Category: Safety News & Information (English)
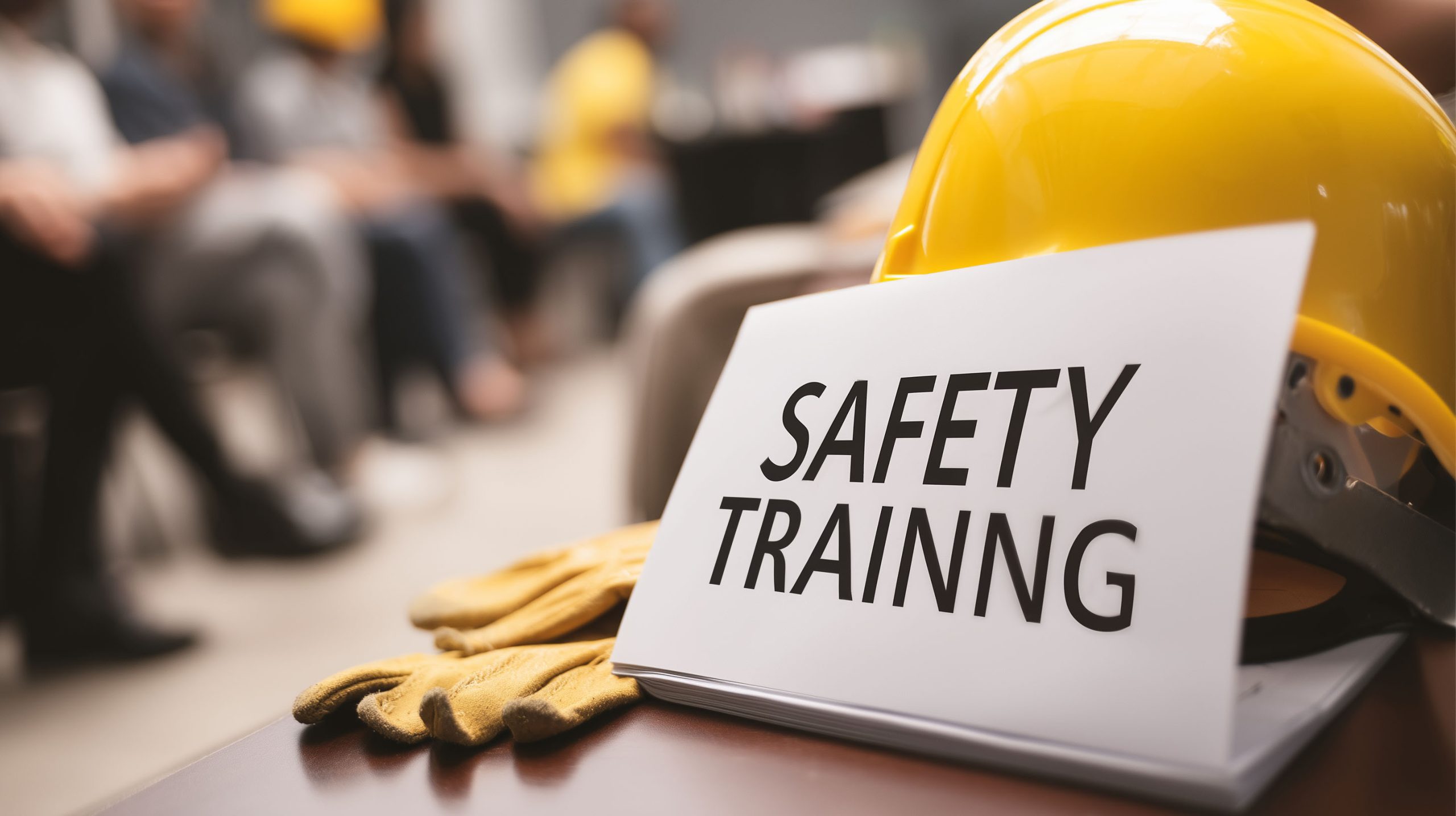
Avoiding the top 5 safety training mistakes is essential to building a safer, more effective workplace—and knowing how to correct them can make all the difference. Workplace safety training is more than a legal requirement—it’s essential for protecting employees and maintaining productivity. But even the best-intentioned training programs can fall short if common pitfalls aren’t avoided. By offering many safety training courses at NSC, we are here to help you keep your employees safe and make sure everyone makes it home from work.
According to the National Safety Council, effective safety training can reduce workplace injuries by up to 60%, saving companies thousands in medical costs, lost productivity, and regulatory fines. In this post, we’ll break down the top 5 safety training mistakes and how to avoid them in order to help you build a truly effective safety training culture. Before we dive into the mistakes, let’s look at why safety training is critical:
- Protects Lives and Well-being: Safety training gives employees the knowledge they need to avoid accidents and injuries on the job.
- Improves Productivity: A safe workplace reduces downtime, absenteeism, and disruption due to injuries.
- Reduces Legal and Financial Risk: Fewer accidents mean fewer workers’ comp claims, OSHA fines, and legal battles.
- Builds Employee Trust: When companies show they care about safety, employee morale and retention improve.
- Reinforces Company Culture: Safety-focused training promotes responsibility, communication, and teamwork.
Top 5 Safety Training Mistakes
1. Treating Safety Training as a One-Time Event
The Mistake:
Many organizations treat safety training as a “set-it-and-forget-it” task—offering it during onboarding or once a year.
How to Avoid It:
Make safety training an ongoing effort. Use monthly refreshers, toolbox talks, and update training whenever procedures or regulations change.
2. Using Generic, One-Size-Fits-All Programs
The Mistake:
Off-the-shelf training often fails to address your team’s specific risks or workflows.
How to Avoid It:
Customize your safety programs. Focus on the actual hazards employees face in their day-to-day roles, and tailor examples to your specific work environment.
3. Failing to Engage Employees
The Mistake:
Passive formats like long videos or PowerPoint slides lead to poor retention and engagement.
How to Avoid It:
Use active, hands-on training: simulate real scenarios, use quizzes, and encourage discussion. Interactive training is more memorable and effective.
4. Not Measuring Effectiveness
The Mistake:
Just checking a box that training is “complete” doesn’t mean it was understood or useful.
How to Avoid It:
Track learning through pre- and post-training assessments, observe behavior changes on the job, and review safety incidents regularly for gaps in knowledge.
5. Overlooking Follow-Up and Accountability
The Mistake:
Failing to reinforce training can lead to bad habits or noncompliance over time.
