Category: Safety News & Information (English)
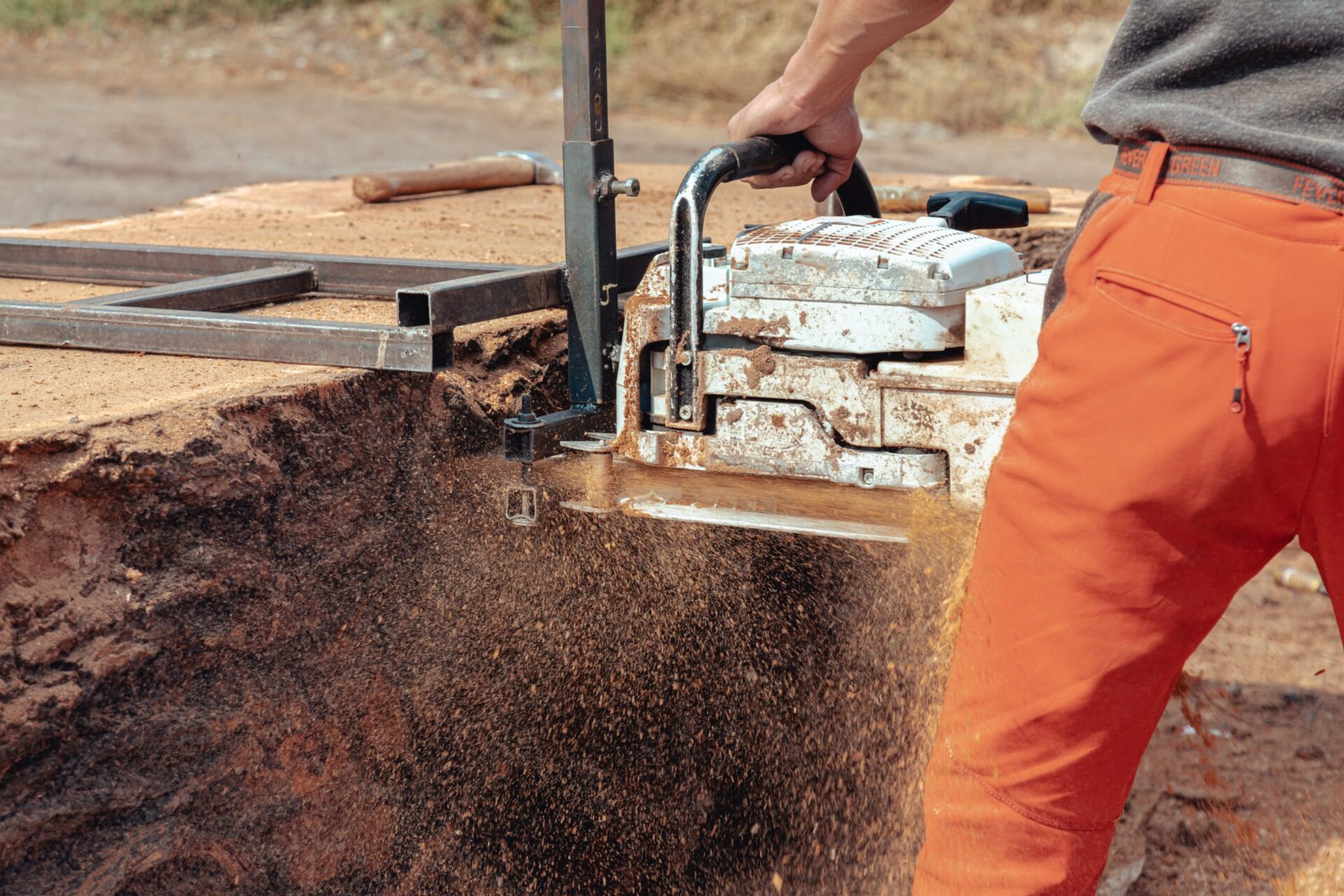
Heat illness is preventable, even though Millions of U.S. workers are exposed to heat in their workplaces. Every year, thousands become sick from occupational heat exposure. Some cases are fatal. Most outdoor fatalities, 50% to 70%, occur in the first few days of working in hot environments. This is because the body needs to build a tolerance to the heat gradually over time. Lack of acclimatization is a major risk factor for fatal outcomes. However, illness from exposure to heat is preventable.
Since 2011, a focus on keeping workers safe while working in the heat has made great progress. However, there is still significant work to be done. OSHA’s Heat Illness Prevention campaign comes down to three keywords: Water. Rest. Shade.
New employees will need time to build a tolerance to the heat. Especially during their first few days in warm or hot environments. Workers who are new to working in warm environments are at increased risk of heat-related illness. Especially during a worker’s first few days, absolutely all symptoms should be taken seriously.
Workers who develop symptoms should be allowed to stop working. They should receive an evaluation for possible heat-related illnesses. Employers should encourage new workers to consume adequate fluids (water and sports drinks), work shorter shifts, take frequent breaks, and quickly identify any heat illness symptoms
Heat-Related Dangers
Every year, dozens of workers die and thousands more become ill while working in extreme heat or humid conditions. There is a range of heat illnesses and they can affect anyone, regardless of age or physical condition.
