Category: Safety News & Information (English)
From labor-intensive construction jobs to digitally oriented office work, employees may face a daily risk of back injury. Various work hazards, including heavy loads and poor posture, can injure and hinder employees in any field. Workers should be well-informed about the potential health and safety hazards they may encounter daily.
Workers with healthy backs can remain productive and effective in the workplace. NSC offers easy-to-use, OSHA-compliant safety solutions and packages for back safety and proper lifting procedures in any industry.
Back Safety
According to the Bureau of Labor Statistics, more than one million workers suffer a work-related back industry each year. Back-related injuries can occur in manual labor-heavy work environments, such as construction and warehouse work. Workers in any industry may be at risk for back injuries due to poor posture.
A work-related back injury can cause workers to miss time and hurt their productivity. Their place of work may struggle to replace them in the meantime, further hurting efficiency.
Help your employees avoid back injuries and stay productive with our Back Safety Training Course. This training program can educate workers on the causes of back pain, safe lifting procedures, proper posture, and back anatomy to ensure safe transport of both worker and patient.
Lift Safety
Heavy items can be a significant occupational safety hazard. The Bureau of Labor Statistics reported over 86,000 lifting-related work injuries in 2019. Like general back injuries, lift-related injuries can severely inhibit a company’s profitability.
Proper lifting procedures are especially crucial when carrying and transporting heavy loads. Our Back Safety Training Bundle offers comprehensive video training and convenient booklets about safe lifting procedures. Minimize the risk of back injury in your workplace when handling heavy loads with our safety resources.
Additional Materials
Supervisors and managers can utilize various materials to implement safe lifting procedures in the workplace. Video kits and training booklets can serve as comprehensive safety resources, while posters and handbooks can offer convenient, valuable reminders for your workers. Together, these pieces of media can promote and engender a safe, OSHA-compliant environment.
Our Get Some Help Safety Poster is packaged with other back safety materials. Remind your workers to share the load while lifting, moving, and working with heavy items. Display this poster in a visible area, such as the breakroom, for best results.
Rely on National Safety Compliance to build a thorough, OSHA-compliant, and safe work environment. Our Back Safety Training Bundle offers in-depth information on the back-related hazards discussed above. These materials can serve as a valuable resource for new hires. Use these resources to start building a safe workplace today.
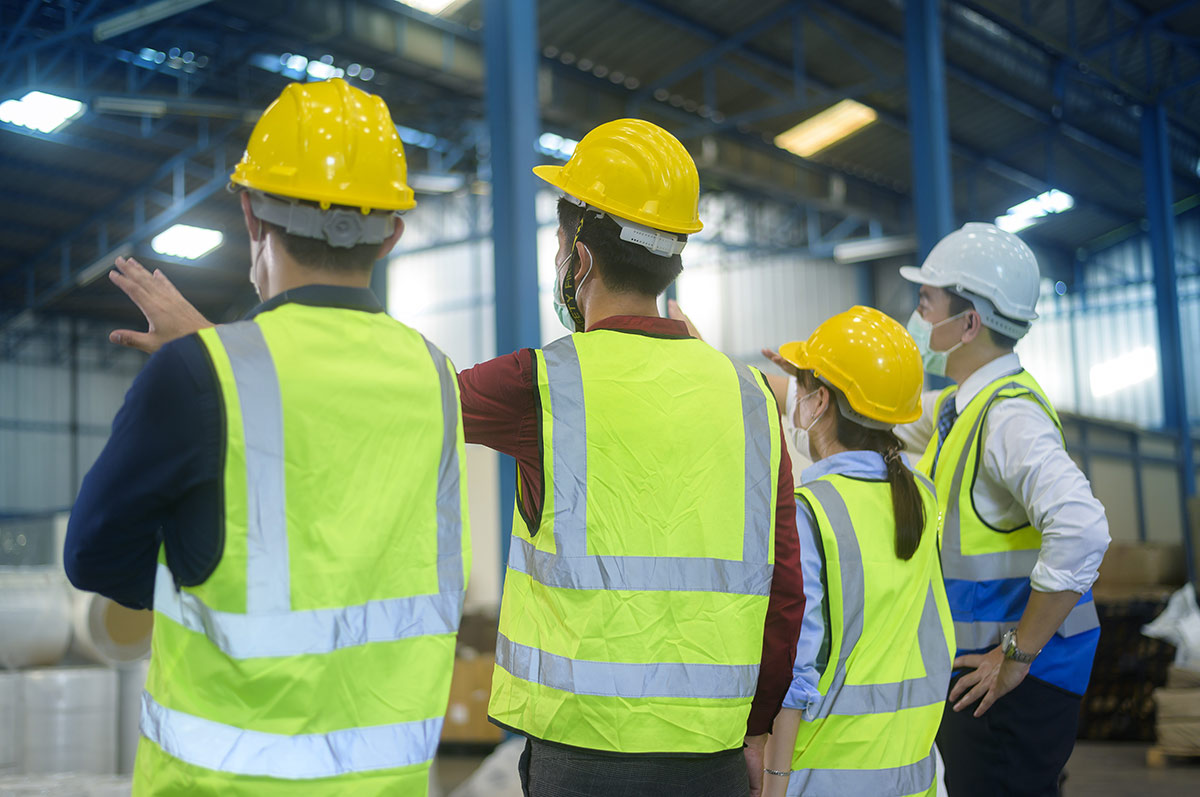
What is the first step in providing a safe workplace? While the safety of workers is our primary focus, having an effective safety orientation training plan in place has value beyond what is self-evident. To begin with, research shows that with consistent orientation, employee morale gets a boost, productivity increases, and staff turnover is reduced. It is vital to get all the necessary information to new employees before they start at the job site.