How to Avoid It:
Hold regular safety audits, briefings, and one-on-one follow-ups. Encourage supervisors to lead by example and correct unsafe practices in real time.
Bonus Tip: Don’t Forget to Train the Trainers
Even experienced supervisors may not have the skills to teach effectively. Taking the time to train-the-trainer ensures those delivering the training are clear, confident, and engaging. Having subject matter knowledge doesn’t mean someone can teach effectively. Train your trainers in facilitation and communication to ensure knowledge is passed on clearly and confidently.
Effective trainers know how to read the room, adapt to different learning styles, and keep sessions engaging and practical. When you invest in trainer development, you make sure safety messages are communicated effectively and understood by all.
Build a Stronger Safety Culture Today
Want to improve your training program and reduce safety incidents? Effective safety training isn’t just about compliance—it’s about culture, care, and commitment. By avoiding these mistakes and taking a proactive approach, you’ll build a safer, smarter workplace where everyone thrives. At NSC, we are here to help you protect your workforce and ensure every employee returns home safely each day. We offer a variety of safety training options in a wide range of industries.
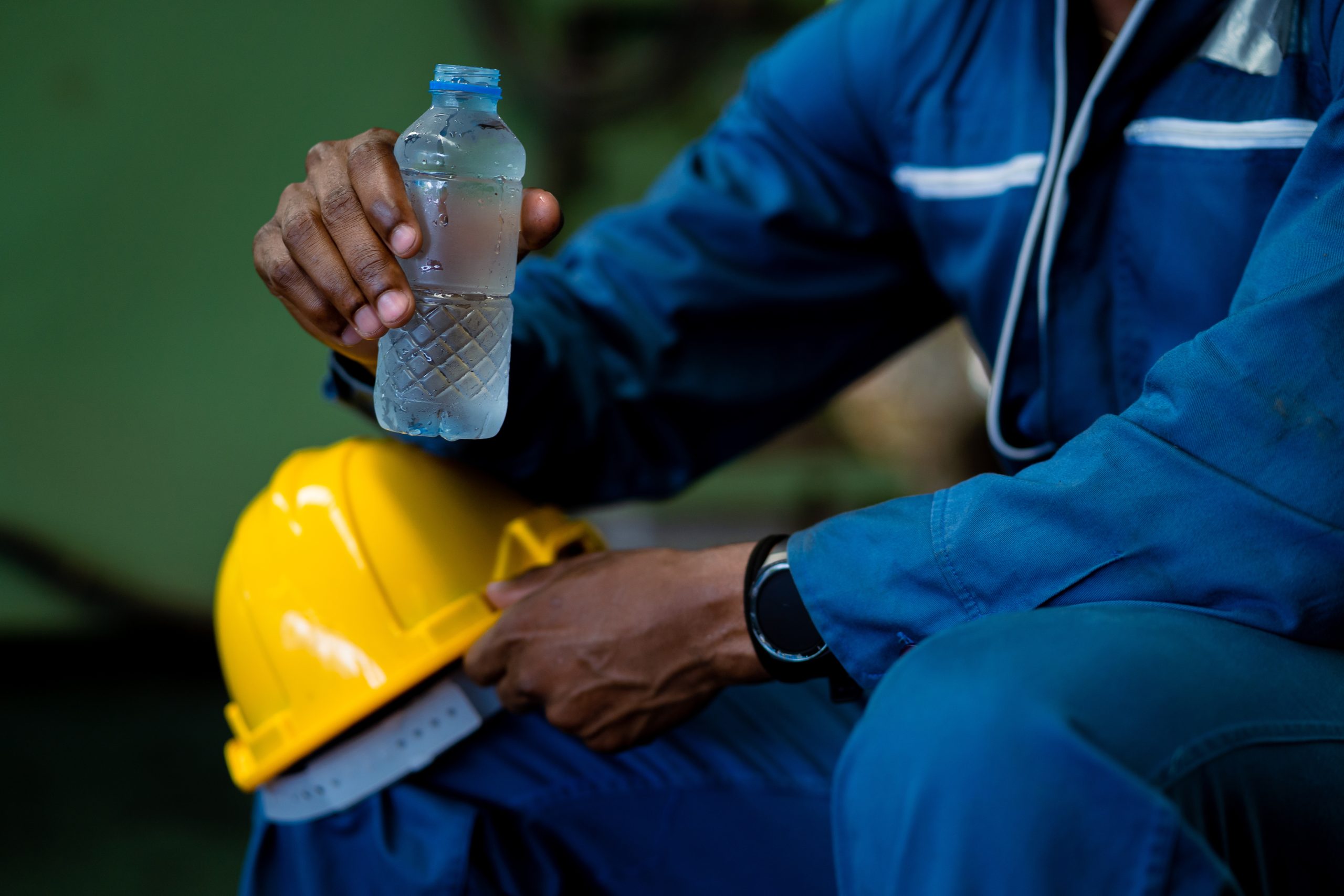
As temperatures rise, so do the risk of heat-related illness and injury among workers, especially those in physically demanding or poorly ventilated environments. Whether on a rooftop, in a kitchen, or behind the wheel of a delivery truck, heat stress is a silent but serious occupational hazard. That’s why heat safety training for workers is essential—not only for compliance but for saving lives.
Who’s Most at Risk of Heat-Related Illness?
Workers at highest risk typically fall into four categories:
1. Outdoor Laborers: These workers face direct sunlight, physical exertion, and heavy gear:
- Construction Workers
- Agricultural Workers (Farmworkers)
- Landscaping and Grounds Maintenance Workers
- Roofing Workers
- Utility Workers (Electricians, Water Treatment, etc.)
- Outdoor Event Workers (Festival and Construction Crew Members)
2. Indoor High-Heat Workers: These workers operate in enclosed spaces near heat-generating machinery:
- Factory and Warehouse Workers
- Food Service Workers (Kitchen Staff, Cooks, Dishwashers)
3. Mobile Workers: Spending long hours in hot, enclosed vehicles poses their own dangers:
- Truck Drivers
- Delivery Personnel
4. Underground/Confined Space Workers: Often facing extreme humidity and limited airflow in confined spaces:
- Mining Workers
- Maintenance and Repair Workers
- Farm Workers
Why Heat Safety Training Matters
Heat-related illnesses are 100% preventable. Yet every year, thousands of workers suffer from heat stress, and some cases turn fatal. Employers must ensure that both supervisors and workers are trained to prevent, recognize, and respond to these dangers.