Employers should recognize that not all workers tolerate heat the same way. Therefore, workplace controls should focus on making jobs safe for all employees. Workers should receive training about personal factors that can make them more susceptible to heat-related illness. When in doubt, workers should talk to their healthcare provider about whether they can work safely in the heat.
Responsibility to Protect Workers
Under OSHA law, employers are responsible for providing workplaces free of known safety hazards. This includes protecting workers from extreme heat. An employer with workers exposed to high temperatures should establish a complete heat illness prevention program including these 6 steps to prevent heat illness.
- Train workers in prevention
- Provide workers with water, rest, and shade
- Allow new or returning workers to gradually increase workloads
- Take more frequent breaks as they build a tolerance for working in the heat
- Plan for emergencies
- Monitor workers for signs of illness
We offer safety training that includes keeping workers safe in heat-exposed jobs. This covers what workers need to know – including factors for heat illness. As well as, adapting to working in indoor and outdoor heat and protecting workers. Furthermore, it includes recognizing symptoms and first aid training. Our heat illness training materials meet OSHA workplace standards.

Video safety training is the most cost-efficient method of training for today’s companies. Clear training is vital to keeping workers safe on the job. Similarly, a solid knowledge of safety practices relevant to the job is crucial. According to elearningindustry.com, a learner will only remember 10% of text content. Typically, they remember 65% of visual content. However, we remember 95% of audio-visual content.
Because it works, Video Training is here to stay. As a result, it is the new normal. Videos keep learners’ attention. Equally important, people enjoy videos. Actually, research confirms videos help companies train smarter.
OSHA-compliant training is essential for today’s businesses. The need for consistent material is abundant. Likewise, the safety of our employees depends on it. Additionally, in today’s world flexibility is necessary. Furthermore, the ability to include on-site and remote workers is a benefit of this type of training.
Video-based learning is quickly becoming a basic training need. In essence, employees benefit from watching a video. In fact, according to Forrester Research, employees are 75% more likely to watch a video than to read materials. Video training ensures uniformity of information presented. This is essential for safety in the workplace.
10 reasons to choose video-based training:
- Videos are persuasive
- Videos are effective and engaging
- Increased information retention
- Video supports teaching at the moment of need
- It is flexible and accessible
- Addresses the different learning styles
- Video is a cost-effective solution
- Video training boosts work productivity
- Videos can extend training across internal and off-site employees
- Video training ensures consistency in safety training materials
As shown above, Safety training must be uniformly taught. In addition, consistency in training employees according to OSHA standards is critical. This should not be taken lightly. With this in mind, we offer OSHA-compliant materials that cover everything you need for training compliance.

In some states, the month of May is Safe Jobs for Youth Month. Communities benefit greatly by having teens in the workforce. Employment teaches young people important skills, including responsibility, timeliness, honesty, teamwork, resourcefulness, communication skills and confidence.
Many states have departments of labor that work with employers and parents to help keep young workers safe and healthy. Youth will benefit from learning these valuable life lessons. Fast food, grocery stores, general retail, and lawn care are the most popular jobs for teenagers. Most states have laws that restrict the age, number of hours, and occupations youth can work during the school year and in the summer.
Tips for Youth Employers and Parents
Youth employment safety starts at home. It is also an important responsibility of employers. It’s vital for the parents along with employers of young workers to make sure that young employees know how to be safe. Teens need to be able to identify potential safety risks. Together, we can work to keep young employees safe in the workplace. At the same time they will gain valuable skills to guide them into the future.
Here are a few key things to consider as kids head off to work:
- Be aware of how youth employment laws impact different ages, particularly 14-15 year old youth workers.
- Know the name of your child’s employer, as well as any location he or she may be working.
- Look up the law on acceptable work hours for youth and be a part of the discussion when determining your child’s schedule. Often, this information is included on State Labor Law Posters.
- Do some research and find out if the employer stresses safety on the job. Do they provide workers’ compensation insurance and if so, who is their carrier?
- Find out what specific types of work your child will be doing and verify that those tasks are allowed under youth employment laws.
- Know the potential hazards of the work being done and ensure that proper training will take place to ensure your child’s/ employee’s safety.
Our communities benefit as we all work together to prepare our young people to be valuable assets while also being safe in the workplace.

Even in the safest workplaces, accidents happen. Slips, trips, and falls account for over one-third of all workplace injuries across all industries. Fortunately, these types of injuries are also some of the most preventable — if you have the right procedures and fall protection gear in place.
Fall protection is mandated when workers are exposed to different heights, which vary by industry:
- General workplaces: Four feet
- Shipyards: Five feet
- Construction: Six feet
- Longshoring operations: Eight feet
- When working above dangerous machinery: Always, regardless of potential fall distance
And this isn’t just in reference to people working above ground: even workers at ground level are at risk when floor openings are present.
There are many different types of fall protection equipment, both temporary and permanent, that can keep workers safe in these scenarios. Here’s a rundown of the main types of fall protection used today, along with some resources for learning more about each.
