National Safety was extremely easy to work with. We found the training video that we wanted and it was shipped in a timely manner. The product purchased will be beneficial to our staff.
Search Results for: video
Slips, Trips, and Falls: Protect Your Employees from Preventable Injuries
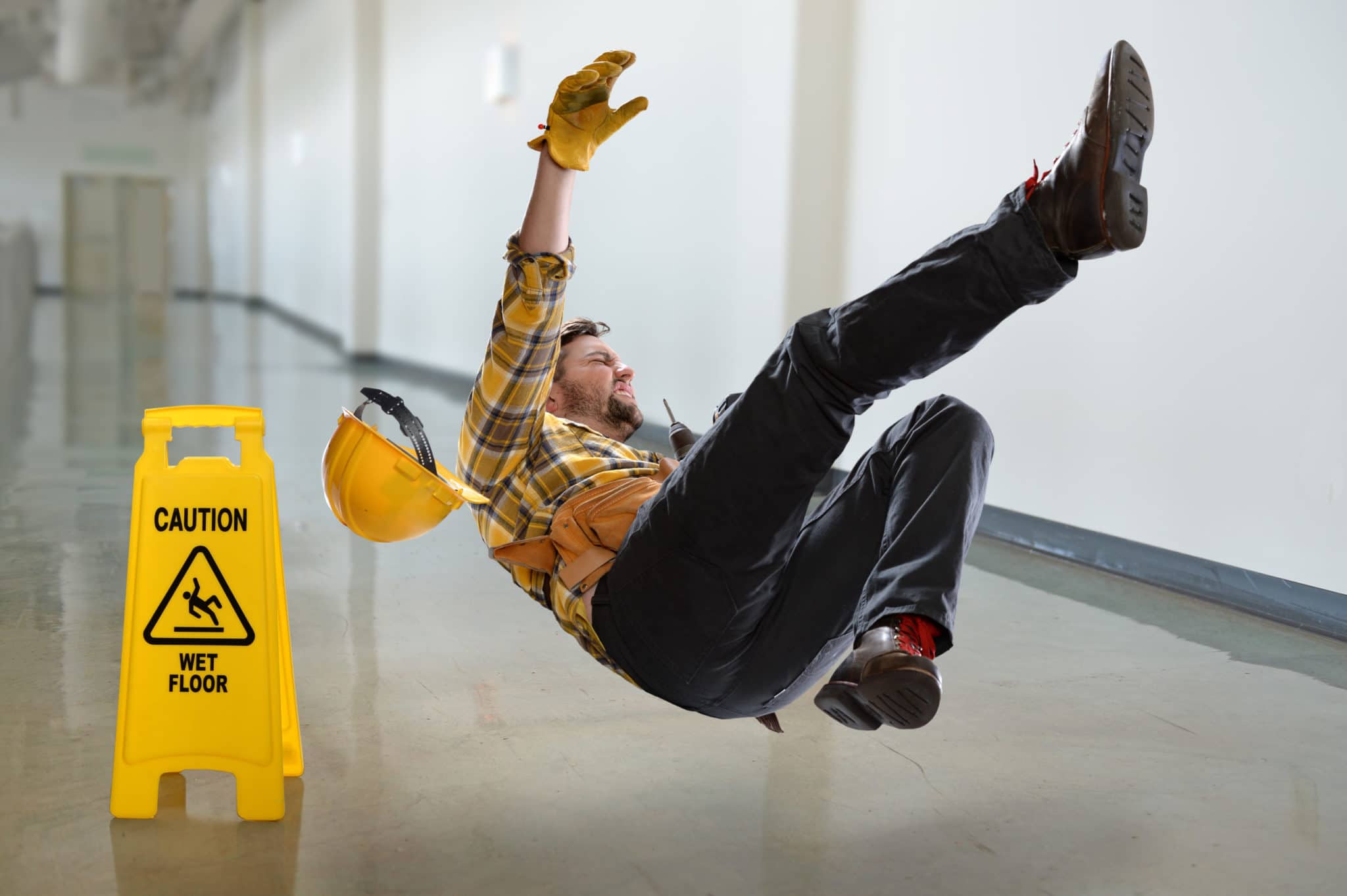
Slip and fall dangers are present in every workplace. When drafting your safety plans and protocols for most settings, it’s easy to focus on the more dramatic and dangerous hazards like fire safety, emergency training, or first aid. However, slips, trips, and falls are the second most common cause of injury at work. Shockingly, about 20-30% of people who experience a fall at work will suffer a moderate to severe injury, like deep bruising, a bone fracture, or a concussion.
Slips, trips, and fall hazards are sometimes easy to overlook because they tend to pop up unexpectedly. To maintain a safe workplace and protect your workers from preventable fall-related injuries, your safety plan should include strong protocols for footwear, signage, and housekeeping with training guidance and enforcement policies that instill safe attitudes and compliance within your employees.
OSHA Guidelines on Slips Trips and Falls
OSHA doesn’t have a set regulation about slips, trips, and falls, specifically. Instead, the bulk of the guidelines for this issue are contained in 29 CFR 1910 Subpart D Walking-Working Surfaces. This section of the Code of Federal Regulation covers both same-level falls and elevated falls, though, for this article, we will focus on same-level falls.
This important guidance went through a major overhaul in 2017 to better protect workers from hazards by adding important inspection requirements, clarifying standards, and aligning the guidance from 29 CFR 1910 General Industry with 29 CFR 1926 Construction as much as possible.
Another regulation that applies to slips, trips, and falls is 29 CFR 1910.36 and 37 Means of Egress which covers exit route safety. This standard outlines guardrail requirements, the importance of level walkways, and ice removal from exits to prevent slips.
Hazard Definitions
When we walk, our center of gravity shifts from side-to-side as we transfer our weight. With every step, there is a brief moment where our body is off-balance. When we encounter a slip or trip hazard at this moment, it can lead to a sudden fall.
Slips and trips both lead to falls. However, the difference between a slip and a trip hazard is specific and well-defined.
Slips
A slip occurs when there is too little traction between your foot and the surface that can cause a sudden loss of balance and potential fall. Slips occur on wet or oily surfaces, floors covered in fine dust or powder, or on ice.
Trips
A trip occurs when your foot or leg comes in contact with a hazard while walking. The momentum from the upper body continues to move while the tripped leg stays stationary for a moment, causing your body to fall. Trips can also occur when a person steps up or down and the surface is uneven or not at the height they expected.
Falls
When a slip or trip causes your center of gravity to shift unexpectedly, sometimes it isn’t possible to correct before the body collapses. This is when a fall has taken place.
There are two types of falls: Same level falls and elevated falls. A same level fall is when a person falls to the floor or against an object or wall. An elevated fall is when a person falls from above or below the floor, like from a ladder, scaffold, building, or into a hole.
Trip and Fall Prevention
The best way to protect your workers from these hazards is to prevent them whenever possible. Since slip and trip hazards often appear suddenly from hazards like spills or loose cables, everyone must remain vigilant to protect one another. It is the employer’s role to provide a safe workplace for all employees, so a watchful eye must always be maintained.
Footwear
Proper footwear is of the utmost importance to prevent slips and trips. This means shoes like sandals, open-toed shoes, canvas shoes, or high heels should be avoided in workplaces that often deal with slippery or uneven surfaces. Non-slip shoes or waterproof footwear can help your workers safely navigate wet or slick surfaces easily.
In-office environments where some workers choose to wear heels or sneakers, there are still precautions to take for proper footwear. Check for uneven surfaces or rugs that may snag a high heel and be sure to encourage that all employees keep their shoes snugly tied.
Signage
When a trip hazard or spill is present, signage is a great way to bring awareness to the new hazard. The trouble is many companies tend to leave their spill signs up far after the hazard is resolved or store it where it becomes part of the daily scenery.
When a sign is seen frequently, it becomes visual noise to your employees. It’s best practice to only put these signs out during the moment of danger and remove it as soon as the hazard is resolved.