Effective orientation is part of fulfilling your company’s obligation to a worker’s “right to know”. Don’t make assumptions that a worker has more experience than they actually do. Workers may not know what to expect on the worksite. It is entirely possible that a worker is not familiar with the unique hazards associated with their job. Safety orientation programs provide a lot of information that many workers feel is common sense. But you never know what a new employee does or does not know. Further, exhibiting a commitment to the rights of workers creates positive engagement. It can produce a positive working relationship with your new employees right from the start.
Orientation allows new hires to hit the ground running safely by empowering them with information. You never know what knowledge your new workers bring with them, and your organization has unique processes and procedures to share.
Our safety orientation course is an excellent resource for new hires in any industry. It is designed to foster positive safety attitudes and raise awareness of potential workplace hazards and emergencies. It is a great start for new workers in general industry positions. This training is also suitable for members of management, and supervisors, to train the trainer and for refresher courses.
Safety Orientation Training Class Topic Overview:
- Safety Attitudes and working safely
- Introductory information on these common topics:
- Slips, Trips & Falls
- Back Injuries
- PPE
- Chemicals
- Fire Safety
- First Aid
It is important to remember that some training must start before employees can start performing their tasks. Everyone benefits when workers know the safe way to work from the start rather than waiting to be corrected. Ideally, you need to know whether an employee feels self-sufficient or is at least on the road to self-sufficiency.
Helpful orientation training questions to ask:
- Do you know what’s expected of you?
- How comfortable do you feel reaching out to coworkers with questions?
- Do you know where to go to problem-solve?
- Are you aware of what resources are available to do your job?
Safety orientation is not a checklist. Rather, it is an employee’s first impression of the management system and further of the overall workplace culture. New employees will have expectations about the workplace. An emphasis on safety orientation is vital. Work performance can indicate successful orientation. Thorough orientation may also positively affect the employees’ eagerness to learn and their willingness to contribute to a safe and healthy workplace.
Sometimes a new employee needs additional training or direction. In this case, the employee should be given the opportunity to correct mistakes and receive additional training. Ignoring an employee’s mistakes (intentional or unintentional) puts that employee at risk and may also put others at risk. Supervisors cannot assume mistakes will be self-corrected. Supervisors should review it again if an employee is not following policy or procedure. Under due diligence, supervisors are responsible to correct employees who do not follow standards. Furthermore, disciplinary action may be necessary for that employee. If disciplinary action is required, supervisors must document the situation and proceed by the company directives for the situation.
Retraining is necessary when:
- You have new information or revised best practices
- You spot a deficiency
- An employee experiences an incident (or near miss)
- Company policy dictates retraining (usually according to a set interval)
A study from the National Opinion Research Center at the University of Chicago reported that 85 percent of American workers rank job safety as a number one priority. Your safety orientation program and the importance you give to safety generally communicate a lot about the importance of safety in your workplace. In summary, most new employees are deeply concerned about their safety on the job.
We also offer industry-specific safety orientation training.

Tragically, in the first six months of 2022, twenty-two trench-related fatalities occurred, surpassing the 15 fatalities in all of 2021. These workers fell victim to the deadly hazards present in trenching and excavation work. Prompting the U.S. Department of Labor’s Occupational Safety and Health Administration to launch enhanced enforcement initiatives to protect workers from known industry hazards.
With the hope of saving lives, OSHA enforcement staff is considering every available tool at the agency’s disposal in order to stress the dangers of disregarding federal workplace safety requirements for trenching and excavation work. This will include placing additional emphasis on penalties for trenching and excavation-related incidents. In a worst-case scenario, this may include federal or state prosecution. Therefore holding employers and others accountable when their actions or inactions kill workers or put their lives at risk.
Because of the continuing incidence of trench collapses and loss of life, the agency has determined that these worksites continue to warrant an increased enforcement presence. Employees exposed to potential cave-ins must be protected before the excavation face is in imminent danger of collapse. Furthermore, OSHA believes that there is a potential for collapse in virtually all excavations. OSHA compliance officers will perform more than 1,000 trench inspections nationwide where they may stop by, and inspect, any excavation site during their daily duties.