Scaffolding
Workers use scaffolding to temporarily get access to buildings or machines for construction, repair, or maintenance. These temporary platforms feature planks of different lengths and widths designed to hold both workers and materials.
There are a number of OSHA regulations for scaffolds to help ensure they’re strong and stable enough to support workers and materials. Here are the highlights:
- Scaffolds must support their own weight and at least 4 times the maximum load that will be applied to it.
- Platforms must be at least 18 inches wide, and they must include guardrails or fall arrest systems for workers.
- Space between platforms and uprights can’t be more than one inch wide
- Both supported and suspended scaffolds have their own unique requirements.
- Shore and lean-to scaffolds are prohibited.
- For scaffolds 10 feet or higher, workers are required to use fall protection equipment like a personal fall arrest system or a guardrail system.
Other Types of Fall Protection
For some jobs, like window washing or HVAC repair, it would be unreasonable to build scaffolding to protect workers at elevation. There are a number of other types of fall protection gear, including:
- Guardrails. Guardrails can be temporary or permanent, but both keep workers away from dangerous edges or holes.
- Fall arrest system. A fall arrest system stops a fall, and consists of a body harness, anchor, and a lifeline connecting the two. A fall restriction system is similar, but often includes another component, like a bosun’s chair, that serves as a work positioning system.
- Travel-restraint system. These systems keep workers from getting too close to an unprotected edge. In a travel-restraint system, a worker is attached to a body harness, which connects to a lanyard that may move freely along an anchored line — keeping the worker in the safe zone.
Best Practices for Keeping Workers Safe
Regardless of your industry, there are a number of measures you can take to prevent slips and trips — whether your workers are routinely high above the ground (or not). They are:
- Keep work areas clean, dry, and free of debris.
- Use railings, floor covers, and toe boards to prevent workers from falling into holes.
- Install guardrails and toe boards against open-sided platforms.
- Ensure rooftop safety by using temporary or permanent guardrails and anchors for personal fall protection.
- Train your team on fall protection standards (start with our fall protection video kit, booklets, and regulations manual).
National Safety Compliance provides safety training courses to help you stay compliant and stay safe in the workplace. Check out our range of safety training products here.

It’s Injury Prevention Month, so we thought it would be helpful to put together a list of ways you can keep your employees safer in the workplace.
There were 4,764 workplace injuries that resulted in death in 2020. Nearly half of these occurred in the transportation, material moving, and construction and extraction occupations. Beyond that, there were 2.7 million non-fatal workplace injuries in the United States during 2020. While these numbers have decreased over the past few years, workplace safety is still a prominent concern.
To focus on injury and fatality prevention in your workplace, there are several different categories of solutions you should have in place. Here are the ones we believe are the most important.
Provide General Safety Orientation
What your employees don’t know can hurt them. Your safety orientation program will look different depending on your industry, regulations in your locale, and your workers’ roles, but it’s a must-have for companies that want to remain compliant, reduce turnover, and foster the kind of workplace culture that leads to both a strong reputation and bottom line.
Check out our array of Safety Orientation Training Courses, available in both video and booklet formats for different learning environments.
Focus on Slips, Trips, and Falls
While some workplaces inherently present more dangerous hazards than others (think heavy machinery inside a manufacturing facility, or on a construction site), no workplace is exempt from the hazards of slips, trips, and falls — not even a seemingly benign office environment. Get your team up to speed on these common hazards by having them participate in a Slips, Trips and Falls Training Course.
Use Posters and Visuals
There’s no better way to keep safety top-of-mind than to provide visuals around your workplace. Safety posters can serve a variety of purposes, from helping employees recall a specific process or steps, to helping to motivate or inspire changes in behavior. Some posters or safety signs are required by law in certain workplaces. Signage in your workplace can dramatically help with knowledge retention after your employees complete a training course, as well — serving as a valuable way to protect your investment in employee safety education.
Offer Industry-Specific Information
While generic safety education will certainly help prevent injuries in the workplace, there’s no substitute for expert, industry-focused training. This is especially true for construction, manufacturing & warehousing, and healthcare, since these are the main industries where workers suffer the highest number of injuries and fatalities on the job. They’re also some of the most highly regulated industries, meaning you could face hefty fines if you aren’t up to speed on compliance requirements.
Have an Emergency Plan
No matter the type of business you operate, emergencies happen. These include natural disasters, chemical and HAZMAT accidents, and even workplace violence. Do your employees know what to do in the event of any of these disasters? Are you aware of which types of emergencies are most likely to occur at your place of work? Outline an emergency action plan that states the steps your team members should take in the event of each type of emergency. Ready to prevent injuries within your workplace? NSC makes training easy.

Both OSHA and ANSI have standards in place for protecting workers who operate dangerous machinery — and if your industry is impacted by such regulations, you’re likely well-aware of the statistics about amputations, lacerations, and other injuries that come from improper machine guarding. Still, it’s worth noting that improper machine guarding was one of the top OSHA citations of 2021, and has held a place on this list every year for the past decade.
