reference information on hazardous materials specific to the job site. Being able to quickly identify a hazardous material will help keep employees safe. It can be the difference between maintaining a safe work environment and creating a perilous, and possibly deadly, situation.
Safety Data Sheets (SDS) are the best way to keep employees informed about known hazardous materials that are kept on site. SDS provide quick reference information for each chemical at a workplace, their hazards, and the best guidelines for managing each chemical or material. National Safety Compliance (NSC) offers a training course video to help organizations align with best practices for creating, maintaining, and interpreting SDS. Of course, SDS information is only as useful as it is available. Worksite management and leadership should ensure these sheets are easily accessible at all times.
It’s important to have SDS on-site, so employees know about hazardous materials, but it’s difficult for every employee to memorize them. Furthermore, employees may also encounter new materials from time to time. This is why it’s critical to provide training on how to read chemical labels.
All hazardous materials are required to be properly labeled based on their DOT classifications, and in some cases, their subcategories. These labels include standardized symbols, pictograms, or codes. To the trained eye, this information explains everything a worker needs to know about a particular material. They explain the possible dangers and also provide information on how to manage accidents involving materials, such as an accidental discharge or release. Finally, they also explain the requirements for storage and disposal.
There are additional communication requirements for workplaces that regularly handle hazardous materials. For example, chemical manufacturers need to understand and comply with OSHA’s Hazard Communication Standard. Organizations in these situations should use training materials specific to these requirements.
Careful Handling, Storage, and Disposal
When it comes to handling hazardous materials, the utmost caution should be used every time these materials are on the worksite – even if they aren’t being actively used.
Storage and Labeling
Hazardous materials should be stored in their original containers. Materials like corrosives can breach containers that aren’t designed for them, such as recycled food containers. Do not combine hazardous materials, including for storage.
While the specific storage precautions should be taken based on each classification, most hazardous materials should be stored in dry, cool areas with good ventilation. Incompatible chemicals should not be stored near one another. Many hazardous materials can cause dangerous reactions when combined.
Hazardous materials should be properly labeled. In fact, OSHA requires it: hazardous materials must be properly labeled based on their classification with SDS. Chemicals that are improperly marked or have missing labels should never be used. Workers should alert their manager if any potentially hazardous material is not properly labeled. If a material cannot be identified, it’s best to assume it’s hazardous. It’s a wise idea to take regular inventory of hazardous materials to ensure they are properly stored and labeled.
Careful Handling
Every hazardous material has its own requirements for personal protective equipment (PPE) when being directly handled. Read labels carefully and follow all handling requirements.
Always have PPE like face masks, gloves, and goggles, ready and available for use. These materials should be inspected regularly to ensure they are in proper working order. Any old or defective PPE should be immediately replaced. Replace PPE if it becomes damaged or worn, and do not reuse disposable PPE. Cleaning areas should be clutter-free and regularly inspected. In addition, it’s recommended that workplaces have hand-washing and eye-wash stations installed, in the case of an emergency. For full PPE training, check out NSC’s video kit.
Proper Disposal
While each hazardous material has its own disposal requirements, many have a special disposal process. It’s a safe bet that the hazardous materials at a worksite cannot be simply sent to the landfill.
Certain chemicals must be treated as part of the disposal process. Many cannot be poured down the drain or into the sewer system. Some hazardous materials may even need to be sealed into special containers, whereas others need to be sent to special facilities for disposal.
Hazardous materials should be disposed of according to their specific label instructions and their classification. In some circumstances, there are also local regulations that apply. Before taking steps to discard any material, it’s critical to fully understand the disposal requirements based on the DOT classification and, if applicable, local, state, and federal regulations. To ensure compliance, keep records of all disposals.
Next Steps
There’s no time like the present to ensure a workplace is up-to-date with safety training, particularly when it comes to hazardous materials.
NSC can serve as a partner for organizations looking to establish safety and compliance on all hazardous materials in the workplace. The HAZWOPER: Handling Hazardous Materials DVD outlines critical information regarding such materials, as well as what to do in the case of a spill, emergency or injury.