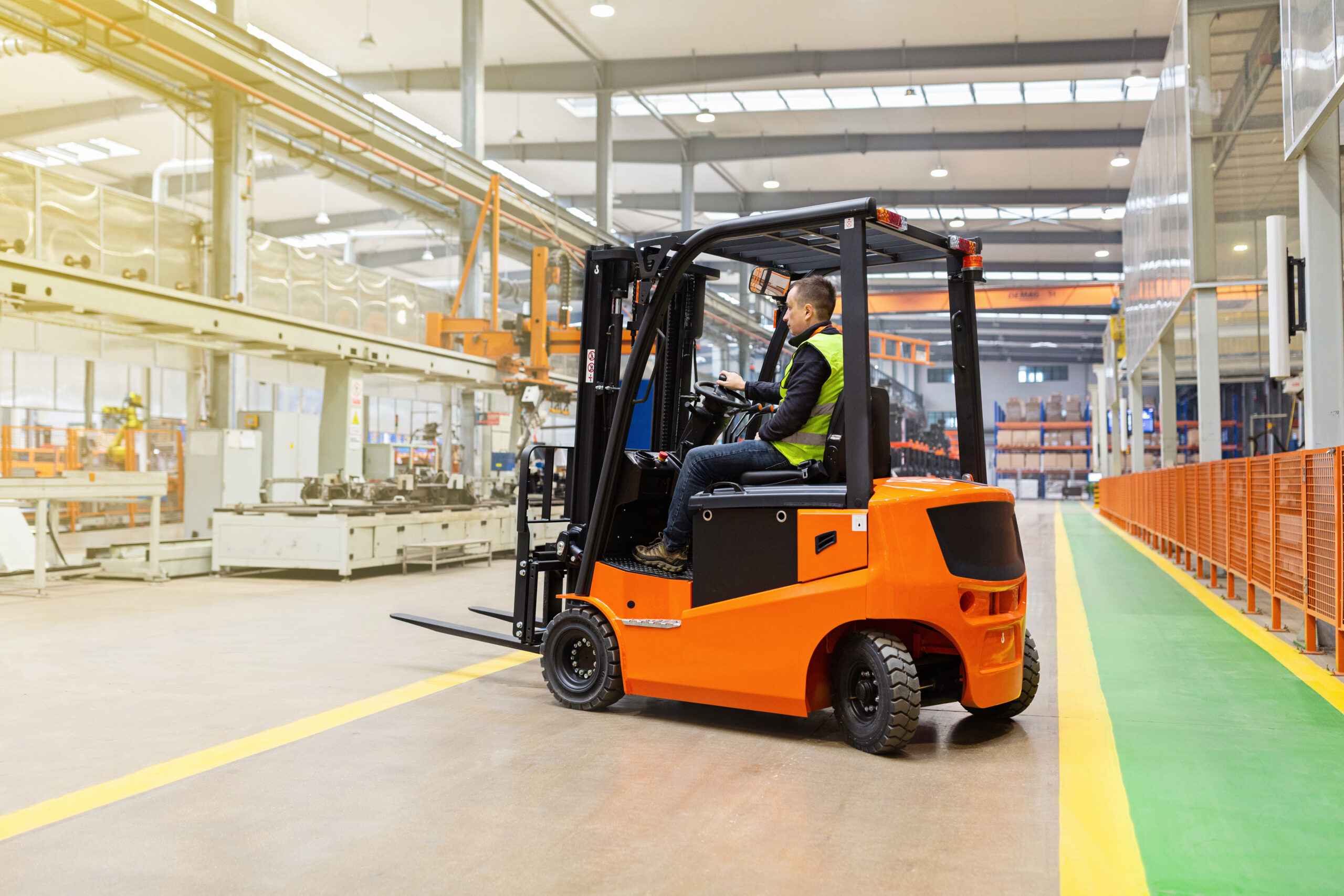
Forklift safety training is essential to fulfill the mission of OSHA: to assure safe and healthful working conditions for all workers. Because forklifts are commonly used in such a broad range of industries such as construction, distribution, manufacturing, retail, recycling operations, and warehousing, the importance of properly training all forklift operators cannot be overstated. Forklifts play a pivotal role in enhancing warehouse efficiency, providing workers with the ability to swiftly move heavy loads as well as transport goods between various locations at a much faster rate. Forklifts can save a significant amount of time and manpower.
Benefits of Using Forklifts
- Enhancing Productivity
- Optimizing Storage Capacity
- Prioritizing Workplace Safety
- Controlling Labor Costs
- Versatility in Handling Materials
While forklifts improve workplace efficiency by enabling quick and safe movement of goods and equipment, they also pose a significant risk of injury. The power and functionality of these machines come with inherent risks. Forklift accidents can lead to serious injuries, damaged property, and even fatalities. Therefore, forklift safety training is essential to assure safe and healthful working conditions for all workers. In fact, OSHA mandates that employers ensure all forklift operators are trained and tested, including a practical evaluation of their skills. Completing forklift training is crucial for individual safety and the safety of fellow workers. Quality training ensures operators are qualified to operate heavy equipment.