Key Elements of Effective Heat Safety Training
1. Educating on Heat Stress
- Types of heat-related illnesses: heat cramps, heat exhaustion, and heat stroke
- Common symptoms and early warning signs
- High-risk environmental conditions like high heat with humidity
2. Prevention Best Practices
- Schedule regular water breaks (every 15–20 minutes)
- Encourage light, breathable clothing
- Rotate shifts or modify schedules during extreme heat
3. Emergency Response
- What to do when a worker shows symptoms
- Cooling methods (ice packs, shade, hydration)
- When to call 911 or activate your emergency plan
4. Acclimatization Programs
- Gradual exposure over 7–14 days for new or returning workers
- Monitor vulnerable employees more closely during heat waves
5. Communication and Support
- Empower workers to speak up if they feel unwell
- Train supervisors to act quickly and without hesitation
- Foster a culture that prioritizes worker well-being over productivity
If your team includes high-risk roles—from construction crews to kitchen staff, now is the time to make heat safety training part of your standard protocol. As summer arrives and extreme heat events return, the workplace must be prepared. Train. Protect. Prevent. That’s a formula for a safer, cooler, and more productive workforce.
At NSC, we have the Heat Safety Training course you need to equip your workers for the heat. They need to be aware of heat-related illnesses and hazards, be able to keep themselves safe in hot environments, and be on the lookout for dangerous heat-related symptoms in their co-workers. Heat-related illnesses can have severe consequences for both workers and employers. Everyone has a role to play to keep each other safe. Workers in physically demanding jobs, especially those who are exposed to high temperatures for extended periods, are most vulnerable. Don’t delay, begin training today in order to keep all your employees safe tomorrow.
Additional Helpful Resources:
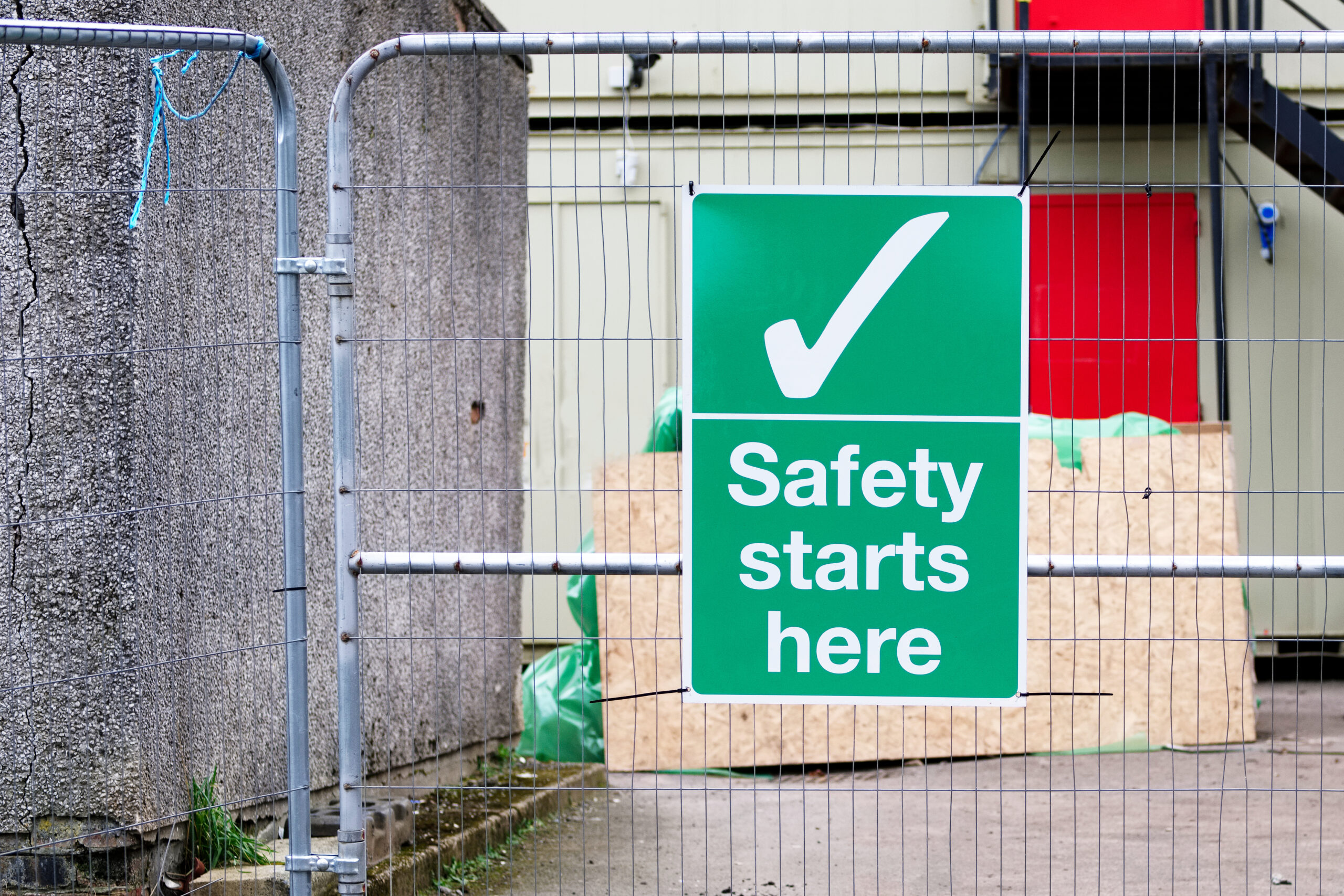
Quality Safety training for new hires can make all the difference in keeping workers safe. According to Injury Facts, compiled by the National Safety Council, the first 90 days of work can be some of the most dangerous. In fact, in a two-year period nearly 278,000 employees experienced an incident that resulted in days away from work – in their first 90 days on the job. This can be prevented.
“The data says that it’s among the most dangerous times in someone’s career,” said Larry Pearlman, president and founder of Safety and Consulting Associates Inc. So, when should the process of keeping new workers safe begin? “At the very moment an applicant learns about your organization’s job opening,” Pearlman says.
When and Where To Begin
- Make sure job descriptions, job postings, and employment boards communicate a safety culture.
- Provide a realistic preview of the job’s risks.
- Thoroughly explain potential risks and job requirements (like being able to lift a certain amount of weight, etc).
- Use YouTube videos to allow potential employees to preview the work environment and what the job actually is.
- Ask safety-related questions during the interview.
- Employers must send clear messages about the importance of the organization’s safety culture.
- Establish best practices regarding safety and keep lines of communication open.