OSHA Training and Compliance Saves Lives
Trenching and excavation work exposes workers to extremely dangerous hazards. OSHA believes that the rate of deaths and serious injuries resulting from trenching and excavation incidents (mostly collapses) can be significantly reduced if OSHA concentrates resources to effectively engage in trenching and excavation operations through both enforcement and compliance assistance activities.
“Every one of these tragedies could have been prevented had employers complied with OSHA standards,” said Assistant Secretary for Occupational Health and Safety Doug Parker. “There simply is no excuse for ignoring safety requirements to prevent trench collapses and cave-ins, and leaving families, friends, and co-workers to grieve when the solutions are so well-understood.”
“The Occupational Safety and Health Administration is calling on all employers engaged in trenching and excavation activities to act immediately to ensure that required protections are fully in place every single time their employees step down into or work near a trench,” Parker added. “In a matter of seconds, workers can be crushed and buried under thousands of pounds of soil and rocks in an unsafe trench. The alarming increase in the number of workers needlessly dying and suffering serious injuries in trenching incidents must be stopped.”
Trench Shields Unused in Fatal Accident
A recent incident in Texas highlights the dangers of trenching and the importance of following safety standards. On June 28, 2022, two workers suffered fatal injuries when the unprotected trench more than 20 feet deep collapsed upon them as they worked. Trench shields, which could have saved their lives, sat unused beside the excavation.
Trenching and excavation operations require protective systems and inspections before workers can enter. Workers are exposed to serious hazards when trench protection systems are not installed. Furthermore, failing to properly inspect the trench, puts everyone at high risk for injury. These hazards include the risk of being buried under thousands of pounds of soil. Following safety requirements helps protect workers from tragic injuries and possibly death.
Excavation and Trenching Safety Training Includes:
- Overview of OSHA Standard on Trenching and Excavation
- Hazards of trenching and excavation
- Competent Person Roles and Duties
- Safety Precautions
- Access & Egress
- Excavated Materials (Spoil)
- Confined Spaces
- Mobile Equipment
- Surface Crossing
Vital trenching standards require protective systems on all trenches 5 feet deep. In addition, soil and other materials must be kept at least 2 feet from the edge of a trench. Furthermore, trenches must be inspected by a knowledgeable person. Equally important, they must be free of standing water and atmospheric hazards. As well as have a safe means of entering and exiting prior to allowing a worker to enter. Without proper training keeping workers safe is impossible but carefully following OSHA regulations gives everyone the best chance at a safe work environment.
“OSHA stands ready to assist any employer who needs help to comply with our trenching and excavation requirements,” Parker added. “We will conduct outreach programs, including safety summits, in all of our 10 regions to help ensure any employer who wants assistance gets it. The stakes are too important.”

OSHA’s mission is to ensure the protection of workers. Not only striving to prevent work-related injuries but also illnesses, and deaths. The method of achieving this is setting and enforcing standards. OSHA standards include explicit safety and health training requirements. Which ensures that workers have the required skills and knowledge to do their work safely. Likewise, OSHA standards, have prevented countless workplace tragedies. OSHA regulation training reflects the belief that training is essential to every employer’s safety and health program. Researchers conclude that those who are new on the job have a higher rate of injuries and illnesses than more experienced workers. Proper training that meets the requirements will help protect these inexperienced workers from injuries and illnesses. Identically, these standards include providing adequate training, therefore, saving lives and preventing injuries.
Basically, OSHA standards are rules that describe the methods that employers must use to protect their employees from hazards. Furthermore, there are four groups of OSHA standards: General Industry, Construction, Maritime, and Agriculture. General Industry covers the largest number of workers and worksites.
Training in OSHA Standards has Benefits
- Comply with federal and state safety and health requirements
- Recognize and remove hazards from your workplace
- Protect your workers from injury and illness
- Prevent the loss of life at your worksite
- Cultivate informed and alert employees who take responsibility
- Worksite safety as a whole
- Improve employee morale
OSHA regulations help reduce future incidents by identifying potential hazards. It is also vital to regularly review safety procedures with employees. Accurate record-keeping is also important. Clearly, a safer environment keeps your employees at work by reducing the chances of accidents or health problems.
Everyone benefits from proper training. In addition, Workplace safety regulation training makes financial sense. The cost of accident prevention is far lower than the cost of accidents.
Improve the bottom line by:
- Lowering injury and illness rates
- Decreasing workers’ compensation costs
- Reducing lost workdays
- Limiting equipment damage and product losses
Employers also benefit from providing a safe workplace for their employees. This includes knowing that they are complying with OSHA regulations. Fewer injuries result in fewer workers’ compensation claims. Furthermore, a decline in all work-related injuries may occur, which ultimately improves the efficiency and work ethic of employees. Not to mention building an environment at work where employees are physically safe and practice awareness about dangers at work. Additionally, proper training could increase employee retention due to a safe environment for everybody. In short, OSHA training is vital and will help to provide strong morale.