So if machine guard safety isn’t on your list of priorities, it should be. Let’s take a look at some of the safety standards surrounding machine guarding, then we’ll follow up with some actionable steps you can take today to improve compliance and avoid mistakes in the future.
OSHA Standards for Machine Guards
OSHA Standard 1910.212 covers general machine guarding requirements for all machines. The standard defines machine guarding and gives examples (including barrier guards, two-hand tripping devices, and electronic safety devices).
While you can read the full standard at the link above, here are the main points:
Affixing guards to machines. Whenever possible, a guard should be affixed to the machine, and the guard should never cause a hazard in itself.
Point of operation guarding. The “point of operation” is the area where someone processes a material. For example, the point of operation on a table saw would be the table area around the exposed blade. Points of operation must be guarded so that the operator doesn’t have any of their body parts exposed to hazards while operating. While not all machines require point of operation guarding, here are a few that do:
- Shears
- Power presses
- Milling machines
- Portable power tools
- Guillotine cutters
- Power saws
- Jointers
- Forming rolls and calendars
Barrels, containers and drums have specific guidelines for enclosures, as well as exposed blades on fans. Fixed machinery also should be anchored for added safety.
How to Avoid Mistakes with Machine Guarding
There are a number of steps you can take to avoid mistakes with machine guarding and keep your workplace safe and incident-free. Here are the top tips for setting your work environment and machinery up to ensure worker safety.
Check all of your equipment.
Every machine, from the years-old hydraulic press in the back of the shop to the brand new plastic injection molding machine you just purchased, needs to be checked against OSHA machine guarding standards. It’s surprisingly common for even brand-new machinery to lack proper guards and shields — so run a complete audit of all of the machines in your work area and make a plan for updating or upgrading those that don’t include proper guards.
Replace faulty or outdated machine guards.
After you’ve audited your workplace machinery for safety, replace or add guards to machines that didn’t meet the standard. If you’re unsure of how to do this, check out OSHA’s machine guarding resource. While it’s not comprehensive, this tool does cover some of the most common hazardous machines (saws, presses, and plastics machinery) and ways to employ guards to protect the people who operate them.
When replacing guards, be very careful to use the right materials. One of the most common mistakes is failing to use the right materials, which can render the guard ineffective or make it even more dangerous.
Know the types of machine guarding, and which applies to each machine.
Not all machines need the same types of guarding, and some require unique considerations. Here are some of the main types of machine guarding and what they’re used for:
- Fixed guards. Fixed guards are permanent parts of a machine that are usually very simple, like a barrier guard or a screen. These guards provide maximum protection without requiring much maintenance, although they can inhibit visibility in some cases.
- Interlocked guards. An interlocked guard is a mechanical device that automatically turns a machine off when the guard is removed or opened — like the door of a microwave. Interlocked guards are very effective but can present hazards when they’re removed for maintenance.
- Adjustable guards. Adjustable guards are exactly what they sound like: guards that expand or contract to accommodate different shapes and sizes of materials. Because they require manual adjustment, however, workers must be specifically trained on how to use these guards in order for them to be effective.
- Self-adjusting guards. A self-adjusting guard begins in a “rest” position and only moves out of the way to allow a material to pass through the danger zone before returning to a guarded position. A retractable plastic guard on a circular saw is an example of a self-adjusting guard.
Don’t remove machine guards.
Some workers may be inclined to remove guards to speed up their work or make it easier to clean or service the machine. If this is the case at your workplace, you may need to set new expectations for your employees — and consistently apply discipline to those who don’t follow them. Employees should be required to:
- Keep machine guards on while machines are in use
- Promptly replace guards on machines after cleaning or performing routine maintenance
- Notify a supervisor if a guard is broken or missing
- Sign an agreement stating that they understand your organization’s rules and regulations around machine guarding, and that they are aware of the consequences of breaking these rules
Training is one of the best preventative measures you can take to ensure your employees’ safety when using machines. If you don’t already have a machine guarding program, consider implementing one like the Machine Safeguarding Training Course available here. Having a standardized training program levels the playing field for your team, and helps you rest assured that everyone has undergone the latest machine guarding training.
Hazardous materials are ubiquitous in a variety of workplaces and industries. From common household chemicals like cleaning products and antifreeze to industry-specific chemicals like muriatic acid, dangerous substances are a part of everyday life and work.
Unfortunately, when employees aren’t properly trained on handling hazardous materials (or these materials aren’t labelled or stored properly), workers can become injured, hospitalized, and can even potentially die from burns, cuts, explosions, and more.
While some workplaces are replacing harmful chemicals with more eco-friendly ones, this isn’t always an option for every industry. So here are 10 steps to help your employees take the initiative and keep safe when interacting with hazardous materials at your workplace.
1: Ensure all hazardous materials are labelled and stored properly
Have you taken inventory of all hazardous materials in your workplace? Identify all potentially hazardous materials and verify that they’re labelled and stored correctly. Keep hazardous materials in dry, cool areas with proper ventilation — and possibly behind locked doors, when applicable. Ensure incompatible chemicals aren’t stored close together, either, as these can cause dangerous chemical reactions and result in fires or explosions.