Clean up spills and keep floors dry
Some of the most common causes of slips are workplace spills and wet floors. Whether the surface is wet from an accident or freshly mopped, always put out a sign as soon as possible to navigate your workers away from the wet surface. If there was a spill, it’s crucial to clean it up as soon as possible.
In wet environments like kitchens, it’s best practice to put down something to improve traction like anti-skid tape or slip-resistant mats.
Housekeeping
Anything in a walking path that could catch a foot or cause a loss of traction is a potential slip or trip hazard. Cables across walkways, paper on the floor, boxes, or hoses can all cause a dangerous accident. Items should never be left on the floor and it is important for employers to continuously check for hazardous clutter.
Encourage frequent cleaning of all work areas, including a company culture that closes drawers, puts boxes away, and hides cables in protective covers if they must extend into walking areas.
Proper lighting
Especially when navigating uneven or wet surfaces, your employees need their workplaces to be well lit to avoid falls. If they can’t see the dangers around them, how can they be expected to avoid them? Adequate lighting is required not only on the work floor, but anywhere your employees are expected to walk including stairs, halls, ramps, and exits.
Plans and protocols
Each of these methods of prevention should be written in your safety plan as company protocol that each worker has easy access to. For your slips, trips, and falls safety plan to work well, each employee must maintain a safe attitude during their daily work and act on resolving any slip or trip hazards in their area.
Importance of slips, trips, and falls training
Proper training for hazard awareness is the most effective way to avoid slip or trip injuries. Any safety orientation training or refresher course should include a reminder of the types of slip or trip hazards your workers may encounter at your facility, as well as how to safely navigate them.
Creating a culture of safety can help each worker feel comfortable pointing out a potential hazard and act on protocols to prevent injuries or incidents without hesitation. Help your workers recognize these hazards confidently with clear and frequent training. If incidents in your facility do occur, reevaluate your safety plan after you conduct an incident investigation to find methods to improve your implementation of crucial slip, trip, and fall prevention.
Ready to prevent slips, trips, and falls in your workplace? NSC makes training easy.
Our all-in-one video training kit on Slips, Trips, and Falls are available for General Industry or Construction and come with everything you need to train your employees.
A Quick Guide to HIPAA Compliance Training Requirements for Employers
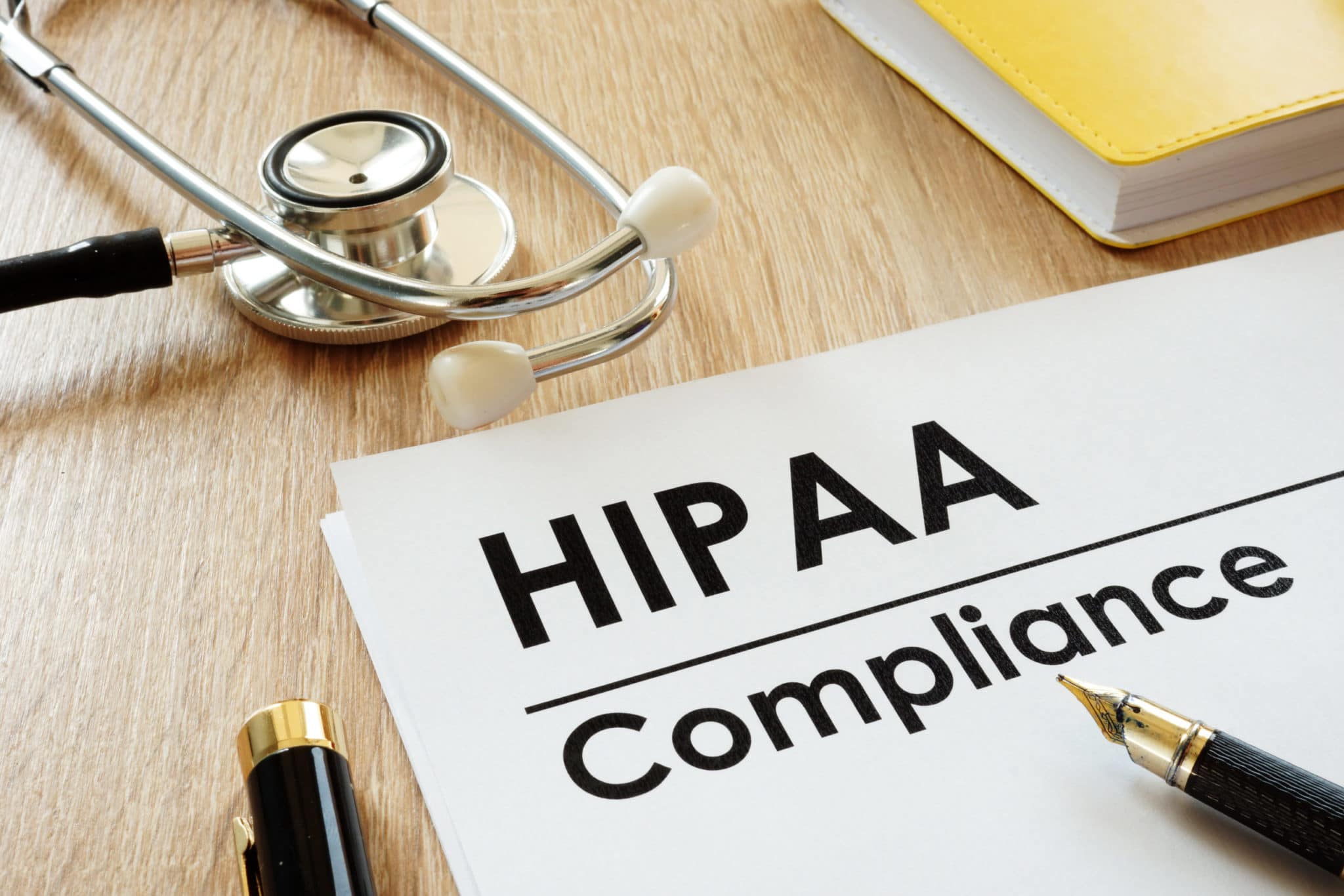
To most, HIPAA compliance boils down to a simple concept: the security of patient medical information and data. With these guidelines in place, patients expect their medical data will remain private and protected from prying eyes or theft. It is your responsibility, if your company works with protected patient information, to ensure that your employees are properly implementing HIPAA compliant procedures.
A lot goes into designing HIPAA compliance training. While training should be tailored to the individual jobs at hand, there is plenty about HIPAA that every relevant worker should know. If you’re planning a class and need a simple to use HIPAA training kit with an instruction video, lesson plan, PowerPoint Presentation and certification test: we’ve got you covered.
What is HIPAA?
The Health Insurance Portability and Accountability Act, or HIPAA, is a federal law designed to protect patient health information from being disclosed without the patient’s consent or knowledge. HIPAA encompasses not only the original act but several subsequent legislative acts and together they form a vast number of regulatory requirements for a variety of entities.
What industries require HIPAA training?
The simple answer is that HIPAA regulations will apply to Covered Entities and their Business Associates. Basically, anyone who could possibly come in contact with protected health information should receive HIPAA training. This includes more obvious healthcare roles like doctors, nurses, medical receptionists and hospital recordkeepers. However, there are roles outside of the traditional healthcare system who also should be trained in HIPAA regulations.
What is a covered entity?
- Healthcare providers, including but not limited to clinics, hospitals, and private practices for medical, dental, psychological, chiropractic, etc.
- Health insurance providers, including but not limited to health insurance companies, HMOs, company healthcare plans, Medicare and Medicaid.
- This section also includes the staff that handles the sign-up process for employees or students at their company for health plans—oftentimes, these are human resources professionals.
- Healthcare Clearing House
What is a business associate?
Covered entities often work with vendors or subcontractors to handle important tasks like data storage, networking or other information technology services. Other vendors or subcontractors could include companies that provide shredding services of sensitive documents, lawyers, translation services, medical equipment professionals, answering or reception services, consultants.