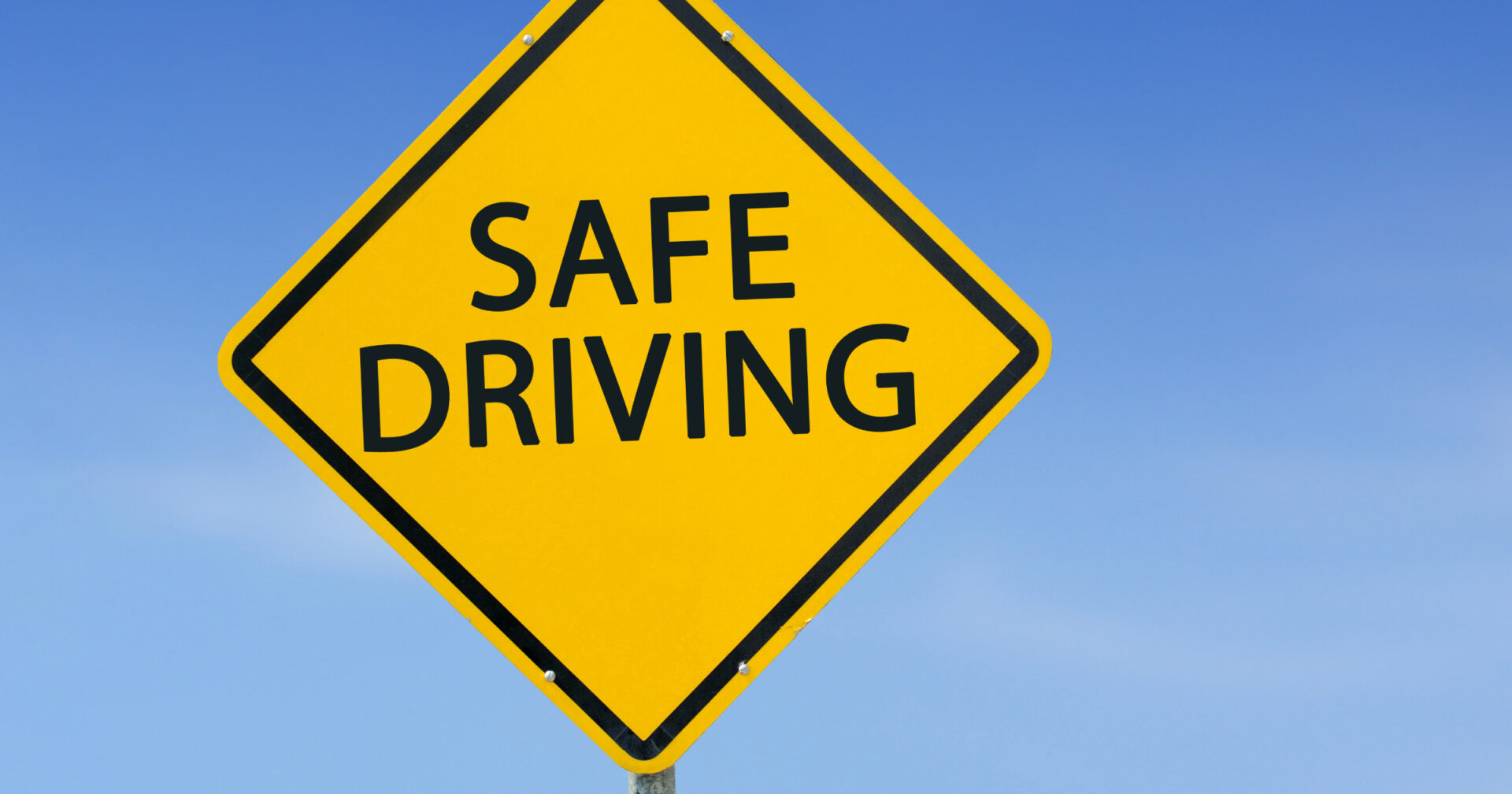
Whether you have one employee on the road or one thousand, promoting a culture of driving safety should always be a top priority for your organization.
The number of trucks involved in fatal crashes has increased 5% since 2016, and a total of 107,000 large truck crashes resulted in an injury in 2020. And while this number still accounts for a low percentage of total vehicular crashes, it’s essential that you’re doing everything you can to ensure your drivers are set up for safety.
Effective safe driver training helps protect your employees and other drivers on the road. This means fewer accidents, as well as reduced overall spending on things like vehicle repairs, insurance premiums, and workers’ compensation premiums. Simply put, investing in driving safety is good business — and one of the best things that you can do for your organization’s fleet.
So, where do you start? We’re sharing some of our top tips for training employees on driving safety, including NSC products that can help you make safe driving a central part of your company culture.