OSHA requires hazardous materials to be labelled and accompanied by safety data sheets (SDS). Don’t remove or change these container labels. If a label is missing, don’t use the material or chemical — and instruct your employees to notify a supervisor if they come across an unlabeled substance.
2: Keep Safety Data Sheets accessible to employees
Safety Data Sheets are valuable resources for you and your employees when it comes to identifying and handling hazardous materials. They share the properties of each chemical at your workplace, their hazards, and guidelines for managing each chemical or material. Whether you keep them in an electronic database or store paper copies, SDS should be readily available to all employees — not locked up or kept in a password-protected location.
3: Train employees on reading chemical labels & SDS
You can’t expect every team member to be an expert on every chemical you keep in the workplace, which is why chemical labels and SDS are so useful. Chemical labels and SDS tell your employees everything they need to know about a substance: from the types of dangers it poses (whether it’s flammable, causes cancer, is poisonous, etc.) to instructions for how to manage leaks, spills, or accidents involving the material. They state how a material should be stored and used, and how it should be disposed of.
However, labels and SDS aren’t much help if your team doesn’t use them! To ensure everyone has access to accurate information about your hazardous materials, require your team to take a safety training course on reading chemical labels. Not only is a course a great way to verify your team’s knowledge is up to date, but it will help you cover your bases with OSHA, which requires that workers are able to understand chemical labels and SDS.
4: Control hazardous energy using proper lockout/tagout procedures
If your work environment involves potential hazardous energy releases from equipment or machines, a lockout/tagout process is essential to keeping your workers safe from accidents like burns, amputation, fractures, and more.
Here’s a lockout/tagout training booklet to include in your workplace safety program.
5: Ensure employees understand OSHA’s Hazard Communication Standard
If you’re a chemical manufacturer, you’ll want your employees to be up-to-date on OSHA’s Hazard Communication Standard. To start, here’s a booklet that summarizes the OSHA Standard and provides important details about chemicals, safety data sheets, handling leaks and spills, PPE, and more.
6: Have PPE and emergency equipment ready and available
Your PPE and emergency equipment will vary depending on your workplace, but here are some examples:
- Face masks, gloves, and goggles
- Hand washing stations
- Eye wash stations
Replace PPE if it becomes damaged or worn, and don’t reuse disposable PPE. Cleaning areas should be clutter-free and regularly inspected.
7: Store hazardous materials in their proper containers
Chemicals and other hazardous materials must stay in their original containers. Don’t mix them with other substances or put them into food containers.
8: Handle hazardous materials with care
Each material or substance has its own requirements for personal protective equipment (PPE), handling, use with other substances, and cleanup — so read labels carefully. Only use chemicals for their intended purpose, and take care to follow procedures when transporting hazmat from one location to another.
9: Familiarize yourself with emergency procedures
Accidents happen, so your familiarity with emergency protocol can potentially mean the difference between serious injury and safety. What happens if there’s a chemical fire, spill, or a worker is injured from handling a dangerous substance? When should your team evacuate the premises? Have an emergency plan written and posted for your team to reference.
10: Dispose of hazardous materials properly
Different hazardous materials require different disposal methods. Some chemicals can never be poured down the drain, in the sewer, or even disposed of in the trash. Further, some materials require special sealed containers for disposal, while others may need to be transported to a special facility for disposal.
When it comes to workplace safety, don’t delay. Reinforce the need for vigilance around hazardous materials by checking out our affordable and ready-to-use hazard communication training kits.
While great trainers are important to the success of any organization, safety trainers carry a huge responsibility: the lives of their trainees. With over 4,500 fatal work injuries recorded by the BLS in 2020, there’s no room for B-players on your safety training team.
So how do you identify employees who have the potential to be great safety trainers? And how do you structure your safety training program to ensure compliance across your team of trainers, and by extension, your employees?
Here’s what research shows us about what makes a good safety trainer, along with the knowledge we’ve gleaned from our own decades of experience in safety training. By the end of this article, you’ll be able to identify which of your employees will make the best safety trainers — setting your workplace up for health and success in 2022.
Safety Trainer Characteristics
While diversity and a range of personality types is great to have among your team of trainers, there are a few specific traits that will increase their likelihood of thriving in a trainer role. If you’re evaluating potential trainers from your group of employees, keep an eye out for those that exhibit some or all of the following characteristics:
Thirst for knowledge.
Effective trainers in any setting often have to memorize a dizzying array of information, but for safety trainers, this is even more true. With OSHA and other regulations changing frequently (and the risks of non-compliance being dangerous, expensive, and even deadly), safety trainers will be the most successful when they have a natural thirst for knowledge.
Which of your employees seems to soak up knowledge like a sponge? Is there anyone who has a near-encyclopedic memory when it comes to rules and regulations? These could be your next all-star safety trainers.
Positive attitude.
Your trainers set the tone, and the standard, for anyone they’re training. According to program safety manager Jason Townsell, CSP, “A positive, helpful and cooperative attitude can be the difference between a student learning and a student mentally checking out of a safety training class.”