With those definitions in place, let’s look at what HIPAA says about required training in the regulatory code text. The training section in the Privacy Rule states a covered entity must train all member of its workforce on the policies and procedures as necessary and appropriate. Any covered entity or business associate employee, with potential access to protected health information (PHI), must be provided regular training. The Security Rule states covered entities and business associates must implement a security awareness and training program for all members of its workforce.
What topics should be covered in HIPAA training?
HIPAA takes a somewhat vague approach to training. The law does not give specifics about required training. So, the implementation of specifics of HIPAA requirements are considered “addressable,” which simply means they must be followed but provide covered entities a level of flexibility in how they comply with the standard.
Covered entities must decide whether a given addressable implementation specification is reasonable and appropriate security measures apply within their framework. Their decisions must be documented in writing and the written documentation should include factors considered as well as the results of the risk assessment on which the decision was based.
With that documentation in place, training can be conducted with a “custom-fit” approach. It is important to train employees on many aspects of the HIPAA regulations, but the training does not have to be comprehensive on all topics. Ideally, training should be more about the company policies and procedures to ensure compliance with HIPAA law. Even so, there are some basic HIPAA components which should be covered including the following:
Important HIPAA training topics
- The HIPAA Privacy Rule
- The HIPAA Security Rule
- Patients’ Rights
- Rules on PHI disclosures
- Safeguarding electronic PHI or ePHI
- Preventing HIPAA Violations
- Breach Notifications
- Compliance and Enforcement
There are additional areas on which employees might need training. Ultimately it is up to the covered entity to determine the topics covered and make sure their employees are trained, and compliance with HIPAA is happening.
When should employees receive HIPAA training?
The Privacy Rule states that HIPAA training is required for “each new member of the workforce within a reasonable period of time after the person joins the Covered Entity’s workforce” and also when “functions are affected by a material change in policies or procedures” – again within a reasonable period of time. This implies training should occur the first few days and not months later.
How often is HIPAA training required?
According to the Security Rule, HIPAA training is required periodically. Most covered entities meet this requirement by holding annual training sessions. Annual training helps to protect the employer and employees by ensuring employees are:
- “Refreshed” on HIPAA regulations
- Aware of any policy changes that may have occurred since their last training session
- Knowledgeable about cybercrime and ways to protect against it
While annual training is sufficient to meet HIPAA’s periodic requirements, holding additional training sessions throughout the year is not a bad idea. These other sessions can be shorter and provide quick info to reinforce employee’s knowledge and compliance with HIPAA.
Tips for HIPAA compliance training
An effective HIPAA training program allows employees to participate in the training process and to practice their skills or knowledge. This will help to ensure they are learning the required knowledge or skills. Employees can become involved in the training process by participating in discussions, asking questions, contributing their knowledge and expertise, learning through hands-on experiences, and through role-playing exercises.
Steps can be taken to help ensure employees are attentive and engaged during HIPAA training.
- Keep training sessions under an hour in length. Long training sessions lose the attention of the trainees.
- Keep the employees engaged. Asking questions and encouraging conversation helps to keep employees plugged-in to the training session.
- Keep handouts to a minimum and make sure the ones you hand out are meaningful. Too many handouts will draw the employee’s attention away from what is currently being discussed.
- Include various media for different learning types, including videos, classroom presentations, quizzes and discussion.
- Make HIPAA compliance training simple
HIPAA compliance requires frequent and effective training that gives your employees the tools and knowledge they need to implement these critical guidelines in their everyday work. The best HIPAA training courses will combine interactive elements with classroom lecture and discussion to help your employees learn and implement these crucial guidelines.
Ready to train your employees? NSC makes HIPAA compliance easy. Our all-in-one HIPAA Compliance training course contains everything you need to run a successful class, including a training video developed by industry experts, classroom presentation, supplemental handouts and printable certificates. This course is available on DVD, digital access, or in a self-guided online training course.
Products
With a wide range of safety training products and resources, National Safety Compliance is a go to source for training and compliance needs. Our products include video training kits, online courses, DVDs/USBs, streaming subscriptions, and safety posters. Training resources cover various topics such as aerial lift safety, asbestos hazards, bloodborne pathogens, confined space entry, crane safety, drug and alcohol abuse, electrical safety, emergency planning, ergonomics, excavation and trenching, eye safety, fall protection, fire safety, first aid, food safety, forklift safety, and more.
Privacy Policy Archive
National Safety Compliance only collects personal information when you request our services and only uses the information collected to provide those services for you. If you choose to make a purchase, you will be asked to provide contact information (such as your name and shipping address) and financial information (such as your credit card number and expiration date). This information is used for billing purposes and to process your order. National Safety Compliance handles all of this data with the utmost confidentiality.
Collection of Information & Use
When visitors leave comments on the site we collect the data shown in the comments form, and also the visitor’s IP address and browser user agent string to help spam detection.
An anonymized string created from your email address (also called a hash) may be provided to the Gravatar service to see if you are using it. The Gravatar service privacy policy is available here: https://automattic.com/privacy/. After approval of your comment, your profile picture is visible to the public in the context of your comment.
Cookies
If you leave a comment on our site you may opt-in to saving your name, email address and website in cookies. These are for your convenience so that you do not have to fill in your details again when you leave another comment. These cookies will last for one year.
If you have an account and you log in to this site, we will set a temporary cookie to determine if your browser accepts cookies. This cookie contains no personal data and is discarded when you close your browser.
When you log in, we will also set up several cookies to save your login information and your screen display choices. Login cookies last for two days, and screen options cookies last for a year. If you select “Remember Me”, your login will persist for two weeks. If you log out of your account, the login cookies will be removed.
If you edit or publish an article, an additional cookie will be saved in your browser. This cookie includes no personal data and simply indicates the post ID of the article you just edited. It expires after 1 day.
Embedded content from other websites
Articles on this site may include embedded content (e.g. videos, images, articles, etc.). Embedded content from other websites behaves in the exact same way as if the visitor has visited the other website.
These websites may collect data about you, use cookies, embed additional third-party tracking, and monitor your interaction with that embedded content, including tracking your interaction with the embedded content if you have an account and are logged in to that website.
OSHA-Compliant Forklift Safety Training Standards

Powered industrial trucks, commonly known as forklifts, are used in a variety of industries. From manufacturing plants to warehouses to construction sites, forklifts are critical pieces of workplace equipment used to raise, lower, and move materials. With their presence being so commonplace it is no surprise how many employers are interested in understanding and providing compliant, effective training for their employees.
Forklift safety training is not only essential for a safe working environment but required under the most recent OSHA regulations. Forklifts are an exceptional tool for efficiency, but they can also be dangerous, damaging, or even deadly. According to a report from the U.S. Bureau of Labor Statistics, more than 600 workers perished in forklift accidents from 2011 to 2017, and a further 7,000 suffered injuries that required time away from work.
To start on the path towards developing forklift safety training for your team, you must first understand the OSHA regulations and how to put these rules into action.
Most Recent OSHA Regulations for Forklift Operators
The most recent OSHA regulations for forklift operators were officially published on December 1, 1998. In response to a rise in workplace safety concerns, the new standard was designed to lower workplace injuries and fatalities through quality operator training.
These new regulations went into effect on March 1, 1999 and apply to all industries except for agriculture.
The new regulations are as follows:
- Operator performance must be evaluated before operating an industrial truck, except for when in training
- The employer can designate any employee who is qualified as a Trainer or Evaluator. There are no special requirements for training.
- OSHA does not certify, accredit, or approve any trainers or training programs for powered industrial trucks. The responsibility for compliance with the requirements of the OSHA standard rests with the employer.
In summary: All employers with forklifts or powered industrial trucks outside of agricultural settings must provide OSHA-compliant training for their operators, evaluate operator performance before allowing them to operate the vehicle, and can designate any qualified employee to act as a trainer or evaluator.