The importance of training employees on safe driving
Educating on and promoting driving safety at your workplace is a must if you have employees operating vehicles on your behalf. We’ve already touched on a few of the reasons why, but here’s a more complete look at the many potential benefits of safe driver training:
- Decreased rates of collisions and traffic violations
- Reduced spending on vehicle repairs and replacements
- Reduced spending on insurance premiums, workers’ compensation claims, and legal costs
- Reduced liability exposure
- Enhanced protection of organizational interests and brand identity
It doesn’t end there. Prioritizing safe driving practices helps you attract and retain the type of employees that you want representing your organization on the road. And the more predictable you make your safety expectations, the less you’ll have to worry about mistakes, miscommunication, and missed opportunities for safer driving.
Building blocks of a safe driving culture
It’s not enough to just cover the basics of highway safety and send your drivers on their way. To be truly impactful, your organization must provide employees with useful, evidence-backed safety training and maintain this training year-round. This requires a purposeful investment of time and resources, which can pay you back tenfold by resulting in fewer driving incidents.
As you look for ways to build or improve on your current safety culture, make sure that you’re incorporating these important building blocks into your strategy.
Tailored training programs
Provide all of your drivers with a comprehensive training program that is industry-specific and based on up-to-date OSHA compliance regulations. Your employees wouldn’t have gotten the job if they didn’t know the basics of safe driving, so the purpose of your training program is to go deeper into what they need to know in regards to the vehicle(s) they’ll be responsible for and the real-life challenges that they might face on the road.
Defensive driving protocols
Safe driving starts with defensive driving. These practices have been instrumental in reducing accident rates and saving the lives of drivers, and we strongly encourage all organizations to utilize NSC defensive driving course materials when designing their training programs.
Qualified trainers
Who you choose to lead your program can make all the difference. Employees tend to learn the most when they’re engaged with the material, and when they are given ample opportunities for interaction. A great instructor, then, is someone who can keep employees interested and open up the floor to participation. Of course, they should also be someone who has a strong grasp on the materials themselves, with the ability to supplement the material as needed whilst also conveying core safety messages with competence.
Appropriate materials
You’re not on your own when it comes to teaching employees about driving safety. We highly recommend the use of NSC Driving Safety Training Booklets and/or the NSC Driving Safety Training Course Video Kit to ensure that your program is based on the most relevant OSHA regulations and requirements. Instructors will still be able to adapt material to include relevant industry use cases, but you’ll know that your bases are covered in terms of the most effective ways to prevent driving accidents and injuries.
Regular reminders
Check-in with your drivers regularly to see if there are any questions or issues about safe driving expectations. This is particularly important if you are adding new types of vehicles to your fleet or making other changes that may impact how your employees drive. You can also hang posters at your workplace that act as casual reminders, such as the NSC Texting & Driving Safety Poster.
Setting your employees up for safety
Your organization’s safe driving program should be specific to the needs of your workforce. It should also include all of OSHA’s basic safe driving practices for employees, which cover things like how to stay focused and how to avoid aggressive driving.
Some of the general guidelines—such as always wear a seatbelt, never drive under the influence of drugs and alcohol, and avoid distractions like texting or talking on the phone—are probably already part of your driving instructions. But some guidelines do require company-specific policies, and will need to be discussed internally prior to training so that you can get everyone on the same page.
- Set a realistic goal for the maximum amount of miles your drivers can safely cover in a day. You should never sacrifice safety in favor of faster logistics, nor should you encourage your drivers to operate a vehicle without being sufficiently well-rested.
- Also necessary is to plan out optimal routes and driving times in advance, providing your drivers with pre-approved instructions for the task ahead.
- Finally, have policies in place for what to do in an emergency situation. This includes what your drivers should do if inclement weather hits and the exact steps they should take if a vehicular incident happens. Being clear about these policies up front takes guesswork out of the equation and eliminates the risk that drivers will unknowingly put themselves or others in additional danger.
Work with NSC to organize effective safe driving training
We’ve made it our mission to help organizations of all scopes and sizes improve their safe driving practices and build a culture of safety for their employees. This includes educating employees and professional drivers at Fortune 100 companies, small business, non-profits, and community service agencies. And we would be happy to work with you, too.
Explore our website to learn about our Safety Training courses, including defensive driving courses. Or contact us directly to discuss options for your organization. We also recommend the use of NSC products, including training materials and course supplements.
Together, we can make safer roads a reality. Optimize your safe driving training program today, and don’t risk another minute of your employees’ safety behind the wheel.

National Forklift Safety Day is June 14
In 2014, the Industrial Truck Association founded National Forklift Safety Day to highlight the safe use of forklifts. An additional motivation was to serve as an annual reminder of the value of training and equipment checks in every industry that relies on forklifts. Forklifts are an essential piece of equipment in many workplaces. For example, warehousing and manufacturing depend on forklifts. These vehicles make work more efficient. However, they can also pose serious hazards to those operating or working near them. With this in mind, we can prevent forklift hazards. Properly trained workers that follow safe practices are the best prevention.