Rich Ives, senior vice president of business insurance claims at Travelers says, “I’ve seen numerous examples over the years of severe injuries from new employees trying to do the right thing and trying to be a good employee but not understanding exactly how the operation works.”
“The message that every worker’s safety is important has to come from Day 1 – not just in response to injuries,” Peter Smith, president and senior scientist at the Toronto-based Institute for Work and Health said. “That sets the tone from the very beginning that we value safety within this workplace.” Training plays a key role, especially when a strong safety plan is in place.
Additionally, Chris Hayes, assistant vice president of transportation and workers’ compensation risk control at insurance provider The Travelers Cos., believes many of these injuries can be prevented with proper precautions, training, and onboarding. “Unless there’s a well-understood, well-documented and well-communicated safety plan already, you really don’t know what to train people on as they come in,” Hayes said.
Have a Safety Plan in Place
- Define safe work practices for all tasks.
- Take proper precautions.
- Provide quality training.
- Examine prior injuries.
- Highlight danger zones or hot spots on the job site.
“Spend the time building up the structures so you have those things well-defined,” Hayes said. “It absolutely helps.” “That includes defining safe work practices for all critical tasks, examining prior injuries and highlighting “hot spots” on the jobsite.”
“That first 90 days is critical,” Hayes said. “That’s when you’re cementing that employee’s access to the right safety tools, the right resources, getting them involved in corporate culture, and helping them work through any misconceptions or gaps in communication that might be arising.”
At National Safety Compliance we have a variety of Safety Orientation resources to help train and keep your new workers safe. It’s never too early to set the tone with potential employees and communicate the importance of safety. Because every life counts, and at NSC we equip employers to create safe workplaces where employees thrive by preventing workplace injuries and protecting employees so they can prosper.
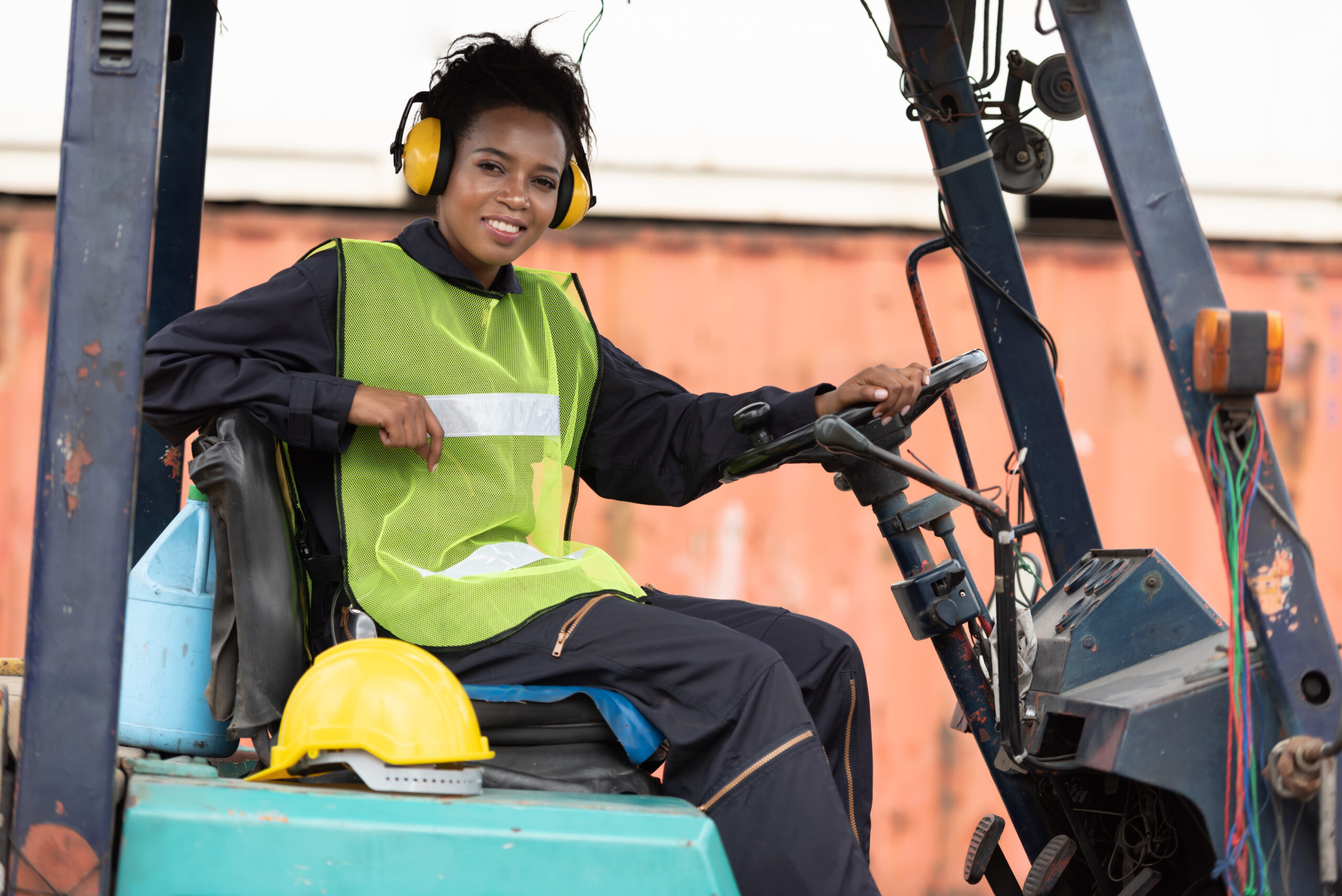
Personal Protective Equipment (PPE) must fit properly to provide employees appropriate protection from workplace hazards. In fact, improperly fitting PPE reduces the effectiveness of protection. Even worse, it may fail to provide any protection at all to an employee. Further, it presents additional hazards to employee safety. Sadly, it can even discourage employees from using vital protective equipment at all. The construction industry is at high risk of failing to offer properly fitting PPE for all workers. OSHA is taking this issue seriously.
In response to this problem, OSHA has finalized revisions to its personal protective equipment standard for construction, (29 CFR 1926.95(c). The revisions explicitly state that PPE must fit properly. This revision aligns the language in the PPE standard for construction with the corresponding language in OSHA’s PPE standards for general industry and shipyards. It affirms OSHA’s interpretation of its PPE standard for construction as requiring properly fitting PPE. The Center for Construction Research and Training (CPWR) has created a new infographic that reminds employers and workers about the importance of proper fit and what that should look like.