Forklift Trainer Requirements Under OSHA Regulations
Under the guidance of OSHA regulations, ensuring that your forklift operators are properly trained is ultimately the responsibility of the employer. This task can be outsourced to outside consultants or pre-developed courses for the classroom portion can be utilized. However, the training provided must adequately prepare your employees for not only general forklift operation, but the unique challenges present in your specific workplace.
Forklift Training Format
Training programs must consist of a combination of formal or classroom-type instruction, using tools such as:
- Lecture formats
- Video formats
- Class discussions and games or activities
- Written materials, worksheets, or training booklets
- Online interactive training
Training must also include a practical, hands-on approach, such as:
- Demonstrations performed by the trainer
- Practical exercises performed, with supervision, by the trainees
- Evaluation of the operator’s performance in the workplace
Trainees participating in hands-on activities can only operate the vehicle as long as it does not endanger them or other employees. This means during the practical portion of training, a safe location should be secured and designated as such to minimize the presence of others in the area. The trainee must also remain supervised at all times during operation until they are certified.
Training Content
The content of the training program must consist of several topics, such as location-specific hazards and truck-specific topics. If operators are going to use different types of forklifts, they must be trained on each vehicle class or type.
Workplace-specific training
Your training plan must include hands-on and written instruction about the vehicles or workplace hazards specific to your place of business. If your business has multiple locations in which the operators will be using forklifts, they must be trained on the hazards that are unique to each of the locations.
Topics for this portion of the training must include:
- Surface conditions where the vehicle will be operated
- Composition of loads to be carried and load stability
- Load manipulation, stacking, and unstacking
- Pedestrian traffic in areas where the vehicle will be operated
- Narrow aisles and other restricted places where the vehicle will be operated
- Hazardous (classified) locations where the vehicle will be operated
- Ramps and other sloped surfaces that could affect the vehicle’s stability
- Closed environments and other areas where insufficient ventilation or poor vehicle maintenance could cause a buildup of carbon monoxide or diesel exhaust
- Other unique or potentially hazardous environmental conditions in the workplace that could affect safe operation.
Truck-related topics
Training must go beyond the basic operation of the industrial powered truck and include comprehensive information about the vehicle’s controls, capacity, maintenance, and precautions.
Topics for this portion must include:
- How to read and understand the forklift’s required name plate / data plate and find vital information such as fuel type and capacity
- Operating instructions, warnings, and precautions for the types of truck the operator will be authorized to operate
- Differences between the truck and an automobile
- Truck controls and instrumentation: where they are located, what they do, and how they work
- Engine or motor operation
- Steering and maneuvering
- Visibility (including restrictions due to loading)
- Fork and attachment adaptation, operation, and use limitations
- Vehicle stability
- Any vehicle inspection and maintenance that the operator will be required to perform
- Refueling and/or charging and recharging of batteries
- Operating limitations
- Any other operating instructions, warnings, or precautions listed in the operator’s manual for the types of vehicle that the employee is being trained to operate
Vehicle class-specific training
There are many types of forklifts used. If your business owns multiple types, operators do not need to be trained on each make and model. But, operators must receive truck-specific training on those types they will be expected to operate. Operators trained to use a sit-down type fork truck cannot operate a stand-up truck unless they have been trained to operate it.
The vehicle classes for powered industrial trucks are as follows:
Class I: Electric motor rider truck
These general use vehicles are most often found indoors, though varieties with pneumatic tires are sometimes used outdoors in dry conditions. These vehicles are versatile and protect air quality by running on battery instead of gasoline, natural gas, or diesel fuel.
Class II: Electric motor narrow aisle trucks
These narrow vehicles are designed to operate in small spaces efficiently. Narrow forklifts allow for their companies to pack in shelving or aisles close together to maximize storage area.
Class III: Electric motor hand trucks or hand rider trucks
These small vehicles battery-powered vehicles are driven by an operator in front of the truck. Steering and controls are contained in the tiller.
Class IV: Internal combustion engine trucks with solid, cushion tires
These forklifts are often seen couriering pallets from the loading dock to indoor storage. They feature a low clearance thanks to their smaller profile tires and can be used indoors or outdoors on smooth surfaces.
Class V: Internal combustion engine trucks with pneumatic tires
These trucks feature an internal combustion engine that is powered by compressed, diesel or LP gas. They are versatile and seen in all kinds of warehouses, from large to small.
Class VI: Electric and internal combustion engine tractors
These electric and combustion-powered tractors are known for their pulling power and are commonly seen on the airport tarmac hauling luggage.
Class VII: Rough terrain forklift trucks
Popular in construction, these large forklifts are designed for heavy outdoor use at a job site to lift and transport large loads of lumber or building materials.
Vehicle Inspection Training
According to OSHA guidelines, forklifts need to be inspected either daily or at the end of every shift if they’re used continuously. Before any driver begins work for the day, they must perform both a walkaround inspection and a seated inspection. In order for employees to properly perform this inspection, they must be formally trained on hazards and where to look for them.
Walkaround inspection
The walkaround inspection involves checking major areas of the vehicle, such as the tires, hoses & belts, fluids, forks, engine, and data plate for safety and good condition.
Seated inspection
The seated inspection is performed while the driver is in their seat. They must check that the controls, safety equipment, horn, brake, steering, seatbelt, and gauges are all in safe, operating condition.
Training the Trainers
OSHA’s regulation CFR 1910.178 (l) Operator Training spells out clearly what you need to do to correctly train employees to use forklifts.
While OSHA does not require special training or certification for forklift trainers or evaluators, they must be qualified for the task. Ensure that your operator training is conducted by someone who has the knowledge and experience to educate powered industrial truck operators and evaluate their competence.
In some cases, this may mean you will want to hire an outside training consultant. In many instances, however, this is not necessary. While outside trainers are certain to have the skill and expertise to train your employees, this does not mean you must hire an outside training consultant or company. Depending upon your circumstances it may be better if you do, but it is not required by OSHA. You simply must ensure that the person conducting the training “has the knowledge, training, and experience to train.”
Timing of forklift training
New operators
Operators with no certification must complete the full training program before operating a forklift. Until they are certified, they can only operate the vehicle under direct supervision while participating in the training.
New employees
Experienced operators who are new to your company and bring with them an outside certification are not necessarily required to go through the full training course. Instead, if you have reason to believe their training is sufficient, you can simply evaluate their skills and train them on only workplace-specific tasks, hazards, and vehicles.
Deficient operators
Deficient operators must go through refresher training when the following occurs:
- The operator has been observed to operate the vehicle in an unsafe manner
- The operator has been involved in an accident or near-miss incident
- The operator has received an evaluation that reveals that the operator is not operating the truck safely
- The operator is assigned to drive a different type of truck
- A condition in the workplace changes in a manner that could affect the safe operation of the truck.
To ensure that the workplace incident was not because of faulty guidance, an evaluation of the entire training program must be performed when refresher training is required.
Seasoned operators
Current OSHA regulations require an evaluation of each forklift operator’s performance at least once every three years. If the operator continues to perform safely and within the guidelines set by your training, no further classwork is required at that time.
Temporary employees
Employees that join your company through a contractor or temporary agency must still be certified to operate a forklift. Since temporary agencies are the employer of your temporary employee, not the host organization, it is the responsibility of the agency or contractor to provide training to the required standard or there must be an agreed-upon plan for providing training between your business and the agency.
If the agency is the one to provide training, your business must still train temporary employees on workplace-specific vehicles and hazards.
Minors
Under no circumstances is a minor allowed to operate a forklift. This is a violation of federal law. All operators must be over the age of 18 before beginning training.
Certification document requirements
OSHA also requires that you certify that each operator has been trained and evaluated. Many folks misunderstand this and think that training must be OSHA-certified. OSHA does not certify your training. This simply means you must document that training was provided and that the training met the requirements laid out in section (l) of the CFR 1910.178. To certify the training, you must document:
- The name of the operator
- The date of the training
- The date of the evaluation
- The identity of the person(s) performing the training or evaluating the training.