Steps that protect workers on forklifts
- Always wear seatbelts when operating a forklift.
- Never exceed the rated load, and ensure loads are balanced.
- Make sure you have enough clearance when raising and loading materials.
- Watch for pedestrians and observe speed limits.
- Keep a safe distance from the platform and ramp edges.
OSHA’s Powered Industrial Trucks – Forklifts page provides additional ideas for keeping workers safe. Every year, forklift accidents result in an average of 85 deaths and 34,900 serious injuries. Therefore, training is vital in reducing the number of injuries and deaths. All employers have an important role in the safety of their employees.
Some additional safety measures for operating forklifts
- Dress For Safety
- Know Your Forklift
- Conduct Daily Forklift Safety Checks
- Never Operate a Damaged Forklift
- Only Work in Well-Lit Locations
- Never Touch The Mast During Forklift Operations
- Refuel with Caution
- Never Stand Beneath a Forklift Load
OSHA provides specific safety rules for operating forklifts. Therefore, employers are expected to conduct training for all employees working forklifts. Then operators must pass a test and recertify at least once every three years. Finally, ongoing supervision is essential to ensure forklift safety rules are enforced so that employees are kept safe.

Recent headlines remind us of the truth that emergencies and disasters can strike anywhere and at any time. Workers and employers must plan for that possibility. Proper planning before an emergency is necessary to respond effectively. The best way to protect workers is to expect the unexpected. Furthermore, employers must carefully develop an emergency action plan to guide everyone in the workplace when immediate action is necessary. Advance planning helps ensure that everyone knows what to do when an emergency occurs.
What is a workplace emergency?
OSHA defines a workplace emergency as a situation that threatens workers, customers, or the public; disrupts or shuts down operations; or causes physical or environmental damage. Emergencies may be natural or man-made. Many types of emergencies can be anticipated. When they are, it helps employers and workers to plan for unpredictable situations.
With little or no warning an emergency or disaster can strike. Employers and employees should be prepared to deal with such situations. It is important to provide guidance for your staff on how to respond to emergency incidents quickly and efficiently. The best way is to prepare a response before an emergency occurs. Preparing before an emergency event occurs plays a vital role in ensuring employers and employees have the right equipment, know where to go when it happens, and learn how to keep safe.
What type of training do workers need?
It is important to educate workers about the types of emergencies that may occur. As well as training them in the proper course of action. Ensure that all workers thoroughly understand the emergency action plan. This should include many types of potential emergencies. As well as, reporting procedures, alarm systems, evacuation plans, and shutdown procedures. Be sure to discuss any special hazards on-site such as flammable materials, toxic chemicals, radioactive sources, or water-reactive substances.
Topics for worker training:
- Individual roles and responsibilities;
- Threats, hazards, and protective actions;
- Notification, warning, and communications procedures;
- Means for contacting family members in an emergency;
- Any special tasks that workers may be called upon to perform during an emergency (if applicable);
- Evacuation, shelter, and accountability procedures;
- Location and use of common emergency equipment;
- Who is authorized to perform emergency shutdown procedures (if any);
- First-aid procedures;
- Protection against bloodborne pathogens (also see the Bloodborne Pathogens standard, 29 CFR 1910.1030);
- Respiratory protection (also see the Respiratory Protection standards, 29 CFR 1910.134 and 29 CFR 1926.103); and
- Methods for preventing unauthorized access to the site.
Once everyone has completed the proper training, it is vital to hold practice drills as often as necessary. It is also a good idea to include outside resources, such as fire and police departments, in the practice drills whenever possible. After each drill, employers should evaluate the effectiveness of the drill. It helps to identify the strengths and weaknesses of the plan. Employers should constantly be looking for ways to improve the plan. The next question to consider is how often to train workers? It is a good practice to review the plan and require annual training on the plan.
Also conduct training after:
- Development of the initial plan;
- The hiring of new workers;
- Introduction of new equipment, materials, or processes into the workplace that affects evacuation routes;
- Reassignment of workers or changing their job duties;
- Change of layout or design of the facility; and
- Revision or updating of emergency procedures.
Finally, an important decision is selecting a responsible individual to lead and coordinate the emergency plan and evacuation. It is critical that workers know who the coordinator is. Furthermore, they must understand that the coordinator has the authority to make decisions during emergencies. Employers should consider making available an emergency communication system to serve as the means of notifying workers of an emergency. It may also assist in contacting local law enforcement, the local fire department, and others. Employers should also provide an updated list of key personnel such as the plant manager or physician, in order of priority, to notify in the event of an emergency during off-duty hours.

