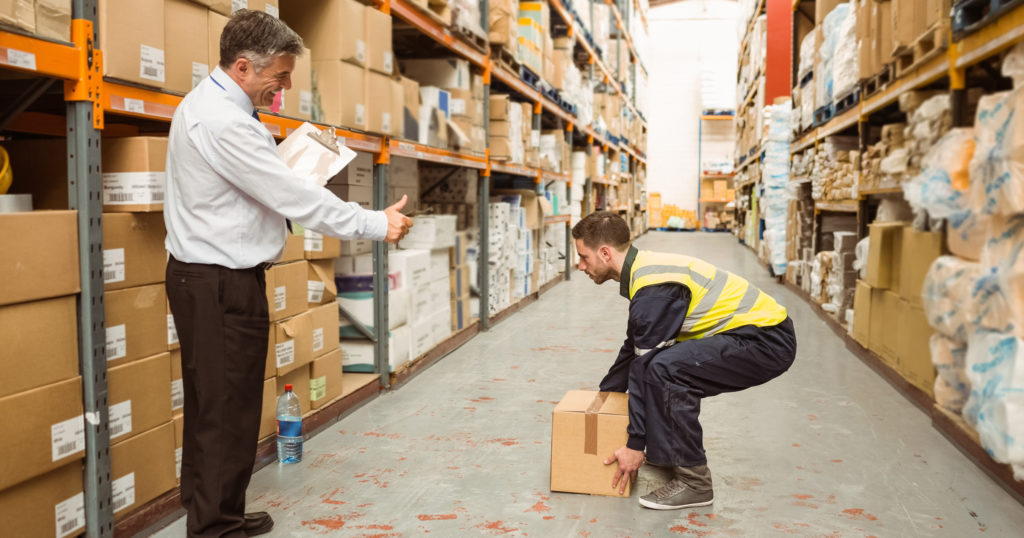
While lifting seems like a risk-free activity, there are many potential hazards. According to the Bureau of Labor Statistics (BLS) more than one million workers experience back injuries each year, with 75% of back injuries occurring while performing lifting tasks.
A back injury can have a permanent effect on a worker’s life and is one of the most common reasons that people miss work. Ensuring your employees have received lifting safety training and practice safe lifts makes them less likely to incur such injuries.
A big benefit of using safe lifting training is that it teaches your employees about the dangers of overexertion while lifting and the importance of always using OSHA proper lifting techniques no matter how heavy the load.
At National Safety Compliance, we offer several different ways to train your employees on safe lifting techniques, including turn-key online safe lifting and back safety training modules onlineOSHAtraining.net, as well as more traditional employer-led training programs available on DVD, USB, or Digital Access on OSHA-Safety-Training.net.
Proper Lifting Technique
- Plan ahead
Before lifting anything, it is important to check your path and surroundings to ensure the work area is flat, dry and free of debris. Decide where you’re going to place the object and how you’ll get there. Then determine the approximate weight of the object and whether or not it’s safe to lift on your own or with a two-man lift limit.
- Stretch
Warming up before lifting can be the defining factor between an injury and gliding through your workload. It is imperative to stretch your back and legs in order to warm up the muscles, some great stretches for this are lower back rotations and the hamstring stretch. You also need good blood flow in order to perform properly so you should do a few jumping jacks or run in place briefly before beginning.
- Lift
To lift safely, you should stand as close to the load as possible so you don’t exert more force onto your back by extending the distance. Then bend your knees and keep your upper body upright so your legs do the lifting rather than your back. Look straight ahead and keep your back straight and shoulders back so you have a slight arch in your lower back.
- Carry
Get a good grip on the load and use your feet to change direction, taking small steps as you go. As you change direction, lead with your hips and keep your shoulders in line with your hip’s movement. Keep the load close to your body with your elbows at your sides.
- Set down
Lower the load in reverse by lowering your legs and keeping the load close to your body. Keep your head up, stomach muscles tight and the load close to your body. While it may seem like this is the easy part, you can injure yourself just as easily with setting down a load as you can picking it up.