Professionalism.
While it’s great for your employees to have fun, safety training is, ultimately, a serious matter — so your best trainers should embody professionalism. What does that entail? Beyond the basics, like showing up on time and knowing the material, professionalism is about staying organized, keeping on-track, and following lesson plans methodically and consistently.
A desire to lead and teach. This might be the most important characteristic of all. While you can teach nearly anyone to execute a specific task, no amount of skill-based training can create passion. Either a trainer has it, or they don’t. Keep an eye out for the “helpers”, those employees who regularly lend a hand to their coworkers and go beyond their role to assist others. These are most likely your future A-list trainers.
Safety Trainer Skills
Beyond soft skills, your potential trainers will need to have some specific hard skills and knowledge in order to be effective safety trainers.
Experience in your workplace. While you’ll likely want your trainers to have spent a good amount of time in your industry, keep in mind that seniority isn’t always synonymous with skill. Conduct hands-on tests, interviews, and written exams to compare your trainers’ different skill levels. The more systematically (and objectively) you can measure your potential trainers’ knowledge, the better.
Subject-matter expertise. Are your potential trainers specialists in the areas they’ll be expected to train others? It’s essential that your trainers are subject-matter experts, themselves, so they can answer complex questions and give real-world examples during training sessions.
Train the Trainer: Creating a Safety Training Lesson Plan
Now that you’ve (hopefully!) identified a few employees who would make great trainers, it’s time to optimize your existing training program. Even if you pick the best possible trainers to get your team up to speed on safety and hazards in your workplace, it’s not worth much if your training program and materials don’t cover the right information.
So before you jump in, take inventory of your training checklists, manuals, and other media. Ask yourself:
Do I have an existing safety training program?
If you’re starting from scratch, consider purchasing a general safety orientation training course that your trainers can use immediately to get up to speed on best practices — and to impart that knowledge to their trainees.
Does my training program cover all the potential risks in my workplace?
Conduct a job hazard analysis of your surroundings. Consider physical, ergonomic, chemical, biological, environmental, and other hazards that your workers could encounter — and ensure you have a part of your training program dedicated to each of them. Here are some examples of each:
- Physical. Slips, trips and falls; loud noises, machinery, vibrations, and working from heights.
- Ergonomic. These tend to be less severe, but still problematic, hazards that build over time — like poor posture, improperly structured workstations and desks, and frequent lifting.
- Chemical. Acids, paint, glues, pesticides, and any substances that could result in damage if mishandled.
- Biological. This includes naturally occurring hazards like mold, bodily fluids, airborne pathogens, and sewage.
- Environmental. Natural disasters like fires, hurricanes, and earthquakes.
Do you have a written emergency plan that your trainers understand and can communicate clearly to trainees? An emergency plan is another foundational aspect of workplace safety that can mean the difference between life and death. If you don’t have a plan written up, use this comprehensive emergency plan kit to create one.
Is your current safety training lesson plan up-to-date with the latest OSHA and other compliance regulations? If you have an existing training program, have some of your top current trainers and potential trainers audit your training materials for compliance and report back to you with ideas for potential changes and improvements.
Am I delivering my training in a format that my trainers like and understand? Consider the range of learning styles across your team. While some learners may prefer written materials that they can absorb on their own time, others may learn better by watching a video and discussing with a group. Offer a range of opportunities to read, listen, watch, and “do”, in order to cover all possible learning styles in your workplace.
Are there clear objectives, assessments, and milestones in my training program? Your trainers will have a much easier time gauging the effectiveness of their training if the program is organized and includes assessments to show if learners are retaining knowledge.
How do I gauge when a trainer is ready and fully qualified to train my employees? How do I measure success? It’s a given that your trainers should be able to complete your existing safety training or compliance programs first, but is there any additional training they should undergo before becoming certified trainers?
There’s a lot to juggle when you’re putting together (or improving) your safety training programs. The good news is you don’t need to start from scratch or hire an expensive production team to create a custom program for your workplace. Check out our library of affordable safety training courses, videos, and other materials to customize a program that reflects your unique environment and rest assured that your trainers have access to the latest in workplace safety.

Every seven seconds, an American is injured on the job, according to the National Safety Council. That totals up to 7 million injuries a year, resulting in an average of 21 days of disability per injury. Back and upper extremity injuries can easily triple that number.
Safety hazards are the primary cause of workplace illnesses and injuries. Depending on the industry, this could include chemical, physical, or ergonomic hazards present at work. While most incidents can be prevented with a positive safety culture and frequent safety training, accidents, unfortunately, still occur.
As you analyze your workplace safety protocols and strive to protect your staff, there’s a key element to note: you can’t anticipate what will present as a hazard to every team member.
Sometimes, at-risk people work in safety-sensitive occupations that put them, their colleagues, or their companies in physical or legal jeopardy. Often, these employees don’t even know they’re susceptible to the hazards in their environment—until an incident occurs.
As an employer, you’re tasked with protecting your workers above all else. Therefore, it’s crucial to discover if an employee is a good fit for a physically demanding post before an injury happens.