In construction, women often have a harder time than men in having access to properly fitting protective equipment. Often, they resort to altering the equipment available which can create its own hazards.
There is hope for women in construction according to Allison Roberts Grealis, founder and president of the Women in Manufacturing Association, “I believe there has been a huge improvement in the last decade in PPE for women, and it’s exciting to see more vendors offering PPE designed for women.” The Center for Construction Research and Training (CPWR) has compiled a list of providers of appropriate-fitting personal protective equipment for female workers.
Jessica Richardson, who chairs the Safety and Health Awareness Committee of the National Association of Women in Construction said, “I don’t know of anyone who thought that PPE wasn’t supposed to fit.” Richardson goes on, “That being said, having this clarity around it, I think, will help drive folks in the right direction, especially the manufacturers, suppliers, distributors and employers.”
Industry leaders are expecting more widespread improvements with the publication of OSHA’s final rule requiring PPE to properly fit each worker in the construction industry. Kelly Franko of AWSAM (Alliance of Women’s Safety Apparel Manufacturers) expressed, “With OSHA passing the standard on fit, I think we’re going to see even more, because companies are trying to do the right thing.”
Encourage Proper Use of PPE for All Employees
- Use visual cues: eye-catching signage near workstations and entry ways.
- Make PPE easily accessible: position PPE in high-traffic areas.
- Positive reinforcement: create a culture where PPE use is encouraged and rewarded.
- Create a default safety option: make PPE part of the workflow and build safety into daily routines.
- Reshape the work environment: place PPE dispensers near task-specific equipment.
Pitfalls to Avoid
- Information overload: too many signs overwhelm workers.
- Relying on data: facts and statistics are useful, but they aren’t effective motivators. Avoid overwhelming with too much copy or numbers.
- Inflexible design: One-size-fits-all solutions don’t work.
Properly fitting PPE is a critical element of an effective occupational safety and health program. PPE must fit properly to provide appropriate protection to employees from workplace hazards. Improperly fitting PPE fails to provide protection to an employee, reduces the effectiveness of protection, can present additional hazards, and may discourage employees from using the protective equipment in the workplace. NSC offers a variety of Personal Protective Equipment training resources.

OSHA’s Top 10 Remains Much the Same.
Fall Protection – General Requirements is OSHA’s most frequently cited standard for the 14th consecutive year. The announcement was made during the 2024 NSC Safety Congress & Expo in Orlando.
OSHA’s Directorate of Enforcement Programs, Scott Ketcham, presented the initial list – which represents OSHA Information System data from Oct. 1, 2023, to Sept. 5. (The finalized data, will be released in December.) “OSHA takes falls very seriously,” Ketcham said during the presentation. “We’re trying to curb this hazard and make inroads to help people understand the standard and requirements. Too many lives are lost each year from workers who fall to their death.”
As is typical, the standards that comprise the Top 10 remained unchanged from FY 2023. However, there was movement within the ranking. Respiratory Protection climbed three spots to No. 4. It was seventh in FY 2023. “What’s more precious than our lungs?” Ketcham asked the audience. Additionally, Scaffolding, fell four spots to No. 8.
The Full List of Top 10 Most Cited OSHA Standards:
- Fall Protection– General Requirements: 6,307 violations
- Hazard Communication: 2,888 violations
- Ladders: 2,573 violations
- Respiratory Protection: 2,470 violations
- Lockout/Tagout: 2,443 violations
- Powered Industrial Trucks: 2,248 violations
- Fall Protection – Training Requirements: 2,050 violations
- Scaffolding: 1,873 violations
- Personal Protective and Lifesaving Equipment – Eye and Face Protection: 1,814 violations
- Machine Guarding: 1,541 violations
While OSHA generally does not post the official top ten list of violations until after the first week in April (in order to allow the prior fiscal year’s inspection data to finalize), it is unlikely that the top ten will see any changes to what was announced at the Expo. Here at National Safety Compliance we offer a variety of resources for each of these OSHA standards. Employers can utilize training options to improve their company’s efforts to keep workers safe and ensure that every employee makes it home safely.

Beginning in 1922 and continuing for over 100 years, the NFPA (National Fire Protection Association) has sponsored the annual public observance of Fire Prevention Week. Additionally, President Calvin Coolidge proclaimed Fire Prevention Week a national observance in 1925. In fact, it is the longest-running public health observance in our country. During Fire Prevention Week, participants learn how to stay safe in case of a fire. Among other efforts, firefighters graciously provide lifesaving public education in an effort to decrease casualties caused by fires.
In commemoration of the Great Chicago Fire, Fire Prevention Week is observed each year during the week of October 9th. Sadly, this disastrous fire killed more than 250 people, left 100,000 homeless, destroyed more than 17,400 structures, and burned more than 2,000 acres of land.
This year, Fire Prevention Week is October 6-12. This is a great opportunity to review fire hazards in the workplace and what to do in a fire emergency. This year’s campaign strives to educate everyone about the importance of having working smoke alarms. For information on how to plan and implement a successful FPW campaign using NFPA resources, visit NPFA.org.
National Fire Protection Association Resources for Fire Prevention Week:
- Key Smoke Alarm Safety Guidelines and Tips
- Smoke Alarm Technology Updates
- Best Practices
- Action Steps: Install, Test, and Replace
- Educator Toolkit
- Smoke Alarm Activities
- Digital Catalog
At National Safety Compliance we offer a variety of fire safety training items including training kits, booklets, and fire safety posters. Injuries due to fire can be prevented and smoke detectors that are functioning properly is one step towards protecting all our employees.