Dangerous Activities to Avoid When Lifting:
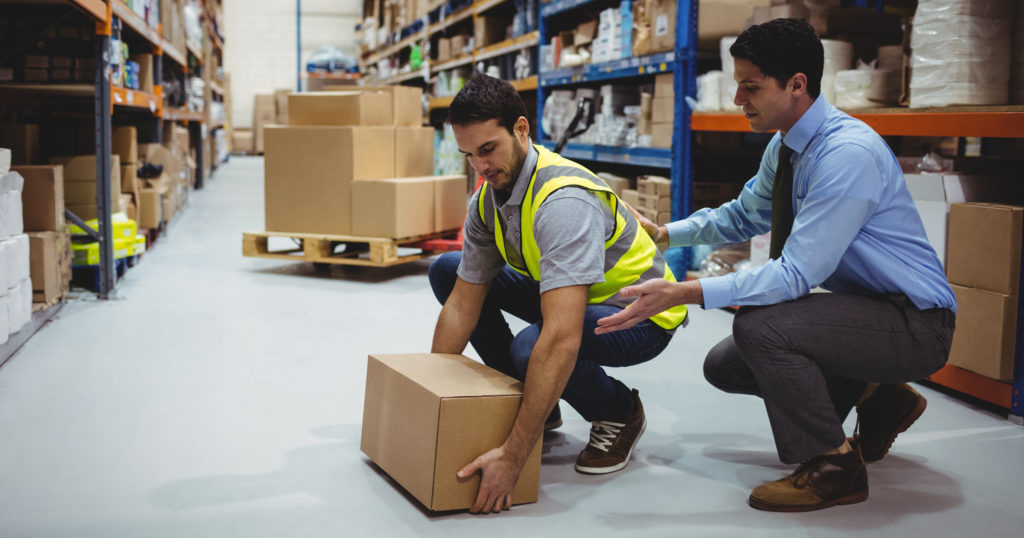
- Twisting or turning your body while lifting a load
- Attempting to carry a load that is too heavy or too large
- Lifting an object above shoulder level
- Bending forward rather than squatting down to your load
- Using a partial grip with only 1-2 fingers
- Lifting or working while fatigued
- Obstructing your vision while carrying a load
- Rushing through the process
- Holding your breath
Can Back Belts Help Prevent Injury?
While back belts have become commonplace for a lot of employees in a workforce that requires a lot of lifting, there is no research that shows that these prevent or decrease back injuries related to lifting.
Back belts offer a lot of supposed benefits but there is a severe lack of scientific evidence to support these benefits. In most cases, back belts can create more potential dangers by creating a false sense of security and making workers more likely to attempt to lift more weight than they can handle.
This is why it is so important to still be mindful of safe lifting techniques and practices rather than relying on a back belt to do the job. Regardless of whether you believe back belts are advantageous or not, do not trust them as a substitute, and instead be mindful of proper lifting.
If you’re putting all your prevention resources into back belts, you are not adequately protecting your workers. Instead, focus your efforts on reducing all risk factors, training your employees on how to lift and respond to reports of discomfort and fatigue as soon as they arise.
High Frequency and Long Duration Lifting
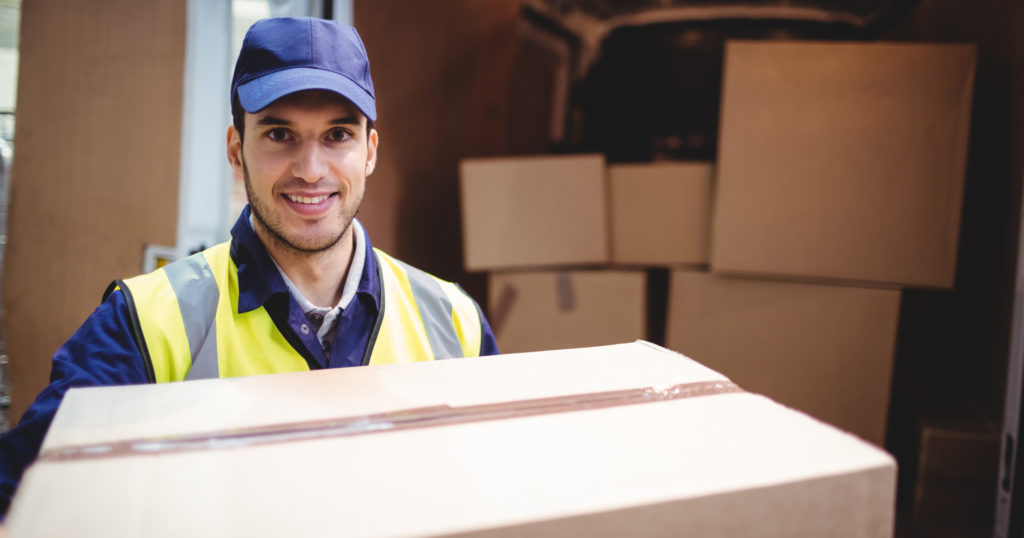
When lifting and carrying loads for long periods of time it is important to be mindful of what your body is telling you. If you begin to feel fatigued you should set down the load, rest and take a break. It is vital to keep your energy up for picking up and setting down the load following the proper technique.
If you are required to have your employees lift high frequency and long duration loads it is essential to plan ahead in order to work in frequent breaks, teamwork and rotating tasks.
If you have any questions about our proper lifting training programs, please don’t hesitate to reach out. You can contact us using the chat function on our site, e-mail us at sales@nscemail.com or call us at 877-922-7233.