Each year, more than 650 people succumb to a heat-related illness. According to the Center for Disease Control, heat-related illnesses are one of the deadliest weather-related health outcomes affecting Americans. However, the most devastating part of this equation is that all deaths from heat-related illnesses are preventable with the proper training and safety tools.
Learn here how to keep yourself and others safe while working in the heat.
What Are Heat-Related Illnesses?
Heat-related illnesses are those that occur after exposure to abnormally high or prolonged amounts of heat and humidity. There are three primary types of heat-related illnesses, including:
- Heat Cramps: A condition causing painful and often intense cramps or spasm of the muscles, usually after exercise or extreme exertion.
- Heat Exhaustion: Resulting from a loss of water and sodium in the body, heat exhaustion causing a range of bodywide symptoms. Left untreated, this can lead to heat stroke.
- Heat Stroke: The most severe form of heat-related illness, heat stroke can cause coma, seizures, and altered mental status. If left untreated, heat stroke can lead to death.
Learn the Signs of Heat-Related Illnesses
Identifying the signs of heat-related illnesses like heat stroke or exhaustion should be a crucial part of your safety strategy. A few common symptoms of heat related illnesses include:
- Headache
- Muscle aches or cramping
- Fatigue
- Dizziness
- Fainting
- High body temperature
- Skin that is red, hot, and dry (no sweating)
- Rapid pulse
- Nausea, with or without vomiting
- Confusion or altered mental state
Companies in industries that require employees to work outdoors or inside high-heat environments should implement training programs. Excellent examples of training materials include The National Safety Compliance’s Heat Stress Training Course Video Kit and Heat Stress Training Booklets.
Use Signage to Refresh Employees on Heat-Related Illnesses
Using signage like this Heat Stress Safety Poster can help keep heat safety at the forefront of an employee’s mind. Place posters and other visual aids in high-traffic areas like break rooms, offices, and workshops. In addition, include signage in areas where heat-related illnesses are more likely to occur.
Recognize Those Most at Risk for Heat Stress
Certain people are at a greater risk for heat-related illness. Learning to identify them can help prevent many tragedies from occurring. People who are at greater risk include:
- Anyone over age 65 or under age five
- People with autoimmune disease, heart disease, or breathing problems
- Those who are overweight
- People taking certain medications
- Anyone who drinks heavily
- Those exposed to high heat for extended periods
- People recovering from illnesses
Know the Precautions to Take
A comprehensive overview of precautions to take during heat waves and inside high-temperature areas is crucial to your training efforts. The best heat stress training courses will include this information. To stay safe in high-heat environments, you should:
- Wear loose, lightweight clothing
- Drink plenty of water
- Avoid dehydration beverages (like alcohol, coffee, or energy drinks)
- Take frequent breaks in cooler areas (preferably in air conditioning)
- Apply sunscreen when working outdoors
- Use a buddy system, so nobody works in the heat alone
- Try to avoid working during the hottest parts of the day, if possible
- Avoid hot and heavy meals that can raise your internal body temperature
- Use sports drinks to replace electrolytes lost when sweating
Companies should keep a close eye on the weather during warmer months to be aware of dangerous heat wave events. If possible, people usually working outdoors should stay home during these events. However, if staying home isn’t possible, companies should implement additional precautions like more frequent breaks or shorter work days until the heat wave has passed.
Additional Precautions for Working Around Fire or Electricity
People working around electricity, fire, or flammable materials should undergo additional heat stress and general safety training. Individuals working around these materials are more prone to injury and should be given training on:
- ARC flash training
- Burn prevention and treatment
- Preventing, recognizing, and treating electrocution
- Handling hazardous or combustible materials
- Preventing contamination
You can also find valuable training resources for individual sectors or industries, such as welding. Certain professions have industry-specific training they need to perform their jobs safely and effectively.
What to Do If Someone Is Experiencing Heat Stress
If someone is experiencing heat stress, the most critical thing is to call 9-1-1 right away. While waiting for emergency first responders to arrive, try moving the affected individual to a shady or cool area. Do not dump cold water or offer ice water to drink if someone is experiencing heat stress, as this could cause the body to go into shock.
Companies should include first aid training as part of their onboarding procedures so everyone understands what to do should a heat-related event occur. An excellent education option is this First Aid Safety Training Course Video Kit, which includes segments on:
- Basic first aid procedures
- Proper handling of bloodborne pathogens
- Treating cuts, scrapes, and burns (including chemical burns)
- Broken bones and fractures
- Heat stress events (including heat exhaustion and stroke)
- Choking emergencies
- CPR
The National Safety Compliance has the tools and information you need to keep yourself and others safe from heat-related illnesses. For more information, visit our heat stress safety product page. If you need help assessing your safety training needs or have questions, fill out our online contact form, and we’ll be in touch as soon as possible.

Tragedy Strikes
Electricity is a serious workplace hazard. It exposes employees to electric shock, electrocution, burns, fires, and explosions. Electrical safety is important in every workplace.