Employer training records
Records of training, performance, and certifications should be kept for at least the duration of employment.
Forklift training under OSHA guidance is one step towards creating a safer workplace for all employees. With some knowledge of OSHA’s requirements, thoughtful classroom planning, and seasoned workers with the skills to train, you will find this process is mostly straightforward. By the end of the training, you should be confident that your operators understand the training they have received and can safely operate the vehicle and have thorough documentation of the training provided.
For our Forklift Safety Training Kits on DVD, USB, or Digital Access visit: https://www.osha-safety-training.net/product-category/topic/subject-forklift-safety/
For our Forklift Safety Training via online LMS visit: https://www.onlineoshatraining.net/product/forklift-safety-training-general-industry/
Training Employees to Properly Use PPE in 2020

What Does PPE Stand For?
Personal protective equipment (PPE) is essential for those working on the frontlines of the COVID-19 pandemic. In general, PPE protects wearers from environmental hazards that could cause injury or illness. These hazards include physical, chemical, radiological, electrical, mechanical, and biological damage. During the current coronavirus pandemic, wearing PPE significantly reduces the chance of being exposed to or spreading germs by creating a barrier between yourself and possible infectious diseases. We offer complete PPE Training Kits here at National Safety Compliance.
2020 has Seen an Unprecedented Increase in PPE Usage
While the use of PPE in all workplaces across the world is certainly spiking, PPE is nothing new for most health care workers. In the past, all hospital staff members and visitors have been required to use PPE in instances where there is potential for contact with blood or bodily fluids. Now, PPE is required around the clock in hospitals as well as other businesses and facilities across the nation to prevent the transmission of the novel coronavirus COVID-19.
For PPE to work effectively, employers must properly train their workers on how to use PPE efficiently. If PPE is something only used rarely, employees should still practice regularly putting on, properly wearing, and taking off their personal protective equipment. This proper training is a must, and employees should be refreshed on these topics on a regular basis.
With the addition of new businesses needing to implement requirements for PPE, there are also many different types of PPE to meet the needs of each industry. These can range depending on your line of business. For example, the PPE that a hospital utilizes will be much different than the PPE used in a restaurant. The different forms of PPE can include;
- Masks and Respirators: These should always cover both your mouth and nose to prevent the inhalation of germs, chemicals, and physical contaminants. Masks also play an important part in stopping asymptomatic employees from spreading disease.
- Eye protection: Some masks come with a clear plastic piece to cover your eyes, other forms of eye protection can include face shields and goggles. These are important in some settings because of how easily germs and other particles can enter through or damage one’s eyes.
- Gloves: Wearing gloves protects your hands by creating a physical barrier. It’s important to avoid touching the body or face while wearing protective gloves, and regularly change them after any possible contamination.
- Clothing: This includes much of what you would picture a surgeon wearing; gowns, aprons, head covering, and shoe covers and while they are often used during surgeries, they can also be used to visit someone who is in isolation or to keep dangerous liquids from touching your skin. Clothing can also be used in other industries outside of the medical field like chemical protective suits for cleaning, reflective vests for outdoor night workers, and lead aprons for radiological workers.
Depending on your local and state mandates, you as an employer can control how often employees are required to wear PPE in certain situations. This can depend on your risk of being severely impacted by COVID-19, but regardless of these requirements, healthcare workers always need PPE when caring for others in isolation. PPE is also essential for confirmed patients to prevent the spread of the disease to others and for healthcare workers to avoid getting the disease themselves. Informational posters can help improve PPE compliance among employees.
Properly Using PPE
Simply wearing PPE is not enough. In order to properly protect yourself and those around you, you must also put on, remove and dispose of PPE safely. Different facilities and industries will have different procedures for properly completing each of these steps so follow these simple guidelines and practice your workplace guidelines.
- Sanitize and Inspect: To properly don PPE, you will want to sanitize your hands before touching any of the equipment and then ensure that the size is correct. If your mask, gown, or gloves do not fit they will not work effectively.
- Put Your PPE on in the Proper Order: You can then put on your mask by hooking them appropriately to your ears so that it covers both your nose and mouth. Following this, you can tie your gown, put on a face shield or goggles and then your gloves. Once you have all of your PPE properly in place you can then enter into the infected area.
- Remove Some PPE Before Leaving the Contaminated Area: Before leaving you should remove the PPE by first starting with your gloves. These should be carefully removed to avoid contaminating your hands by placing one glove in the other one. Then remove your gown by carefully untying it and avoiding any forceful movements. Place these items in the proper disinfection or disposal area.
- Remove Remaining PPE and Sanitize After Leaving: you can then leave the area, use hand sanitizer immediately and then remove your face shield or goggles by gently pulling them away from your face without touching your eyes. To remove your mask, you should carefully untie it and avoid touching the front before using hand sanitizer once more.
- Disinfect or Dispose of Remaining PPE: If you are reusing any of these materials it is important that you clean and disinfect them, as well as any other materials they touched, before using them again. If not, you should place them directly in the trash bin.
Regulations on Supply
The need for PPE has greatly increased due to the pandemic and has caused many shortages. This has created a surge capacity that is challenging the U.S. healthcare system’s ability to identify alternative methods of patient care.
In response, the CDC is working to optimize the use of PPE by helping facilities understand their PPE inventory, supply chain, and utilization rate. It is also vital that facilities communicate with local healthcare to identify supplies and implement conventional capacity measures.
This communication should take place across the nation between state and local departments and partners to develop how to implement strategies that can extend PPE supplies and to properly train on PPE use and optimization strategies so that all communities are educated on the use of PPE.
National Safety Compliance has the information you need to inform your employees and community members on how to utilize and optimize PPE so that you are safely using PPE and still have it when you need it the most. We offer PPE Training Programs on DVD, USB, or Digital Access in English and Spanish here on our OSHA Safety Training website. These training kits come with instructional videos, trainer’s guides, PowerPoint presentations, compliance guides, employee quizzes, completion certificates, and wallet cards. If you would rather your employees train via module, our online LMS version of or PPE Safety Training is also available in English and Spanish on Online OSHA Training.
How to Prepare for National Safety Stand-Down to Prevent Falls in Construction Week

On average, there are more than 100 worker fatalities per week (or approximately 14 deaths each day) in the United States according to 2018 data. Out of the total number of worker fatalities, more than 20% (or one in five deaths) are from the construction industry.
So, what is the leading cause behind construction-related work fatalities? If you guessed falls, you are correct. According to the Bureau of Labor Statistics, falls from elevation accounted for 320 of the 1,008 construction fatalities in 2018. Behind falls, being struck by an object, electrocuted, or caught in or between equipment, objects or materials are additional top factors. Together, these leading causes are what is known in the construction industry as the “Fatal Four.”
Because falls are the most hazardous element of the construction industry, each year the U.S. Department of Labor’s Occupational Safety and Health Administration (OSHA) in partnership with additional safety organizations host the National Safety Stand-Down to Prevent Falls in Construction.
What is the Background on National Safety Stand-Down to Prevent Falls in Construction?
National Safety Stand-Down to Prevent Falls in Construction was first introduced on Workers Memorial Day in 2012 in remembrance of those who have been killed or injured by their job. The voluntary event was originally planned to continue annually for two years with the goal of raising awareness of fall fatalities and injuries along with reducing the risk of these preventable accidents.
However, due to the massive success of National Safety Stand-Down to Prevent Falls in Construction, it has since become an annual event that occurs each May surrounding the launch of construction’s busy season. Due to the coronavirus pandemic, this year’s seventh annual event was rescheduled to Monday, Sept. 14 – Friday, Sept. 18, 2020. Now, more than 150 public events are held each year across the 50 states as well as internationally. Since its introduction six years ago, OSHA’s fall prevention Stand-Down events have reached more than 10 million industry workers.
Who Can Participate in a Stand-Down Event?