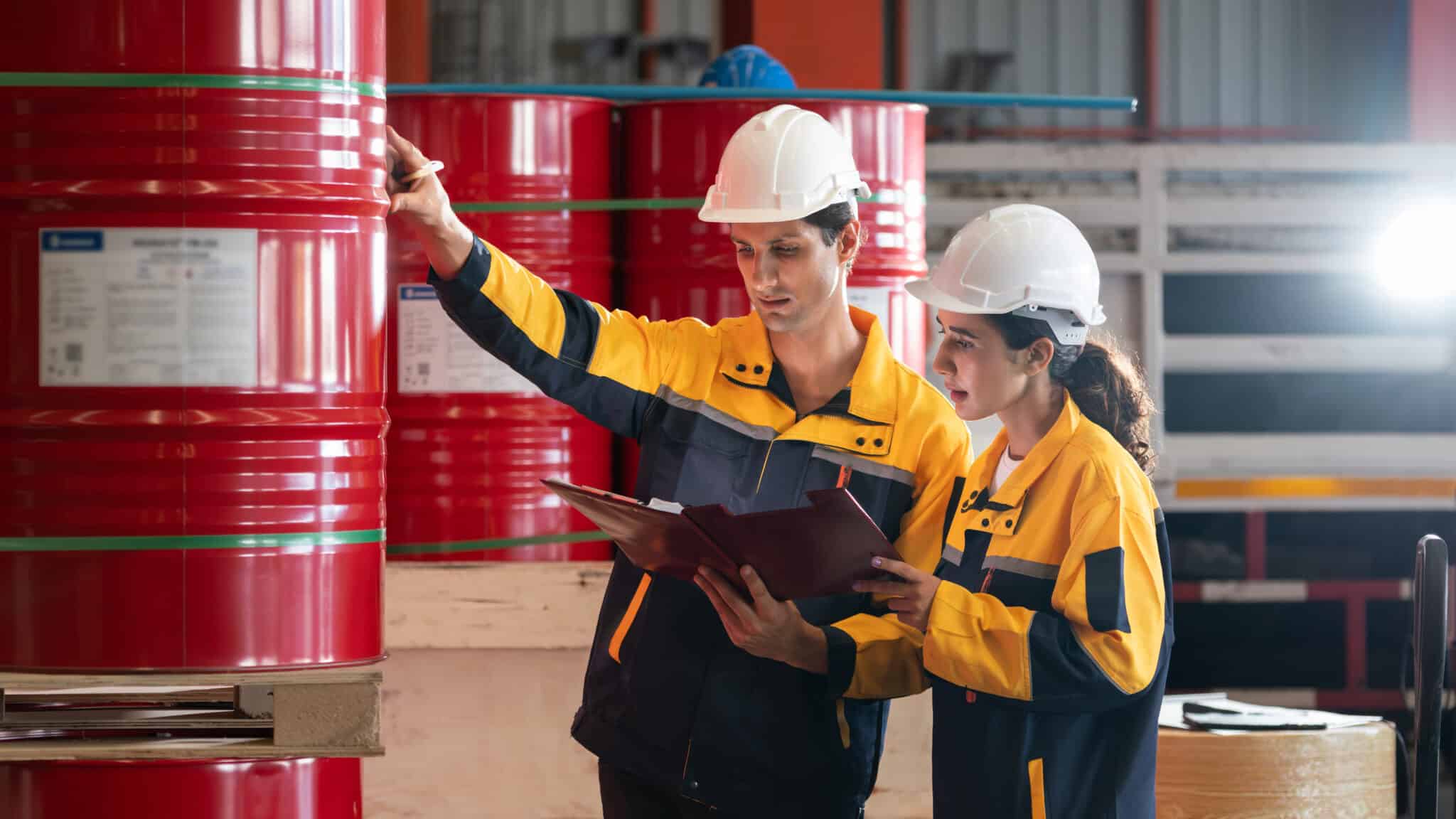
True to its mission, OSHA is always working to assure America’s workers have safe and healthful working conditions, OSHA has recently updated The Hazard Communication Standard (HCS). The update seeks to better align the HCS with Revision 7 of the United Nations’ Globally Harmonized System of Classification, as well as improve alignment with other federal agencies and international trading partners. The updated standard will improve effectiveness by better informing employees about chemical hazards in the workplace. This final rule will increase worker protections and reduce the incidences of chemical-related occupational illnesses and injuries by improving the information on the labels and safety data sheets for hazardous chemicals.
Highlights of the Changes
- Enhanced Information on Labels and SDS
- Clearer Hazard Classification
- Improved Physical Hazard Classes
- Streamlined Precautionary Statements
With these changes, even labels on small containers will be more comprehensive and readable, so that workers have crucial hazard information easily available. The update also addresses trade secret concerns, while also ensuring critical safety information remains accessible on SDS. OSHA revised the classification process to provide complete and accurate hazard information on labels and SDS so that workers understand the chemicals they handle and make informed decisions. Updates to physical hazard classifications will better inform workers on the safe handling of explosives, aerosols, and chemicals under pressure. In addition, updated precautionary statements will provide clearer instructions on handling, storing, and disposing of hazardous chemicals.
In light of these updates to the Hazard Communication Standard, we have updated a series of three Hazard Communication training programs. At NSC we strive to ensure that our training programs contain the most relevant and up to date content for your training efforts.
Updated Training Programs
Hazard Communication
The number of existing chemical products is estimated to be in the hundreds of thousands with hundreds of new ones being introduced into the workplace each year. This poses a serious problem for exposed workers and their employers. This training program has been developed to assist with training all employees concerning chemical products and the hazards they present.
Hazard Communication: Safety Data Sheets
Thousands of chemicals are used in our personal lives and at work. Most of us encounter chemicals at work on a daily basis. While many chemicals are relatively harmless when handled properly, many are dangerous substances by nature. With some chemicals, the simple act of pouring from one container to another can be hazardous. All chemicals can pose serious physical and/or health hazards when transported, handled, or used improperly. Manufacturers are constantly developing new chemicals to be used in ever widening ways. Without accurate adequate knowledge about these chemicals, their hazards, and appropriate precautionary measures, employees are at a great risk of harmful and even fatal accidents.
Hazard Communication: Chemical Safety
The basic goal of any effective Hazard Communication program is to ensure the safety of the employee who works with and around different hazardous chemicals. Each and every workday, over 30 million workers in the U.S. are potentially exposed to a chemical hazard. Exposure to chemicals can cause serious physical and health problems. For employees to be safe when dealing with chemicals, information must be transmitted to them about the identities and hazards of the chemicals. This training program was created to assist with training employees concerning these chemical products and the hazards they present. The focus of this training will be the chemical label.
Overall, this significant revision to the Hazard Communication Standard OSHA aims to better inform employees about chemical hazards in the workplace. The rule does this by improving the quality and accessibility of information on chemical labels and safety data sheets (SDS). It is vital that employers and employees have training that is in alignment with these revisions.