Electrical hazards killed four workers in Missouri and Kansas in five months in 2021. In Missouri, an electrical contractor died replacing light fixtures, and another worker while cleaning a pig barn with a pressure washer. In Kansas, a worker perished while doing heating and air conditioning work, and a contractor lost his life climbing a pole. Their circumstances differ. However, the cause of death is the same – electrocution.
Nationally, the Bureau of Labor Statistics reports a 3.75 percent increase – 166 workplace deaths related to electrocution – in 2019 over the previous year. Additionally, from 2018, through 2021, OSHA investigated 12 electrical-related deaths in Missouri and Kansas. Meanwhile, the U.S. Department of Labor is alerting all employers to review safe electrical work practices with their employees in response to a nationwide increase in workplace deaths by electrocution.
One reason these statistics are so tragic is that these fatalities could have been avoided.
“Recent tragedies in Missouri and Kansas are reminders of the danger of electrical exposures in the workplace,” said OSHA’s Acting Regional Administrator Billie Kizer in Kansas City, Missouri. “OSHA’s electrical standards are designed to protect employees from electric shock and electrocution. Employers should implement safety and health programs, and are required to train workers on identifying hazards and use required protective measures to ensure all employees end each workday safely.”
OSHA standards cover electrical hazards in many different industries. These standards cover general industry, the construction industry, marine terminals, longshoring , and also shipyard standards design, Safety Standards for Electrical Systems, Electrical Safety-Related Work Practices Standards, and Electrical Safety Requirements for Employee Workplaces.
How do electrical injuries happen?
Electricity travels in closed circuits, normally through a conductor. But sometimes a person’s body mistakenly becomes part of the electric circuit. This can cause an electrical shock. Shocks occur when a person’s body completes the current path with either both wires of an electric circuit, one wire of an energized circuit and the ground, a metal part that accidentally becomes energized, or another “conductor” that is carrying a current.
When a person receives a shock, electricity flows between parts of the body or through the body to a ground or the earth. What is the best way to protect employees from electrical hazards? Most electrical accidents result from one of the following three factors: unsafe equipment or installation, unsafe environment, or unsafe work practices.
5 ways to prevent these accidents are through the use of:
- insulation,
- guarding
- grounding
- electrical protective devices
- safe work practices.
Electrical accidents are largely preventable through safe work practices. Examples of these practices include the following: de-energizing electric equipment before inspection or repair and keeping electric tools properly maintained. Additionally, exercising caution when working near energized lines and using appropriate protective equipment are both vital practices. When working on electrical equipment there are some basic procedures to follow.
Basic procedures to follow
- de-energize the equipment
- use lockout and tag procedures to ensure that the equipment remains de-energized
- use insulating protective equipment
- maintain a safe distance from energized parts.
Electrical safety training is critical. All employees should be thoroughly familiar with the safety procedures for their particular jobs. Moreover, good judgment and common sense are vital to preventing electrical accidents.

Injuries Cost Businesses however, Safety Programs Save Money
Have you ever thought about how much a workplace injury costs your business?
OSHA’s $afety Pays tool is an online calculator. This tool uses current data on workplace injury costs to calculate the direct and indirect costs to your business. This helpful resource emphasizes the importance of having an organized safety program. The results may surprise you.
Whether you are a small start-up, an established business, or just ready to start managing safety in a more responsible way, there are some simple steps you can take. Completing these steps will give you a solid base to begin your safety program.
10 Simple Steps
- Lead by example
- Establish safety and health as core values
- Implement a reporting system
- Provide training
- Conduct inspections
- Collect hazard control ideas
- Implement hazard controls
- Address emergencies
- Seek input on workplace changes
- Make improvements
Keeping the Safety Program a Priority
Communicate to your workers that making sure they go home safely is the top priority. Assure them that you will work with them. Proactively find and fix any hazards that could injure employees. Practice safe behaviors yourself. Make safety part of your daily conversations with workers.
Develop and communicate a simple procedure for workers to report all injuries, illnesses, and incidents. Furthermore, hazards or safety and health concerns should be easily reported without fear of retaliation. Additionally, it is profitable to provide an option for reporting concerns anonymously. It is especially important to include near misses/close calls.
Train workers on how to identify and control hazards in the workplace. Inspect the workplace with workers for the purpose of asking them to identify any activity, piece of equipment, or materials that concern them. Also, be sure to use checklists to help identify problems.
Ask workers for ideas on improvements and follow up on their suggestions. Coupled with providing time to research solutions. Assign workers the task of choosing, implementing, and evaluating the solutions they come up with. Whenever possible, identify foreseeable emergency scenarios. Then, follow up by developing instructions on what to do in each case. Finally, meet to discuss these procedures and post them in a visible location in the workplace.
Finally, set aside a regular time to discuss safety and health issues, with the goal of identifying ways to improve and effectively implement the program.