Construction is the number one at-risk industry for falls while on the job, however, there are many others that can and should participate in a Stand-Down event. For example, additional industries such as manufacturing, transportation and agriculture regularly require employees to work from elevated heights. OSHA encourages any company that is potentially impacted by falls to host a Stand-Down event. In the past, OSHA has seen a wide variety of participants including construction companies, contractors, the U.S. Military, unions, trade associations, safety equipment manufacturers and many more.
Additionally, a Stand-Down event can be held no matter the size of your company, with approximately half hosted by small businesses with 25 employees or less. In fact, small business participation is particularly important. According to data from the Center for Construction Research and Training, 61% of fatal falls in construction happened in companies with 10 employees or fewer between 2011-2015.
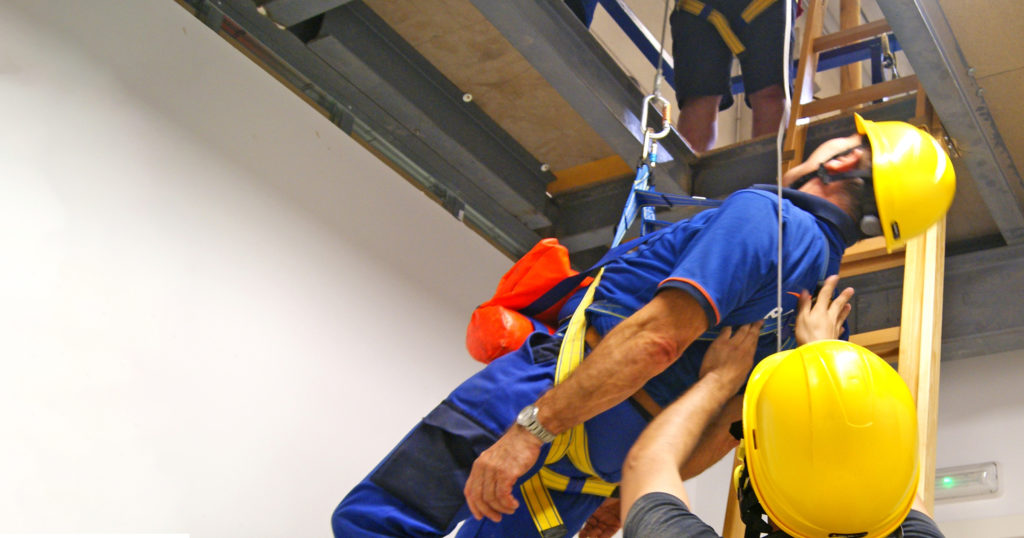
What Are Common Examples of Stand-Down Events?
There are a myriad of ways to conduct a Stand-Down event, and employers are encouraged to consider what will work best to fit their particular needs. You may choose to host one event, or provide ongoing training throughout the week of Sept. 14-18. In light of COVID-19, OSHA asks employers to ensure that events are held while practicing safe social distancing in small groups or even virtually.
Here are some popular examples on how to host a Stand-Down event:
- Conduct a safety demonstration on fall protection equipment.
- Host a toolbox talk (or informal group discussion) on fall-related hazards.
- Hold a training session on your company’s safety policies, goals and expectations.
- Lead a safety inspection with employees.
- Develop a rescue plan.
- Show a safety video.
How Do I Prepare for a Stand-Down Event?
OSHA provides step-by-step instructions to help you prepare for a successful event, which include:
- Start early and designate a Stand-Down coordinator to organize your event(s).
- In addition to jobsite workers, invite all relevant stakeholders involved in your business to participate (for example, subcontractors, architects and engineers).
- Review your current fall prevention efforts. Consider what falls could happen, what training and equipment you have already provided, and what areas could use improvement.
- Decide what type of event will work best for your particular needs, whether it be a presentation, video or hands-on activity. Tip: hands-on activities such as a jobsite inspection or safety equipment check can help with employees’ retention of the information.
- Choose when and for how long to hold your event, such as during a break, lunch or scheduling another designated time. Events can range from as simple as 15 minutes to several hours over the course of the week depending on your preference and needs.
- Promote your Stand-Down event to employees in the medium they prefer to receive information (for instance, in-person, via email or through flyers). Tip: offering snacks has shown to increase event participation. You can also submit your free public event to be featured on OSHA’s website and see what other events are happening in your area.
- Hold your event and create a positive, safe space for employees to engage by asking questions and offering suggestions along the way.
- Finally, implement learnings from your Stand-Down event into your current policies and procedures to make your work environment even safer moving forward.
What Materials Are Available to Help With My Stand-Down Event?
Since our founding in 1999, National Safety Compliance has been committed to providing affordable, reliable and effective training products for American workers—including fall safety. Designed to help employers comply with OSHA regulations, our safety training programs can help companies reduce workplace accidents.
With plenty of easy-to-use, cost-effective options, we have a variety of resources to assist with your Stand-Down event, such as:
- Fall Protection Safety Trainings: Easily train new employees or provide a refresher with a host of digital tools including a 26-minute fall protection safety video, PowerPoint presentation, employee quiz and additional materials. You can purchase digital access to the training with flexible rental options of 7 days, 30 days or 1 year. Additionally, digital access in a Spanish version is available. Or, purchase a Fall Protection Training video kit on USB or DVD that provides the same materials in a DVD or USB format that is also presented in an English or Spanish option.
- Fall Protection Training Booklets: This 16-page booklet serves as a complementary resource to our training program. For example, it covers topics such as safety nets, covers, safety monitor systems, falling object hazards and more.
Additionally, OSHA offers a host of resources to assist with your Stand-Down event. Assets include the following in a variety of languages such as English, Spanish, Russian and Portuguese:
- Posters
- Fact Sheets
- Stickers
- Cards
- Infographics
- Quizzes
- Lesson Plans
- Videos
What Do I Do After My Stand-Down Event?
Participants are encouraged to share their Stand-Down events with #StandDown4Safety on social media. After completing your Stand-Down event, employers can download a certificate of recognition from the U.S. Department of Labor to acknowledge the time and effort spent improving fall safety within their company. The page to download your certificate will become active beginning Sept. 14 on OSHA’s website.
Want More Information?
If you would like additional information on this year’s National Safety Stand-Down to Prevent Falls in Construction, visit the FAQ page. If you have questions or need assistance on how National Safety Compliance’s fall protection products can help with your Stand-Down event, contact us by emailing sales@nscemail.com, calling 877-922-7233, commenting below, or using our simple chat function on our website.
Recommended Fire Safety Training Procedures for Employers in 2020
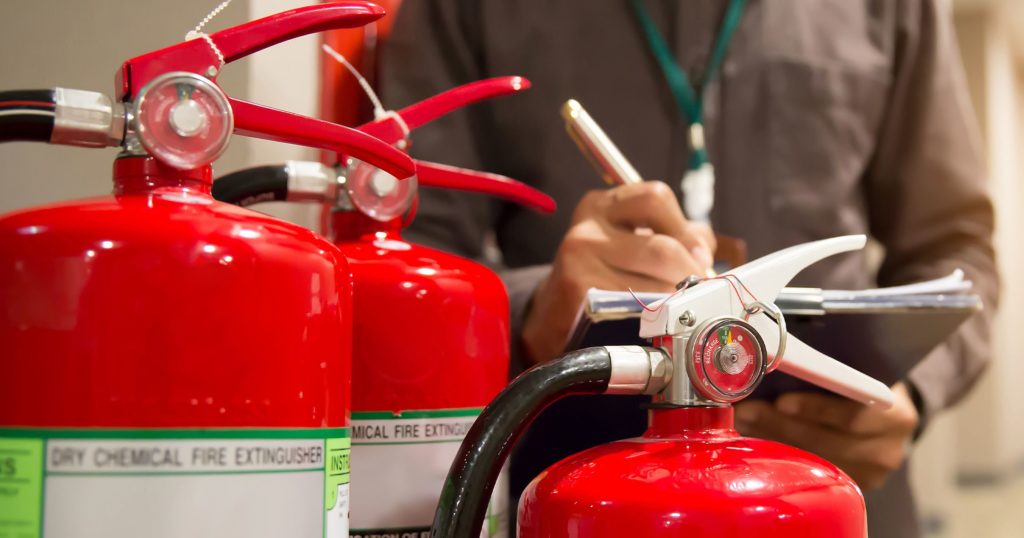
Since elementary school, the concept of stop, drop, and roll has been drilled into the young minds of children. Unfortunately, this is often where fire safety training and education ends. In order to properly respond to a fire, it is vital to further expand on this education, especially in the workplace.