Benefits of Proper Forklift Safety Training
- Adherence to OSHA Standards
- Protects Lives
- Mitigate Risks and Accidents
- Improve Operator Competence
- Reduce Downtime and Costs
- Preserve Equipment and Infrastructure
- Empower Emergency Preparedness
- Enhanced Safety and Productivity
- Boost Workplace Morale
In warehouses, distribution centers, and construction sites around the world, forklifts are indispensable tools that streamline operations and boost efficiency. Forklifts improve workplace efficiency by enabling quick and safe movement of goods and equipment. At National Safety Compliance we offer a Forklift Safety Course that satisfies the OSHA requirements for classroom training for forklift operators in industrial, transportation, and warehouse industries. Additionally, we have a Forklift Load Stability Training Course that covers safe forklift operation and how to properly balance their forklift while hauling loads to avoid collisions or loss of control. For the construction industry, our Forklift Safety: Construction Program covers all topics needed to comply with the classroom portion of the training regulations for OSHA forklift certification in construction. As previously mentioned, the importance of properly training all forklift operators cannot be overstated and at NSC we have the forklift training resources you need.
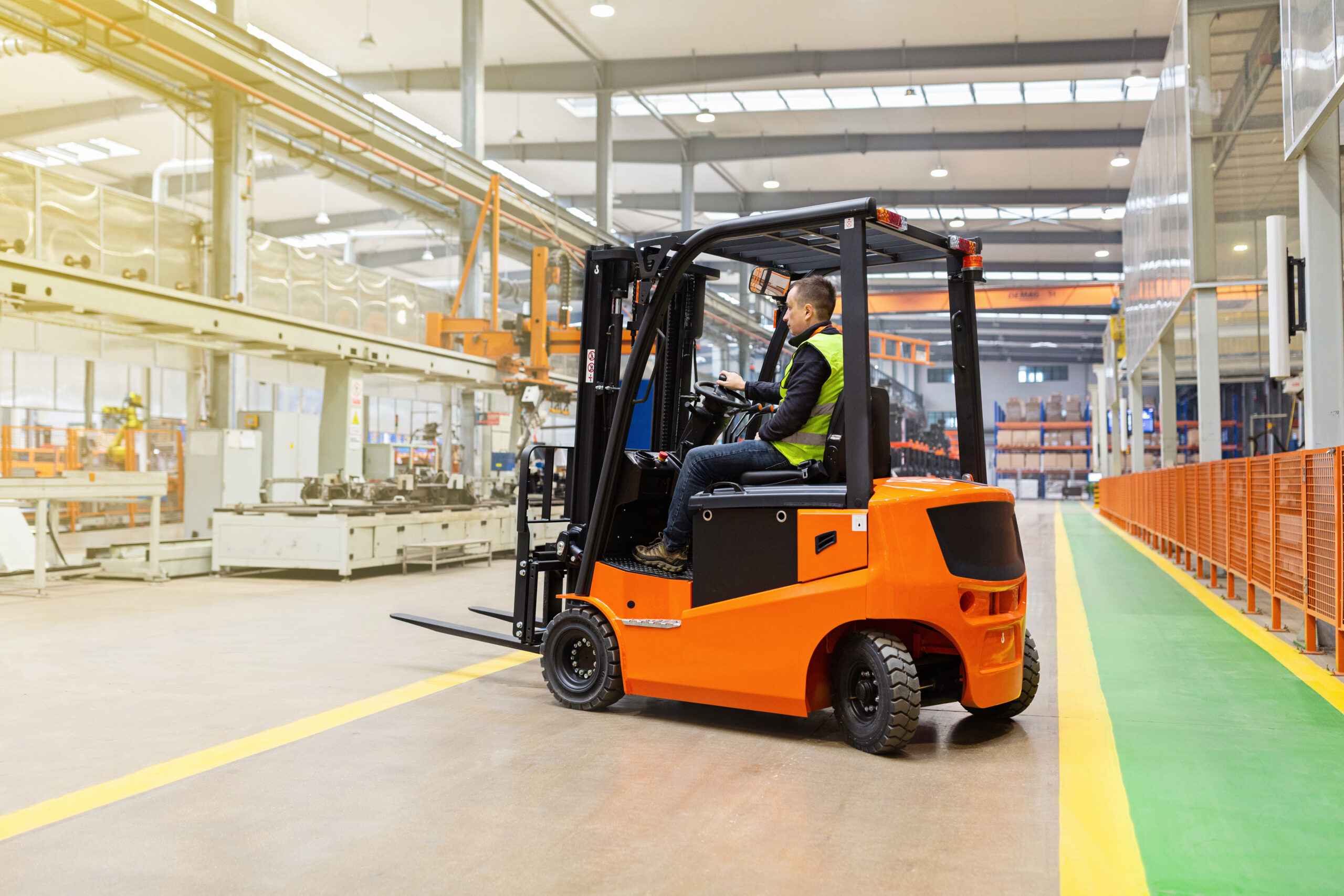