Many employers, particularly in industrial, manufacturing, and construction industries, utilize the post-offer physical to determine role suitability.
What Is a Post-offer Physical?
A post-offer physical is a test conducted for an employee after a company makes an offer of employment. This exam can tell you if a prospective team member has the physical capacity to perform their job safely and effectively.
You should contract with a licensed medical professional such as a physician or a nurse practitioner, typically your workers’ compensation provider, to conduct the exam. They will provide you with the results and help you interpret their findings.
What should a post-offer physical include?
You will work with your provider to decide what you need to learn about each employee’s physical capacity. In general, the doctor or nurse practitioner will investigate four specific target areas: strength, endurance, physical capacity, and overall physical fitness.
Specifically, a post-offer physical might look at a candidate’s medical history, pre-existing conditions, range of motion, lift strength, limb strength, and body fat and weight. Most importantly, what is measured in the physical exam should match the physical abilities section of your published job description.
How Does a Post-Offer Physical Work?
Your company first extends an offer of employment contingent on passing the post-offer physical exam. Explain to the candidate that this exam consists of medical, physical, and non-medical tests designed to make sure they can fulfill all job requirements safely.
Then, the candidate visits your approved healthcare provider who performs the physical. The provider may ask the candidate if they take any medications, have allergies, or have had prior surgeries. They may also inquire about lifestyle habits such as smoking, drinking, and exercise.
The provider could choose to examine the candidate by feeling for lumps, growths, or tenderness and listening to their heart and lungs through a stethoscope. Often, they’ll check the candidate’s reflexes and their abilities to sit, stand, walk, talk, and think.
After the exam, the doctor will send the relevant results to your company. If the prospective employee passes, you know they can perform the physical functions of the job. However, if they fail, you must decide if you want to take the risk and hire them. Sometimes, you can simply make reasonable accommodations for your preferred candidate to bring them on board safely.
What Can You Learn from a Post-Offer Physical?
In a post-office physical, you can uncover valuable information. Most important is a candidate’s history of impacting injuries.
For example, let’s say you are hiring for a job that requires lifting 20-pound boxes and placing them at various heights on shelves. You send a candidate to the healthcare provider for an exam. Their report informs you that your potential employee had rotator cuff surgery 12 months ago. The doctor or nurse practitioner could ask the employee to perform the task in their office to see what capacity appears to be and add their observations to the report.
With this information in hand, you can ask better questions, such as:
- Is reinjury likely?
- How much of this position’s day is spent doing this activity?
- How much risk is our company willing to accept?
How to Implement a Post-Offer Physical Policy
Start by analyzing the job’s physical requirements. Then, you can talk with supervisors and employees who currently hold the position to learn about frequent physically demanding activities or hazards native to the occupation.
This step offers an excellent opportunity to review your published job descriptions. Have you accurately represented the physical strenuousness of the role? If not, you can update your postings and descriptions. You may even want to list examples of the physical demands of the job in your advertisements.
From there, create a comprehensive job demands analysis. Finally, you will use this analysis to determine what the post-offer physical exam should entail.
Next, reach out to your workers’ compensation provider to see if they offer a post-offer physical exam as a service. If so, they should create a list of essential function tests and validate those with you. Remember, you’re not getting an annual wellness check on this prospective team member. You just want to know if they have the physical capacity to do the job the right way and without getting hurt.
Finally, you need to create a pre-employment physical demands testing process. Your healthcare provider should be able to walk with you through this.
Is a Post-Offer Physical Policy Legal?
Yes! Under both the Americans with Disabilities Act and the U.S. Equal Employment Opportunity Commission’s regulations, you can conduct a post-offer physical. Just like you can conduct a drug test after making an offer of employment, you can also conduct a medical test to make sure the candidate you want to hire can safely perform the physical demands of their job.
Provided you use the same job analysis metric for your medical tests that you used for your job description, you can transfer an employee between job sites or even between states without conducting another exam. This is especially valuable to large employers operating multiple locations across state lines.
If an employee is transferring positions, a new pre-employment physical could be necessary. In general, team members moving to a more physically demanding job should see a provider. Those transferring to a less strenuous role probably will not need reassessment.
OSHA can require certain employees to get vaccinated for Hepatitis A or MMR. You can also legally recommend or require your at-risk employees to take sensible occupational health and safety precautions in your work setting.
However, one point to be aware of is that you should not have access to a candidate’s medical records beyond what is required for your job offer. Again, a testing company or labor law attorney can help you make sure you’re staying on the right side of HIPAA regulations.
Benefits of a Post-offer Physical
Approximately 10% of those who undertake the post-offer physical will “fail.” This means, by requiring this exam, you helped protect these workers from a potentially life-changing injury.
In addition, new hires will better understand the physical demands of the position before they sign up to work with you. Even better, these prospective employees now know you care about them and are committed to their well-being at work. This can lead to an increase in worker retention.
Finally, a post-offer physical helps keep workplace accidents at bay, protecting your employees and business.
Workplace injuries cost your employees money, their well-being, and potentially loss of future income potential. Injuries are also costly to your company and cause loss of time, money, and productivity.