Many employers feel as though fire safety and training is not something they need to be concerned with. It is easy to fall under the impression that you and your employees will never be impacted by a fire, but fires are a lot more commonplace than many assume.
The National Fire Protection Association (NFPA) estimates that the fire department responds to a fire every 24 seconds, a fire-related injury occurs every 35 minutes, and a fatality every 144 minutes in the United States. As a result of these frequent fires, the U.S. Fire Administration estimated losses of $26.5 billion in 2018.
This is time, money, and lives that are carelessly lost and, in most cases, could have been otherwise prevented with proper training on fire safety. Simply hanging an evacuation plan in the breakroom is not enough training to ensure the wellbeing of your employees. When an actual fire occurs, panic sets in, and reasonable action is often forgotten.
This onset of panic is due to a lack of training on the process of evacuation. The only way to prevent the injuries and fatalities caused by this is with proper training. The most powerful defense an employer can take against potential threats of fire is empowering their employees by preparing them with fire safety training and response.
Fire safety experts believe that training, knowledge, and practical experience can be the difference between a few small flames and an uncontrolled blaze. This is why at National Safety Compliance, we offer several different ways to train your employees on fire safety, including turn-key online training modules here on Online OSHA Training, as well as more traditional employer-led training programs available on DVD, USB, or Digital Access on OSHA-Safety-Training.net.
Guidelines for Workplace Fire Safety Training
Employer Fire Safety Responsibilities:
- Emergency Preparedness Plan: All employers should have a emergency preparedness plan in place in the event of a fire to outline all actions that employees should take. Plans should include response duties, coordination with fire departments, resources for the disabled, evacuation, emergency communication, and first aid provisions.
- Equipment: Must have the proper equipment and maintain it with proper inspections to ensure that they are working properly.
- Training: In order for employees to know how to work fire equipment like extinguishers and fire suppression systems it is important for them to have training on the proper operation of the equipment. This fire safety training should be provided by the employer.
Employee Fire Safety Responsibilities:
- Keep informed on safety procedures: Employees must pay attention to all safety procedures and details laid out in the Emergency Preparedness Plan. They have the responsibility to retain the information, participate, and confidently use the equipment. Signs and posters can help employees remember fire safety information.
- Participate in drills: It is vital to take any drills in your office building seriously regardless of whether or not they are an inconvenience, because they are designed to ensure you are fully prepared for an emergency.
- Understand your fight or flight options: In the event of an actual fire it is important to decide to either fight the fire if you are trained and confident in your ability to use an extinguisher or immediately exit the building and trigger the alarm if that is not already done. There is no time for indecision so this is important to consider beforehand.
Roles of Fire Safety Professionals:
It is important to be mindful of comparing your roles to those of professionals, especially in the event of an actual fire. Some jobs are important to leave to the professionals who are trained on how to handle particular situations and fire safety in a specific manner. These responsibilities include;
- Fire officers: Respond to emergency cases and provide immediate assistance.
- Fire warden: Clear the building of all people and ensure that no one is stuck inside by carrying out a thorough check and call.
- Fire marshals: Identify fire hazards at their workplace by keeping station equipment in great condition and updating records for incoming service calls.
- Fire inspectors: Work to prevent fires by providing regular inspections and helping employers to follow policies and report any needed changes, unsafe activities, or poor conditions.
Your employees can become a fire warden or marshal for your own office or building by going through fire marshal training and receiving their fire marshal certificate. These certificates last for 3 years and give you the ability to delegate responsibilities so you can effectively manage and prevent fires in the workplace.
Even though these responsibilities vary between employer, employees, and professionals, the person responsible for fire safety is still always the employer. They must communicate with staff to implement and maintain relevant fire safety procedures, prepare for an emergency, and supply fire safety information.
Types of Fires and Ways to Stop Them
To the untrained eye, fire is simply fire, but in reality, fire is actually broken down into different classifications. Knowing the differences between these fires is essential to fully understanding how to put them out.
Class A:
This type of fire sparks from wood, paper, trash, and other materials known as common fuel sources. These should be extinguished with water by streaming a continuous supply onto the source of the fire.
Class B:
These ignite due to explosions of flammable liquids or gasses. To extinguish these, simply deplete the oxygen supply by smothering the flames. Never attempt to put out a fire fueled by flammable liquids with water because it splatters and spreads the flames to give the fire strength instead of taking it away.
Class C:
These are known as electrical fires that erupt due to components like appliances and motors and are often seen in industries with lots of electrical power equipment. To extinguish these fires, cut the power and use non-conductive chemicals like carbon dioxide.
Class D:
This type of fire ignites combustible metals. Laboratories are often environments where these occur. Class D fires should be extinguished with dry powder agents like graphite powder or powdered copper. Similar to a Class B fire, you should never use water to attempt to extinguish it as water burns when it comes in contact with specific metals.
Class K:
These are cooking fires that are often seen in commercial buildings, restaurants, or company break rooms caused by ovens, stovetops, or appliances like microwaves. These should be put out with a fire extinguisher.
To further understand fire, it is important some of the main causes. These include but are not limited to;
- Heating
- Electrical equipment
- Candles
- Smoking
- Cooking equipment
- Faulty wiring
- Flammable liquids
- Lighting
These hazards of fires are used a lot in our everyday lives, making it seem like threats of fire are inevitable. Eliminating fire hazards doesn’t mean you have to throw out all your candles and never use another electrical unit, you simply have to follow safer guidelines while using them.
- If an electrical cord, unit or device becomes warm or overloaded disconnect any appliances attached
- Keep your work environment clean and ensure aisles, exits and self-closing doors are easily accessible
- Limit and enforce areas where smoking is allowed
- Avoid using space heaters for too long of a time period, as heating equipment is the second leading cause of fire deaths
- Keep candles one foot away from anything that can burn and never leave them unattended
- Do not leave any cooking equipment, even something as simple as a microwave, unattended and keep anything flammable such as dish towels or wooden spoons away from appliances
Proper use and Maintenance of Fire Safety Equipment
Simply having the equipment necessary to put out a fire is a great first step, but from there it is important to regularly care for and maintain the equipment. What good is a faulty fire extinguisher or fire alarm with a dead battery going to be in the event of a fire?
Proper Fire Extinguisher Usage and Maintenance
Extinguishers should only be used on smaller fires, as it is often not as effective with bigger fires. To properly work a fire extinguisher, you pull the pin while pointing away from you, aim towards the base of the fire, squeeze the lever slowly and evenly, and sweep from side-to-side. This is called the PASS System, and all employees should know these steps.
After using an extinguisher, it is important to replace or refill your extinguisher to ensure that it is ready in case of another emergency. Even if your extinguisher has not been used recently, they should be checked on a regular basis and tested by professionals every few years.
Fire extinguishers should be stored in areas that are accessible within seconds. You should have at least one fire extinguisher on each floor of your building or office space in easy to grab spots, near exits and in any kitchen areas.
Fire and Smoke Alarm Installation and Maintenance
Fire alarms and smoke alarms must first be properly installed. It is vital to ensure all of your alarms are installed correctly and in working order.
After installation, the battery in smoke and fire alarms should be replaced every year. There are life-long batteries, but these should be avoided for older alarms that do not work as well with these legacy products. The alarm itself should be replaced every decade and checked often.