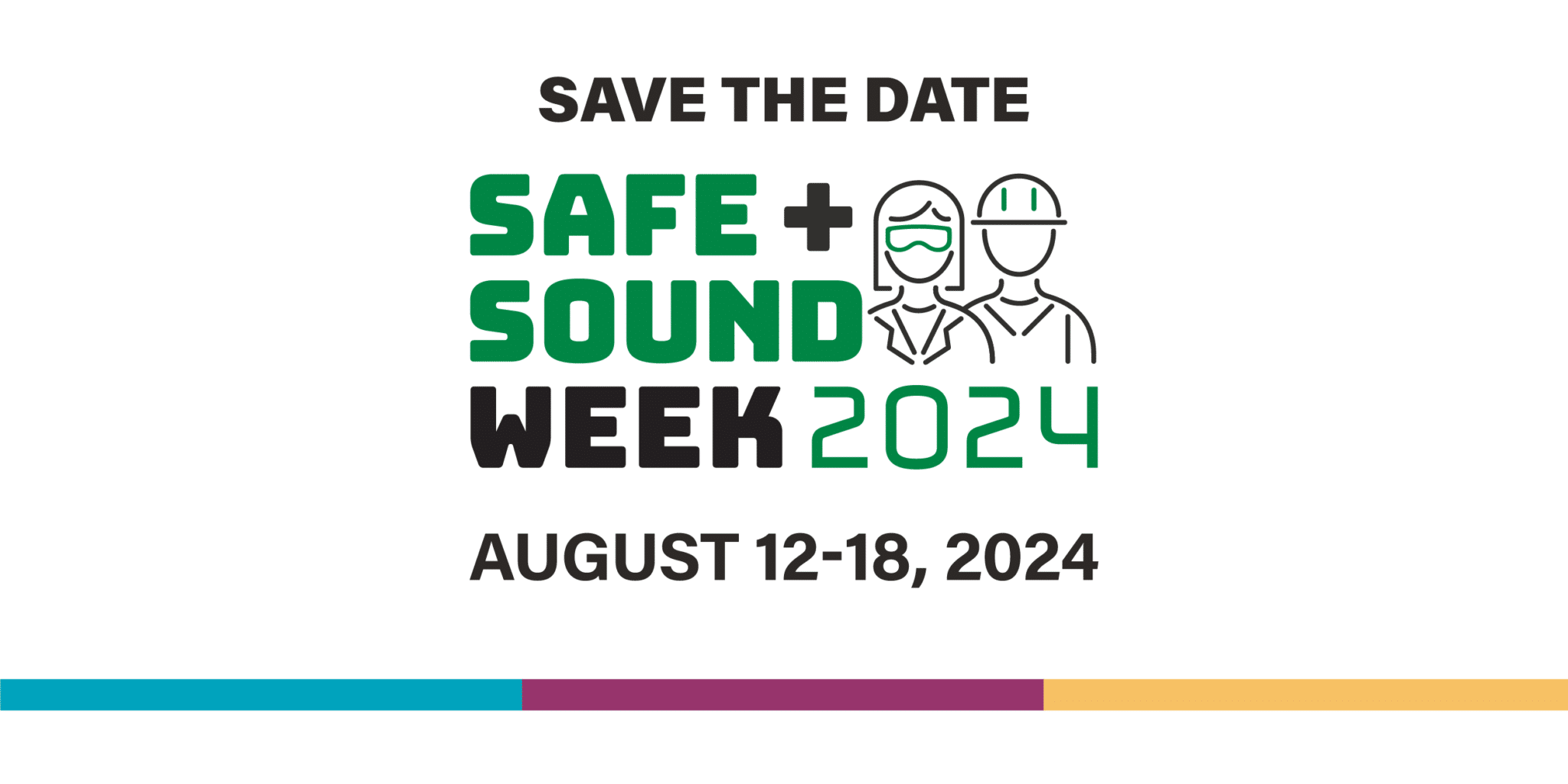
Participate in Safe + Sound Week 2024: August 12-18
All organizations looking for an opportunity to recognize their commitment to safety are welcome to participate. Last year, more than 3,900 businesses helped to raise awareness about workers’ health and safety! Safe + Sound Week is a nationwide event held each August that recognizes the successes of workplace health and safety programs and offers information and ideas on how to keep America’s workers safe. This year for Safe + Sound Week OSHA will be providing resources for businesses on Job Hazard Analysis (JHA).
OSHA is providing many ways to participate in Safe + Sound Week including several Core Element challenges this year. The challenges are grouped into Management Leadership Challenges, Worker Participation Challenges, and Find & Fix Hazards Challenges.
Management Leadership Challenges:
- Take 3 in 30 Challenge
- Lead With Safety Challenge
- Champion Safety Challenge
- Hazard Huddle Challenge
Worker Participation Challenges:
- All in on Safety Challenge
- Speak Up for Safety Challenge
- Safety is Our Right Challenge
Find & Fix Hazards Challenges:
- Check on Safety Challenge
- Eyes on Safety Challenge
- Halt a Hazard Challenge
- Safety Shuffle Challange
OSHA is providing a variety of resources for each of the challenges on its website so businesses can make the most of these challenges. Resources include worksheets, assessment tools, toolkits, posters, conversation starters, surveys, and challenge coins.
Successful safety and health programs can proactively identify and manage workplace hazards before they cause injury or illness, improving sustainability and the bottom line. Participating in Safe + Sound Week can help get your program started, energize an existing one, or provide a chance to recognize your safety successes.

Updated Hazard Communication Standard Effective July 19, 2024
With a significant revision to the Hazard Communication Standard (HCS) OSHA aims to better inform employees about chemical hazards in the workplace. The rule does this by improving the quality and accessibility of information on chemical labels and safety data sheets (SDS). Further, OSHA seeks to better align the HCS with the United Nations’ Globally Harmonized System of Classification, primarily Revision 7 (GHS), and improve alignment with other federal agencies and international trading partners.
History of the Hazard Communication Standard
The Hazard Communication Standard in 1983 gave the workers the ‘right to know,’ and the 2012 Globally Harmonized System ensured workers had the ‘right to understand.’ The original standard allowed chemical manufacturers and importers to convey hazard information on labels and material safety data sheets in whatever format they chose. However, the modified 2012 standard provided a single set of harmonized criteria for classifying chemicals according to their health and physical hazards and specifies hazard communication elements for labeling and safety data sheets. The updated Hazard Communication Standard tackles concerns identified since the 2012 update by addressing past issues and promoting alignment. Additionally, it fosters better alignment with other federal agencies and Canada, promoting a more unified approach to workplace chemical safety across North America.
Highlights of the Changes
- Enhanced Information on Labels and SDS
- Clearer Hazard Classification
- Improved Physical Hazard Classes
- Streamlined Precautionary Statements
With these changes, even labels on small containers will be more comprehensive and readable, so that workers have crucial hazard information easily available. The update also addresses trade secret concerns, while also ensuring critical safety information remains accessible on SDS. OSHA revised the classification process to provide complete and accurate hazard information on labels and SDS so that workers understand the chemicals they handle and make informed decisions. Updates to physical hazard classifications will better inform workers on the safe handling of explosives, aerosols, and chemicals under pressure. In addition, updated precautionary statements will provide clearer instructions on handling, storing, and disposing of hazardous chemicals. The updated standards are effective July 19, 2024, however, OSHA has established a phased set of deadlines for compliance.