The best way to prevent workplace injuries is to frequently train your workers on potential hazards and promote a safe work culture. Ready to train your staff? National Safety Compliance can help you get started. We offer all-in-one video kits with everything you need to prepare your workers on vital safety topics, including back safety; slips, trips, falls; and bloodborne pathogens.
After training, since not every hazard affects every employee equally, you can decrease injury risks by screening out vulnerable employees from safety-sensitive posts.
A post-offer physical exam is a legal, proven, and cost-effective way to protect your workforce and save your company money.
If you’d like to learn more about post-offer physicals, watch our recent Injury Prevention for Workplaces webinar featuring Denice Rankin, a workers compensation and HR generalist.
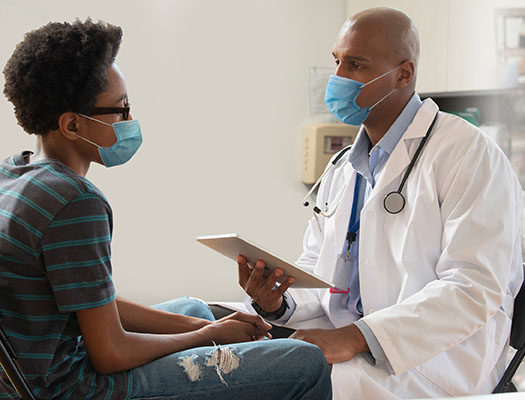
What Employees Should Know About COVID-19 Protections in the Workplace
SARS-CoV-2, the virus that causes COVID-19, spreads mostly among unvaccinated people who are in close proximity to each other. The virus spreads particularly indoors and especially in poorly ventilated areas.
Vaccination is an essential element in a multifaceted approach to protect workers. If your employer offers opportunities to take time off in order to get vaccinated, take advantage of the time offered. Vaccines authorized by the U.S Food and Drug Administration (FDA) are effective at protecting those vaccinated against symptomatic and severe cases of COVID-19 and death. A growing body of evidence suggests that those fully vaccinated are less likely to have symptomatic infection or transmit the virus, according to the Centers for Disease Control and Prevention (CDC).
Many employers have created COVID-19 prevention programs that include precautions to keep unvaccinated or otherwise at-risk employees safe. Created prevention programs might include:
- Telework
- Flexible schedules
- Engineering controls (especially ventilation)
- Administration policies (e.g. vaccination policies)
- PPE
- Face coverings
- Physical distancing
- Enhanced cleaning programs, focusing on high-touch surfaces
The recommended precautions and policies of your workplace should be followed. These multi-layered controls are specific to your workplace and are particularly important to unvaccinated or otherwise at-risk employees.
In addition to these guidelines, the CDC now recommends those that are fully vaccinated wear a mask in public indoor settings where there is a potential of substantial or high transmission. Still, those fully vaccinated might choose to mask, regardless the level of transmission. This choice might depend on if they or someone in their household is immunocompromised or at an increased risk of severe disease, or if others in their household are unvaccinated.
Ask your employer about prevention policies and plans for your workplace. Additionally, employees with disabilities who are at risk may request reasonable accommodation under the Americans with Disabilities Act (ADA).
If your employer does not have a COVID-19 prevention plan and you are unvaccinated or otherwise at risk, you can help protect yourself and others by following the steps below:
- Get a COVID-19 vaccine as soon as you can. Check with your employer about paid leave opportunities, if necessary, to get vaccinated and for recovery time from any side effects.
- Wear a face covering. When properly worn, face coverings are simple barriers worn over the mouth, nose, and chin. These coverings help prevent your respiratory droplets or large particles from reaching others. Higher quality masks are encouraged, as they provide a greater measure of protection. When working outdoors, you may opt to not wear a face covering; however, should you choose to, your employer should support you in safely wearing a face covering continuously, especially if you work closely with others.
- Social Distance. Unless fully vaccinated or not otherwise at-risk, stay far enough away from others that you are not breathing in respiratory particles produced by them. This distance is generally 6 feet (about 2 arm lengths). Please note that this is not a guarantee that you will avoid infection, especially if you are in enclosed or poorly ventilated areas.
- Take advantage of telework or flexible schedule policies, if offered by your employer.
- Perform work tasks, hold meetings, and take breaks outdoors when possible.
- Participate in any training offered by your employer to learn how rooms in your workplace are ventilated effectively, if offered. Encourage your employer to provide such training if it does not already exist. If you see any vents that are clogged, dirty, or blocked by furniture or equipment, notify your building manager.
- Practice good personal hygiene and wash your hands often. When you cough or sneeze, cover your mouth and nose with a tissue or the inside of your elbow. Do not spit. Monitor your health daily and check for COVID-19 symptoms (fever, cough, shortness of breath, etc.)
- Get tested regularly, especially if you live in areas of substantial or high community transmission.
COVID-19 vaccines are safe and highly effective at preventing you from getting COVID-19. If you are not yet fully vaccinated or otherwise at-risk, these multi-layered controls provide optimum protections that prevent exposure and infection.