Fire alarm guidelines are different for schools, hospitals, apartments, hotels, homes, and office spaces so it is important to check guidelines for your specific building.
Emergency Light Illumination
Exit and emergency lights are designed to provide you and your employees with a path to safety in the event of a fire. They are required in all commercial buildings with the intent to save the lives of those who use those buildings.
It is important to ensure that your emergency and exit lights illuminate properly because in the event of a power failure your employees will use those lights to get to safety. The fire code requires that your illumination works for a minimum of 90 minutes when called to do so. To ensure that your lighting will work when you need it most it is important to do a monthly test.
Keeping Records of Maintenance
Record keeping is another important aspect of fire safety, especially regarding fire inspections as inspectors often review these records. Because of this, employers should make and maintain documentation of all records associated with fire protection systems and services.
These records should be updated, stored, and organized for inspectors to see the documentation of regular inspection and maintenance for alarms, sprinklers, extinguishers, and any safety data sheets.
General Fire Safety Rules and Guidelines
To add to your knowledge beyond stop, drop, and roll, another great saying to keep in mind is ACT don’t panic. ACT stands for Assess the situation, Choose your response, and Take action.
These steps include identifying hazards and determining if any people are at risk, then limiting the response of those involved and taking individual action then sounding the alarm and evacuating. These are great steps to keep in mind when running through each part of the ACT acronym.
It is also important to be mindful of OSHA’s guidelines and local codes enforced by local fire safety professionals. Their guidelines are meant to prevent fires and are something you should consider and implement before it is too late.
Fire can present a serious risk to any business; killing and injuring employees, burning and damaging buildings, and creating a massive loss of equipment and funds. As a result, it is vital to provide fire safety training for your employees to ensure their safety in the event of a fire.
If you have any questions about fire safety training programs, please don’t hesitate to reach out. You can contact us by commenting below, using the chat function on our site, e-mailing us at sales@nscemail.com or call us at 877-922-7233.
Preparing for Possible OSHA Inspections in 2020

OSHA can show up at your work site for an inspection at virtually any moment, without any notice in advance. This is why it is so important for employers to always be ready for the possibility of an inspection.
The best way to prepare for an inspection is to ensure your worksite is up-to-date with current OSHA guidelines at all times. Worksites should be compliant for the type of industry and work that is performed.
While in most instances these inspections are done by chance, many conditions can prompt an OSHA inspection. These include a workplace death or catastrophe, complaints from employees, referrals from other workplaces or government agencies and follow-up inspections.
OSHA doesn’t target any one business or industry for inspections, but industries with high risk jobs are often prioritized for OSHA inspections based on reported fatalities and serious injuries.
OSHA conducts these inspections with the purpose of determining whether or not employers are striving to comply with proper OSHA standards that ensure employees have a safe and healthy workplace.
An OSHA inspection should not be a chore to prepare for. In reality, it is simply a way to further improve the safety of your workers in ways you should already be doing.

There are a lot of potential dangers in the workplace and OSHA’s standards simply ensure that no one has to come to work fearful of getting hurt. Preparing for potential OSHA inspections, regardless of whether or not you are chosen for an inspection, has lots of benefits for both the employer and employees and makes a safer and healthier workplace.
Many assume that it is important to be ready for OSHA inspections simply to save on any fines that may occur, but being ready for an inspection simply means that you are following the below steps to ensure the safety of your workplace
What to Expect From an OSHA Inspection
Setting your expectations for what will occur during an OSHA inspection and knowing what to do during an inspection will help ensure things run smoothly.

OSHA Inspector Arrival
When the inspector arrives, you should first confirm their identification. An OSHA ID includes the inspector’s photo, name and office. If you are unsure of whether the inspector is truly from the government, you can also call your local OSHA office to check.
The length of the inspection will depend on the size of your workplace as well as the focus of the review. Throughout the inspection you should conduct yourself in a professional manner. While OSHA inspectors will not accept any bribes, behaving in a friendly and calm way can help the progression of the inspection.
The inspection itself will be broken up into three phases; an opening conference, a walk-through of the facility and a closing conference.
Your Pre-Inspection Meeting
Select a meeting place for the opening conference, this should include the owner or safety manager along with an employee representative. The opening conference will allow the inspector to go over the specifics of the inspection to explain the parameters of the inspection, what will be inspected and if the inspection was prompted by any complaints.
At this time, the inspector will also ask for information on the work your worksite performs, the number of employees, names of those in leadership positions and contact information. They may also request files on injury and illness logs and record keeping.
The Walkthrough
The next step of the inspection is the walk–through. During this phase of the inspection, they are simply looking for any potential hazards that could lead to the death, illness or injury of an employee.
During the walk-through, the officer will point out any violations that need to be immediately corrected and check to ensure that all required OSHA posters and signs are properly posted. The inspector will try to minimize any interruptions to your work schedule and that of your employees throughout the walk-through.
The Closing Conference
Finally, the last phase of the inspection is the closing conference. This gives the inspector the opportunity to discuss any changes or courses of action that need to take place afterward and provide the employer with information on refuting citations and penalties.
How to Always be Prepared for an OSHA Inspection
Going through the process of preparing your workplace will not only ensure you are ready for any unforeseen inspections, but also reduce accident rates.
One of the biggest aspects of being prepared for an OSHA inspection is being organized and methodical in your recordkeeping. There should be a log of all illnesses, injuries and fatalities that occur while on the job including any documentation of emergency preparedness plans, evacuation procedures, lockout/tagout programs, exposure and medical records and material safety data sheets.
Beyond this, employers should also take steps forward in preparing for an inspection by assigning responsibilities. Delegating different roles to ensure there are specific employees educated on different aspects of the inspection such as preparing the proper paperwork and escorting the inspector around the building will be very beneficial in the case of an actual inspection.
Having a designated employee escort the inspector through the inspection also allows them to document everything the inspector does. This includes taking note of any conversations and observations as well as taking pictures of anything the inspector also photographs.
It is also helpful for this employee representative to bring a small dry erase board and marker to identify any objects that are hard to recognize in photos. This is helpful for your own recordkeeping and with the process of appealing any wrongful citations.

Most Cited Osha Regulations For 2019
- Hazard Communication 3,671
- Scaffolding 2,813
- Lockout/Tagout 2,606
- Respiratory 2,450
- Ladders 2,345
- Machine Guarding 1,743
Source: nsc.org
Understanding the Results
Any citations and penalties from the results of your inspection must be received within 6 months of the violation. If you have taken all of the above steps in advance and receive a citation you feel is not consistent with your workplace you can appeal it depending on the category it is listed under.
Citations are listed as either willful, serious, other-than-serious, de minimis, failure to abate and repeated. These different categories determine the likelihood of receiving adjustments to the penalty. For example, any willful citation will not receive an in good faith adjustment, whereas serious violations may have the penalty reduced based on the gravity of the penalty.
You’ll have the opportunity to appeal your claim in a conference with the OSHA Area Director and discuss any penalties and abatement dates. This gives you a chance to come to an agreement on how to eliminate the hazard moving forward. OSHA is very willing to work with you on this stage because their main priority is always eliminating hazards rather than giving penalties.
To avoid having to appeal any violations, be proactive and periodically check that you are compliant to eliminate any potential citations if you are inspected. There are a wide variety of resources that employers can utilize as they work towards preparing for an inspection. These include training software and supportive products and services.
Remember the old adage, “an ounce of prevention is worth a pound of cure.”? The same is true for your OSHA inspection. Taking proper precautions from the beginning, especially when safety is involved can save you from future problems. At National Safety Compliance, we feature easy and affordable solutions for your safety training. We offer complete training kits in DVD, USB, and via Instant Digital Access, as well as on-demand LMS. All of our training kits are available in English or Spanish, and include Program Outlines, Quizzes, Certificates, Training Logs, Wallet/ID Cards, Compliance Guides, PowerPoint Presentations, and a manual. You can use them as many times as you like, because all of the materials are easily printable.