Timeframe for Implementing Compliance
Compliance Date | Requirement | Who |
January 19, 2026 | Update labels and SDSs for substances | Chemical manufacturers, importers, distributors, and employers |
July 20, 2026 | Update workplace labels, hazard communication program, and training as necessary for substances | Employers |
July 19, 2027 | Update labels and SDSs for mixtures | Chemical manufacturers, importers, distributors, and employers |
January 19, 2028 | Update workplace labels, hazard communication program, and training as necessary for mixtures | Employers |
At National Safety Compliance we have a variety of Hazard Communication products to help businesses keep workers safe while handling hazardous materials including several video training courses, SDS binders, HAZCOM booklets, and several posters.

California leads the nation in efforts to prevent workplace violence.
In a historic move, Governor Gavin Newsom signed into law Senate Bill (SB) 553 creating the first general industry workplace violence prevention safety requirements in the United States. This groundbreaking legislation mandates a comprehensive Workplace Violence Prevention Plan (WVPP) for nearly all employers in California. The required WVPP can be built into an existing injury and illness prevention plan (IIPP). Employers are required to create or adopt, implement and train employees on the WVPP.
Effective July 1, 2024, this law is likely to be a landmark legislative move, as it is the first law of its kind nationwide to be applicable across various industries. Further, there is speculation it will be used as a template for similar laws across the country in coming years. The law incorporates many aspects beginning with developing the plan in cooperation with employees and others, regular training on workplace violence hazards, procedures for each element of the prevention plan, maintaining a detailed violent incident log, and conducting regular reviews of the WVPP. The enforcement of these requirements fall under the jurisdiction of California’s Division of Occupational Safety and Health (Cal/OSHA).
What is “workplace violence”?
Labor Code Section 6401.9 defines workplace violence as “any act of violence or threat of violence that occurs in a place of employment,” but does not include lawful acts of self-defense or defense of others.
Workplace violence specifically includes, but is not limited to, the following:
- The threat or use of physical force against an employee that results in, or has a high likelihood of resulting in, injury, psychological trauma, or stress, regardless of whether the employee sustains an injury.
- An incident involving a threat or use of a firearm or other dangerous weapon, including the use of common objects as weapons, regardless of whether the employee sustains an injury.
- Any of the following four types of workplace violence.
What are the Four Types of Workplace Violence?
- Type 1 violence: workplace violence committed by a person who has no legitimate business at the worksite and includes violent acts by anyone who enters the workplace or approaches employees with the intent to commit a crime.
- Type 2 violence: workplace violence directed at employees by customers, clients, patients, students, inmates, or visitors.
- Type 3 violence: workplace violence against an employee by a present or former employee, supervisor, or manager.
- Type 4 violence: workplace violence committed in the workplace by a person who does not work there but has or is known to have had a personal relationship with an employee.
What are the Essential Elements of a WVPP?
- Responsible Personnel: Designate individuals responsible for the WVPP, recommending more than one person for this role.
- Employee Input and Enforcement: Develop procedures for obtaining input from employees on the plan and its enforcement.
- Training Procedures: Establish comprehensive training procedures covering all aspects of the WVPP.
- Incident Reporting: Create procedures for reporting both potential and actual workplace violence incidents.
- Incident Investigation: Implement procedures for investigating potential workplace violence incidents and issues.
- Plan Implementation: Set procedures for the plan’s implementation, including periodic inspections, annual reviews, and ensuring comprehensive training for all employees.
- Anti-Retaliation Clause: Incorporate an anti-retaliation clause to protect employees who report workplace violence.
- Role Coordination: Develop procedures for coordinating roles between supervisors and management.
- Interdepartmental Communication: Establish communication procedures between departments or shifts, as necessary for specific job positions.
- Training Development: Focus on developing effective training procedures.
- Risk Identification: Identify environmental and other risk factors, including considerations for contingent workers, temporary staff, and remote employees.
- Risk Evaluation and Control Development: Create procedures for evaluating specific work-related risks (e.g., customer interactions, security roles) and developing appropriate controls, including engineering, administrative, and personal protective equipment.
- Recordkeeping: Implement procedures for maintaining records, including workplace violence incident logs.
- Post-Incident Response and Investigation: Establish emergency response procedures and investigation protocols for incidents that occur.
Employers are required to train employees on the WVPP when the program is first established, and then every year thereafter. The employee training required under the new law must cover particular subjects, allow for “interactive questions and answers,” and be in “vocabulary appropriate to the educational level, literacy, and language of the employees.” Further, as part of the training, employers also must provide employees with an opportunity for interactive questions and answers with a person knowledgeable about the WVPP. Additional training must take place when a new or previously unrecognized workplace violence hazard has been identified and when changes are made to the WVPP for clarity, this training may be limited to addressing the new hazard or change.
Training requirements
- The employer’s plan, how to obtain a copy, and how to participate in development and implementation of the WVPP.
- The definition of workplace violence and requirements of Labor Code Section 6401.9.
- How to report workplace violence incidents to the employer or law enforcement.
- Workplace violence hazards specific to the employer’s industry, corrective measures the employer has implemented, and strategies on how to prevent or respond to violence.
- The violence log required by the Labor Code and how to obtain a copy.
- An opportunity for interactive questions with a person knowledgeable about the plan.
What are employer responsibilities? Employers are required to take reasonable care to prevent and correct harassment. This includes having a comprehensive Workplace Violence Prevention Plan (WVPP). Key steps to demonstrating reasonable care include: Having a broadly disseminated policy. Establishing an effective complaint process. Providing regular training to ensure employees and supervisors and managers. Understand their rights and responsibilities. Monitoring the workplace to ensure adherence to the employer’s policy.
To help California employers meet this new regulation, and other employers throughout the country, NSC has updated its Workplace Violence Training Program to include the following:
- Impact of Workplace Violence
- Types of Workplace Violence
- OSHA and State Requirements for Workplace Violence (*NEW)
- Developing a Written Workplace Violence Plan (*NEW)
- Risk Factors for Workplace Violence
- Warning Signs of Workplace Violence
- Preventing/Reducing Workplace Violence
- Response Actions
- Training Employees on Workplace Violence (*NEW)